Reducing Operational Costs with an Efficient WMS
Now that EOFY is behind us, it’s time to look forward and get operational efficiencies in order. We know managing and improving inventory management and processes can be tough, especially when trying to reduce labour costs and increase efficiency through warehouse operations. That’s where Datapel can help as you plan for the year ahead.
Reducing Operational Costs with an Efficient WMS
Hidden Inventory Costs
Carrying inventory is one of the biggest expenses for manufacturing and distribution companies. It ties up capital, takes up space and requires ongoing management. But finding the right balance – having just the right amount of stock on hand – is key to maximising your return on investment without compromising service levels.
Real-time inventory tracking within warehouse management systems (WMS) can improve inventory accuracy by automating data capture and using technologies like barcode scanners and RFID to maintain accurate stock levels and reduce errors from manual warehouse processes.
Business Intelligence: Reducing Operational Costs
Looking ahead one of the most powerful tools at your disposal for optimising inventory management is Business Intelligence (BI) software. BI systems like Datapel’s integration with BI4Cloud provide comprehensive visibility and reporting capabilities to transform how you manage inventory and achieve better business outcomes.
Here’s how BI software can help you cut operational costs as you plan for the future:
- Control Inventory Costs: BI analytics gives you insights to find cost savings. By optimising inventory levels you can ensure you’re not overstocking or understocking both of which can be costly.
- Improve Service Levels: BI software provides real-time information to eliminate out-of-stock and minimise shipment delays so your customers are happy.
- Better Inventory Asset Management: With real-time visibility into stock levels, locations and performance you can manage your inventory assets more effectively, reduce waste and increase turnover.
- Prevent Out-of-Stocks: You can avoid supply chain disruptions by setting optimal inventory targets based on historical data and classification schemes.
- Smart Planning and Optimisation: BI tools let you plan and optimise inventory based on sales, shipment and performance data so operations run smoothly and reduce delays.
- Reduce Warehouse Costs: BI software will identify inefficiencies and waste in your warehouse operations. By automating processes, optimising inventory management and using methods like cross-docking you can cut warehouse costs and overall supply chain efficiency and profitability.
These all add up to more informed operational decisions, less safety stock, more inventory control fewer lost sales and lower costs and time as you move forward.
Your Return Authority Workflow
Another area where costs can get out of control is in processing returns. The Return Authority workflow (also known as Credit Note or Stock Returns) is key to managing returns. Once a sales order is invoiced and marked as CLOSED any returned stock should be processed through a returns workflow. Streamlining this workflow will also reduce labour costs.
Here’s a quick overview:
- Returning Stock: Once a sales order is closed process returned stock through either Return Authority (linked to the original order) or Blind Return (unlinked).
- New Return Authority: Start the return process from the original sale order to ensure pricing and stock levels are accurate.
- Receiving Stock: Once a return is processed a new entry is created in the Receiving Register for processing. This ensures that returned goods are accounted for and stock levels are correct.
- Warranty/Repair Items: Allocate specific bin locations for service or warranty items so they can be tracked and managed.
- Damaged Stock: Even damaged stock should be received and disposed of correctly especially if you’re connected to an accounting system.
Managing returns saves time and reduces inventory discrepancies and unnecessary stock.
Supply and Demand: The Key to Success
At the heart of inventory management is balancing supply to meet customer demand. Sounds simple but many businesses struggle with this.
Here are some quick checks to ensure your inventory is aligned with your business goals as you move forward:
- Facility Costs: Are you using your space effectively? Is your stock split between locations or could consolidation be more efficient?
- Labour Overhead: Can you reduce your “cost of fulfilment” by reducing order pick/pack times? An efficient warehouse management system will streamline these processes.
- Finance Costs: Idle inventory ties up working capital. Review your purchasing workflows and consider direct shipping from suppliers to reduce these costs.
- Procurement and Transport: Review your freight costs—can you negotiate better deals with your carriers?
- Stock Accuracy: How accurate is your warehouse management system to your physical count? Regular cycle counts and a strict returns workflow are key to maintaining accuracy.
- Management & Information Systems: Are you getting the most out of your WMS? Integration with trading partners, process automation and customisable reporting can all save costs.
- Warehouse Layout: Is your warehouse layout designed to minimise employee travel time and identify bottlenecks? A well-designed layout will improve operational efficiency and reduce labour costs.
- Warehouse Space: Are you managing your warehouse space effectively? Use cross-docking and advanced WMS to free up space, increase productivity and reduce labour costs.
The Secret to a Successful Warehouse
Successful warehouses follow a few simple rules:
- Integration: A fully functional WMS requires buy-in from internal teams and external partners. Make sure everyone is on the same page to get the most out of your WMS.
- Be Adaptable: Your business should be flexible enough to adapt to changing customer demand and market conditions. A good WMS will help you stay ahead of these changes.
- Use Data to Serve Your Customers: Accurate delivery times are key to customer satisfaction. Make sure your WMS is providing the data to keep your customers informed.
- Staff Buy-In: Your staff need to understand why the WMS is important and where they can make a difference. A trained team is essential to get the most out of your system.
- Optimise Warehouse Operations and Processes: Analysing and optimising warehouse operations and processes will significantly improve efficiency and reduce labour costs. Use performance metrics and data analytics tools to identify bottlenecks and areas for improvement and make better decisions and overall performance.
These guidelines apply to any type of warehouse, including manufacturing, distribution, or retail.
Why Datapel?
Datapel is an Order and Warehouse Management System that helps businesses save costs, increase efficiency and control inventory. As you move forward make sure you review your warehouse operations and make the changes to ensure long-term success. Datapel can benefit a warehouse or distribution centre by optimising processes to enhance productivity and efficiency.
By leveraging Datapel’s powerful tools, you can reduce operational costs, streamline processes, and position your business for continued growth in the year ahead.
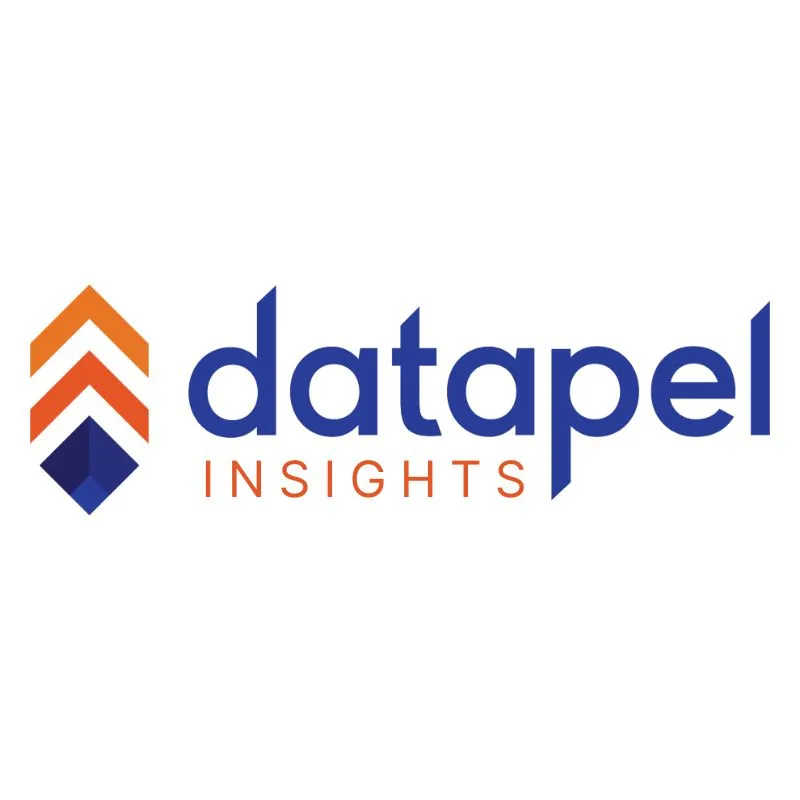
In my role, I oversee the development of insightful blogs that delve into the intricacies of warehouse management. Each piece reflects my dedication to empowering businesses through informative content. Through my team’s extensive experience in the industry, we aim to bring clarity to the complexities of WMS, helping businesses make informed decisions.
Join me on a journey through the ever-evolving landscape of warehouse technology as we explore the latest trends, industry insights, and practical tips to streamline your operations. Feel free to connect, and let’s embark on a collaborative exploration of how WMS can redefine your business efficiency.
Cheers to innovation, efficiency, and the exciting world of warehouse management!