A Complete Guide to Effective Cross Docking
Contents
In supply chain operations, speed and efficiency is more important than ever. Cross docking is a logistics strategy that can save you time and money.
This guide covers the ins and outs of cross docking and how to make it work for you.
Many industries from big retailers to small manufacturers are using cross docking to reduce warehouse costs and delivery times. Whether you’re just starting out or looking to improve your current operations this guide has everything you need to know about cross docking from the basics to advanced tips to get the most out of it.
Before we get into the how to, let’s start with the basics: What is cross docking? This will set us up to go deeper into the processes and benefits and then we’ll get into the scenarios in the next sections.
What is cross docking?
Cross docking (CD) is a logistics process where inbound freight is transferred to outbound vehicles without the need for storage or handling in a warehouse. A cross dock warehouse is a specialised facility designed for the efficient transfer of goods from inbound to outbound shipments, no long term storage. The goal of cross docking is to speed up the distribution process and reduce lead times by eliminating intermediate storage and handling.
In cross docking incoming freight is delivered to a cross docking facility where it’s sorted and sent to outbound vehicles for delivery to the final destination. The cross docking model is about moving freight from receiving docks to outbound shipments with minimal storage, it’s efficient and fast. The process is designed to be cost effective and reduce time and resources to store and handle the materials.
Cross docking can be used in many industries such as retail, manufacturing and distribution. A cross dock terminal is a key facility where goods are received, sorted and dispatched quickly without long-term storage. It’s ideal for companies that need to move large volumes of goods quickly and efficiently or for companies that operate on a just-in-time inventory.
What do you need to be good at cross docking?
To be good at cross docking you need:
- Planning: Cross docking requires planning and coordination to get the incoming freight to the right outbound vehicles on time. This may mean working with your suppliers to schedule deliveries and coordinating with the transportation companies to get the right vehicles to receive the freight. Cross docking facilities with multiple dock doors can facilitate the quick transfer of goods between incoming and outgoing trucks.
- Sorting and segregation: Incoming freight needs to be sorted and segregated to the final destination to get it to the right outbound vehicles. This may mean using barcode scanners or other tracking technology to identify and route the freight. The design of the cross docking facility should have multiple inbound and outbound doors to maximise efficiency and space.
- Transportation: Cross docking relies on transportation to get the freight from the cross docking facility to the final destination. This may be trucks, planes or ships depending on the distance and mode of transport. The inbound dock is critical to get finished goods off the incoming transport and ready for outbound shipment.
- Communication: Communication is key to cross docking as it ensures everyone involved in the process knows what’s happening at each stage. This may mean using real time tracking systems to keep everyone informed of the location and status of the freight.
- Flexibility: Cross docking requires some flexibility as there may be unexpected delays or changes in demand that require adjustments to the process. You need to have a plan B.
Cross Docking Benefits
Cross docking has many benefits that can improve your logistics and supply chain. One of the biggest is the reduction in inventory holding costs. By minimising the time products are in storage you reduce the risk of damage, loss or obsolescence. This saves you money and ensures products are fresher and more relevant to the customer when they arrive.
Also, cross docking can save you big on warehousing costs. Since products are not stored for long periods the need for large warehouse space is reduced. This can free up resources and allow you to repurpose your distribution centre for other critical functions.
Another big benefit is faster delivery times. By getting goods from inbound to outbound shipments quicker cross docking reduces lead times and gets products to their destination faster. This is especially important for high-volume or time-critical products as it allows you to respond quickly to changes in demand and stay ahead of the competition.
Cross Docking in Supply Chain Management
In supply chain management cross docking is a key strategy to improve efficiency and reduce costs. By consolidating shipments and minimising handling times cross docking simplifies logistics and makes the whole supply chain more agile.
One of the biggest benefits of cross docking in supply chain management is a reduction of errors, damage or loss in transit. By reducing the number of touchpoints and handling steps cross docking minimises the chance of mistakes and ensures products are handled with care throughout the process.
Also, cross docking allows you to optimise your supply chain by having lower inventory levels. This reduces the costs of holding inventory and improves cash flow so you can invest in other areas of growth.
Faster delivery times are another big advantage. By eliminating intermediate storage cross docking gets products from suppliers to customers quicker, overall customer satisfaction. In a competitive market being able to deliver products quickly and reliably is a big differentiator.
What are the 5 types of cross docking?
Several types of cross docking can be used in different situations:
- Direct cross docking: In this method, incoming goods are transferred directly to outbound vehicles without any intermediate storage or handling. This is the most efficient method as it eliminates intermediate storage and handling but requires careful planning and coordination to ensure the right goods are sent to the right outbound vehicles. Direct cross docking is the most efficient as it requires minimal storage space and allows for rapid turnaround of shipments.
- Pool cross docking: In this method incoming goods are stored in a central location before being sent to outbound vehicles. This allows for some flexibility in the cross docking process as goods can be stored and sorted over a longer period.
- Break-bulk cross docking: This involves breaking down large shipments into smaller units that can be handled and sent to their final destination. This is often used for oversized or bulky goods that can’t be sent as a single unit.
- Consolidation cross docking: In this method, smaller shipments are combined into one larger shipment which is then sent to its final destination. This reduces transportation costs and lead times by consolidating multiple shipments into one load.
- Distribution cross docking: This involves sorting and sending goods to multiple locations not just one. This is often used in the retail or eCommerce order fulfilment process, where orders need to be fulfilled from multiple warehouses or distribution centres.
Cross Docking Software and Technology
Software and technology play a big role in optimising cross docking. Advanced cross docking software gives businesses real-time visibility into inventory levels, shipment tracking and delivery schedules. This level of visibility is key to coordinating inbound and outbound shipments and making sure the right products are sent to the right destinations.
Automation technology also helps to streamline cross docking. Conveyor systems, sorting machines and robotic picking systems can reduce labour costs and increase the speed and accuracy of the cross docking process. This allows businesses to handle large volumes of goods quickly and efficiently and more of the benefits of cross docking.
By using these tools businesses can optimise their cross docking, reduce errors and overall efficiency. This means cost savings and the ability to meet customer demands quicker and more accurately.
What impact does cross docking have on a warehouse?
Cross docking can do a lot to a warehouse as it eliminates intermediate storage and handling of goods within the warehouse. This means:
- Shorter lead times: Cross docking can reduce the lead time from supplier to end customer as it eliminates intermediate storage and handling. A distribution centre can be a sorting facility where goods are unloaded from incoming shipments and sent to multiple locations without storage.
- Lower storage costs: Cross docking reduces the need for warehouse storage as goods are not stored within the warehouse. This means lower storage costs and potentially the warehouse can be repurposed for something else. Reducing intermediate storage cross docking can reduce overall supply chain costs.
- More efficient: Cross docking helps to streamline the distribution process as it reduces the number of steps to get materials from supplier to end customer. This means the warehouse can be more efficient and require less labour and resources to run. Implementing cross docking as a supply chain strategy can be more efficient and cost savings and meet rising customer demands and competition.
- Better customer satisfaction: By reducing lead times and increasing efficiency cross docking can get products to customers faster and more reliably.
But do remember cross docking also has its downsides, new infrastructure and technology to invest in and potential disruption if not managed properly.
With companies like Amazon investing heavily in cross docking you should be doing the same and taking a page out of their book for maximum efficiency.
FAQs
What is cross docking?
Cross docking is where goods are moved directly from inbound to outbound transport without storage. It’s all about minimising handling and storage time by moving products through a cross dock terminal quickly, saving on warehousing costs and reducing delivery times.
When should you use cross docking?
Cross docking is when speed and efficiency is key, such as for time critical goods, high demand products or products that don’t need storage. It’s great for retail, eCommerce and manufacturing industries looking to reduce warehouse costs, simplify distribution and be more responsive to demand changes.
What is the cross docking process?
The cross docking process involves receiving products at an inbound dock, sorting them by destination and loading onto outbound vehicles for final delivery. It requires planning, coordination and often real-time tracking to get products moved without storage delays.
What is an example of cross docking?
A example of cross docking is in retail distribution: a supplier delivers a shipment of products to a retail distribution centre. Instead of storing the products, the centre sorts and loads the products onto trucks for individual stores. This means shelves get restocked quicker and less warehouse space is required.
What are the advantages of cross docking?
Cross docking gives you lower warehouse costs, faster delivery times, reduced inventory holding costs and more efficient supply chain. By reducing storage and handling steps cross docking helps you save costs and be more responsive to customer demand, better overall.
Conclusion
In summary cross docking is a powerful logistics strategy that offers many benefits to businesses, reduced inventory holding costs, lower warehousing costs and faster delivery times. By optimising cross docking with advanced software and technology businesses can be more efficient, cost savings and better customer satisfaction.
As demand for fast and efficient delivery grows cross docking will play a bigger role in supply chain management. Get ahead of the game, be more competitive and meet the evolving needs of your customers with cross docking.
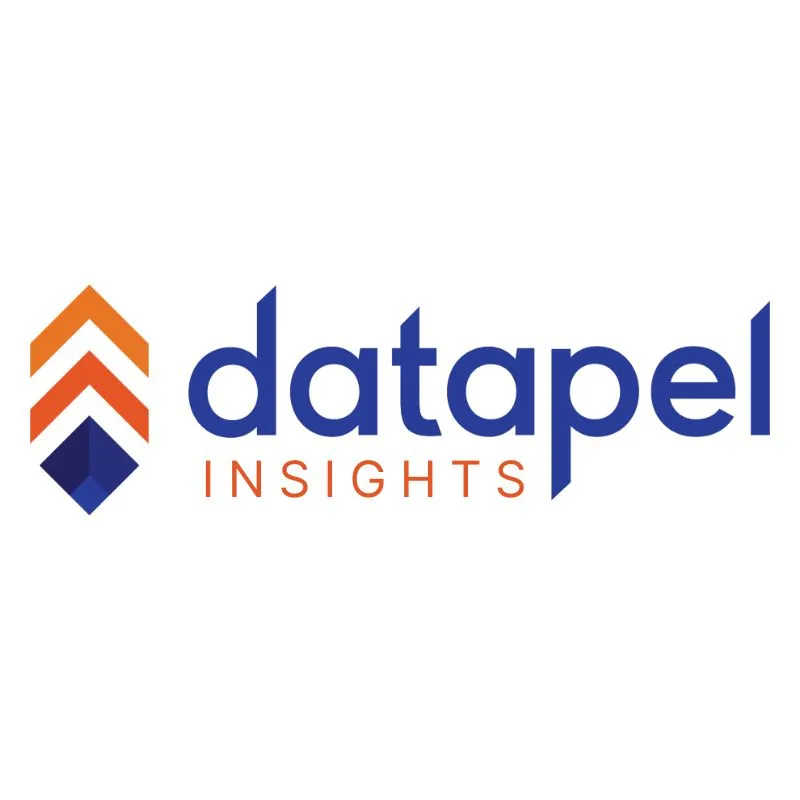
In my role, I oversee the development of insightful blogs that delve into the intricacies of warehouse management. Each piece reflects my dedication to empowering businesses through informative content. Through my team’s extensive experience in the industry, we aim to bring clarity to the complexities of WMS, helping businesses make informed decisions.
Join me on a journey through the ever-evolving landscape of warehouse technology as we explore the latest trends, industry insights, and practical tips to streamline your operations. Feel free to connect, and let’s embark on a collaborative exploration of how WMS can redefine your business efficiency.
Cheers to innovation, efficiency, and the exciting world of warehouse management!