Case studies
Our Warehouse Management System Case Studies
See how Datapel has supported businesses like yours to successfully and smoothly implement a powerful, efficient and easy-to-use WMS – even during rapid business growth or times of immense change.
Streamline your order management with advanced customer and supplier pricing
Best practice inventory control improves order fulfilment accuracy and increases productivity
Detail product tracking options with multiple user defined fields, attachments and images
Introduce barcode scan, print, and label to reduce error rates and avoid missed or extra items
Get full visibility in your warehouse workflow with user action audit trail, reports, and dashboards
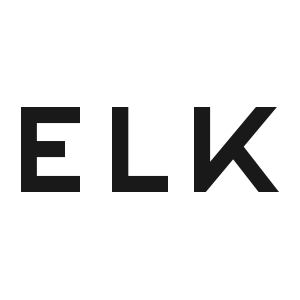
As a leading fashion and accessories brand supplying domestic and overseas stores, ELK identified a growing online e-tailing opportunity. They required a WMS that could keep up with the fast—often next day—delivery of online orders direct from their Melbourne warehouse.
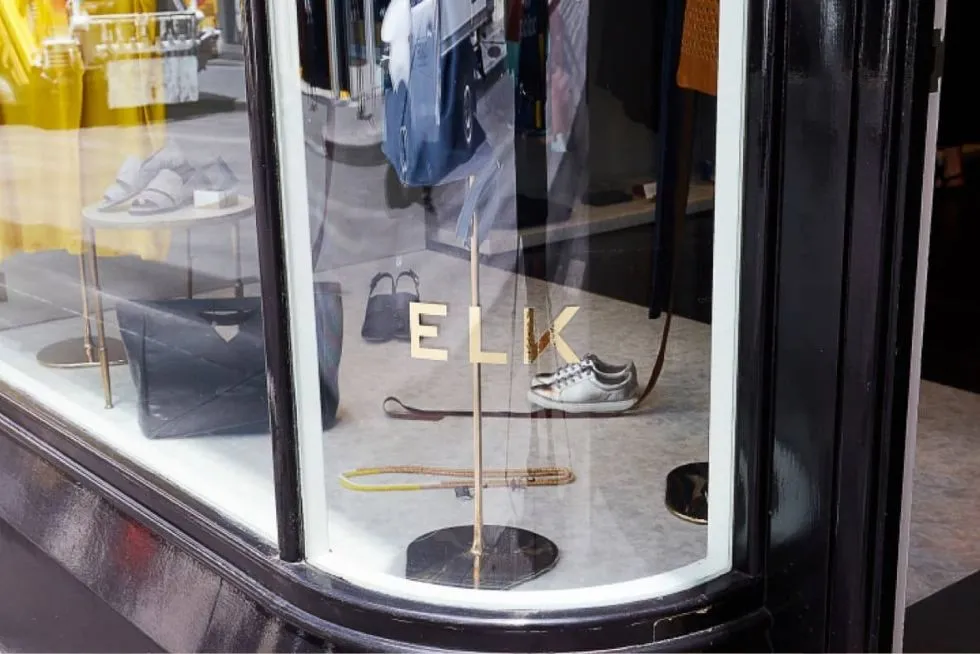
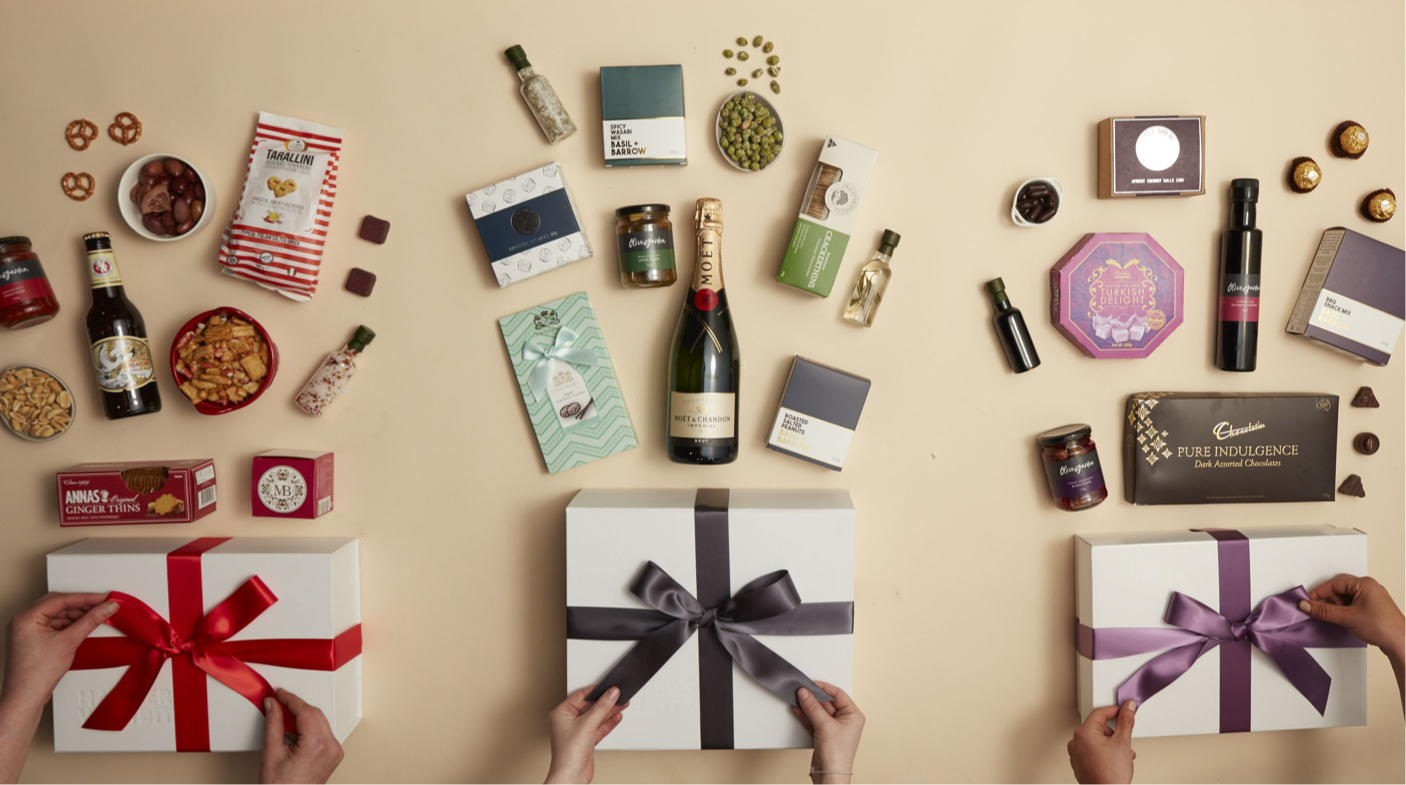
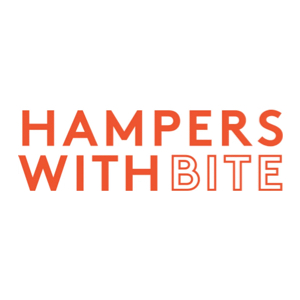
This rapidly growing business was using a legacy, on-premise WMS that lacked flexibility. They were unable to extend ERP integration or offer basic MRP features. Hampers With Bite required a new solution accessible from anywhere prior to the peak Christmas production and distribution season. Additionally, parallel operation of the existing legacy system needed to be maintained during the transition to manage overall business risk.
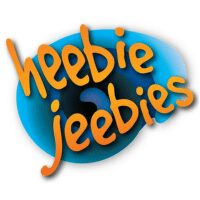
Heebie Jeebies noticed multiple errors in accounts and stock levels due to double-entry and needed a solution that would reduce errors and improve accuracy. Datapel Cloud.WMS was implemented very quickly and they saw instant savings in labour as well as improved efficiency. Ultimately it increased turnover by 4-5 times with the same number of staff they had before implementation.
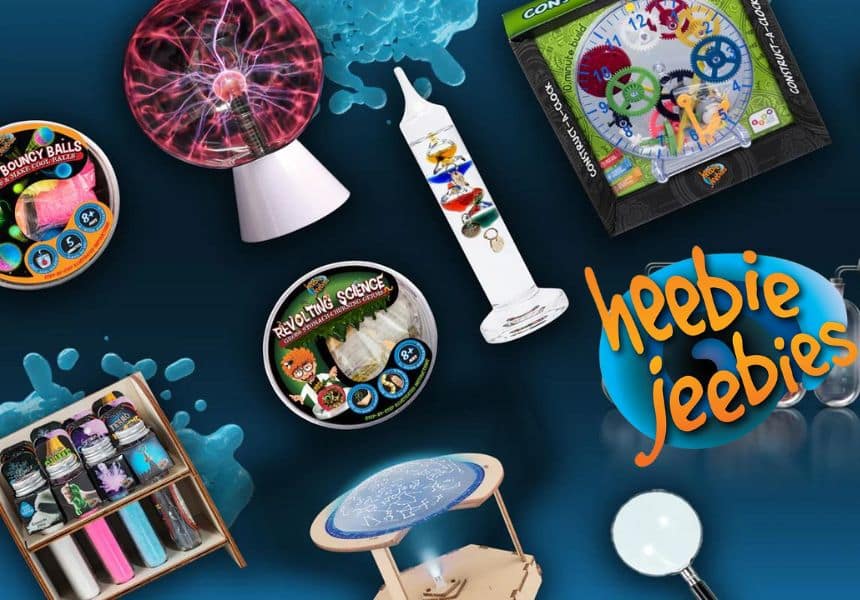
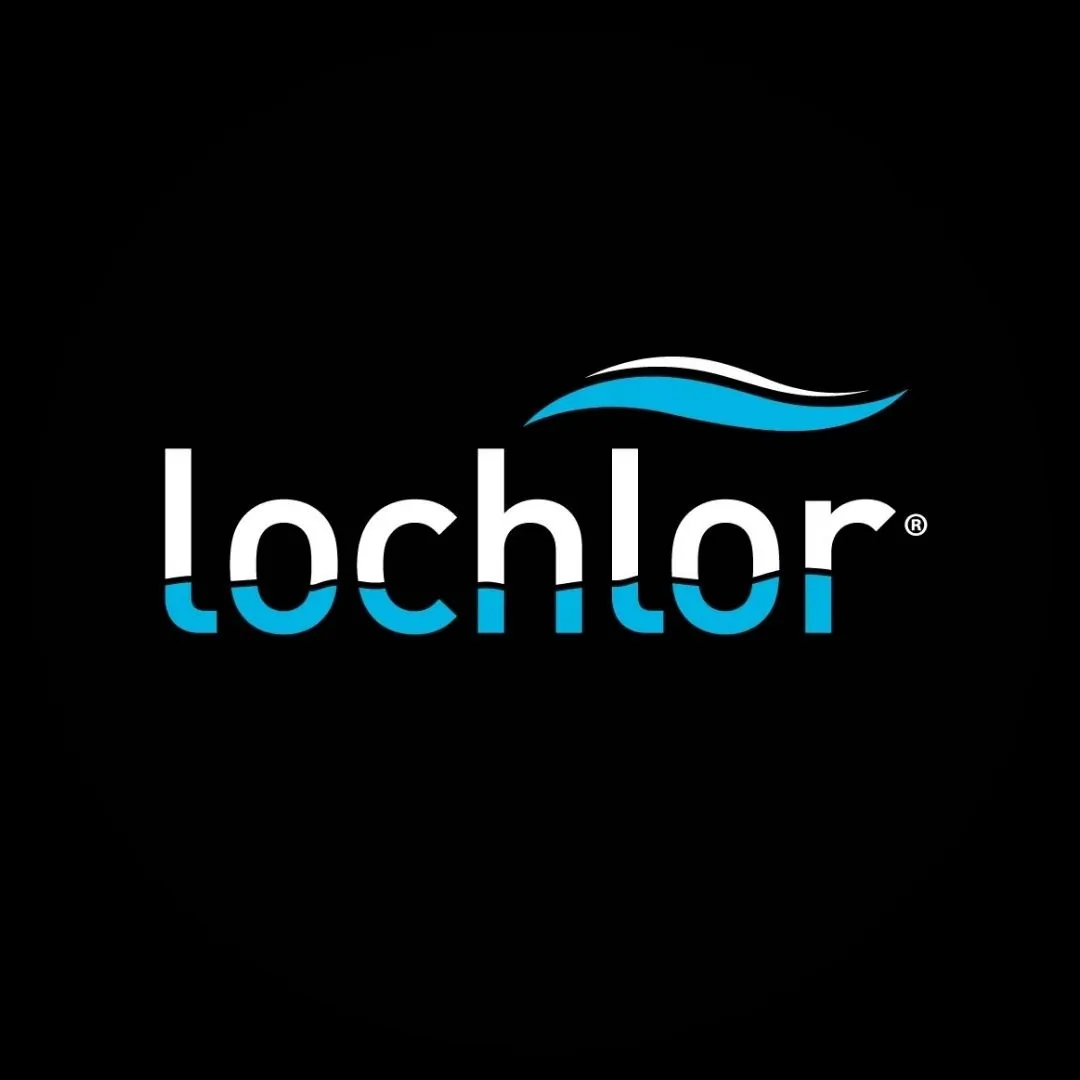
Lo-Chlor Chemicals, based in Sydney, Australia, is a leading manufacturer of chemicals for swimming pool maintenance. As a manufacturer, they faced challenges in tracking inventory, managing orders, and ensuring timely deliveries. Seeking a solution that integrates seamlessly with MYOB, Lo-Chlor turned to Datapel Systems to transform their operations.
“We just didn’t expect it to be that much of an improvement… even with our best pickers… and now we can multi-skill our entire staff and be even more efficient”
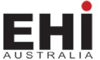
EHI
EHI Australia relied on a good paper-based picking system using incentives for high performing employees. However, the ever-present need to reduce overall error rates—and increasingly strict SLAs with major customers—dictated the need to improve accuracy and minimise penalty charges due to pick errors. With rapid business growth, there was a need to modernise the warehouse management system and scale operations.
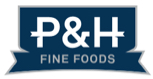
P & H Fine Foods
P & H Fine Foods needed an inventory solution that could adapt following the outbreak of the Covid-19 virus. As a supplier of catering to major airlines, P & H Fine Foods had to rapidly pivot production due to a sharp drop in sales volumes. The management team realised three things were critical to business survival and long-term success: flexibility, access from anywhere via web browser, and real-time scanning capability.
“With Datapel DataPOS we get a flexible POS experience that knows our client and makes the checkout process simple.”
See how Datapel works for you
Leading organisations use Datapel for visibility into their warehouse operations
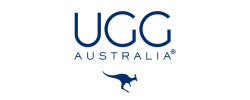
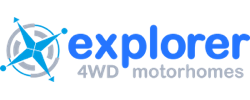
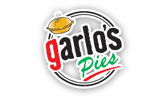
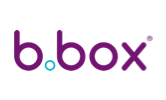
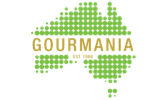
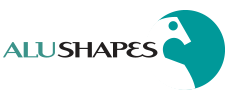
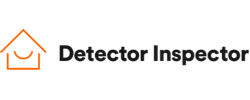
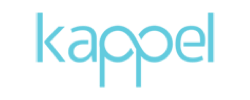
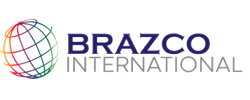
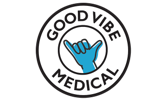
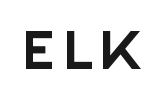
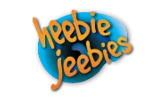
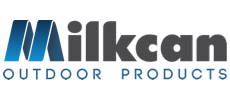
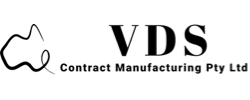