How to Maximise ROI with Warehouse Management Software (WMS)
Contents
What is warehouse management software (WMS)?
Warehouse management software (WMS) is a cloud-based system that helps businesses manage warehouse operations and track inventory. It includes features such as receiving and shipping management, inventory tracking, barcoding, real-time data analysis, and integrations with other platforms like enterprise resource planning(ERP) and transportation management systems(TMS). These features provide seamless connectivity and full supply chain visibility.
A warehouse management system supports inventory tracking and data capture using technologies such as RFID and mobile devices like smartphones, tablets, and barcode scanners. These tools are essential for warehouse staff. It also improves order picking methods—including batch, individual, wave, and wave-less picking—to enhance efficiency and reduce fulfilment times.
Labour management tools in a warehouse management system often include task automation and voice processing. These help increase productivity and provide real-time visibility. The system manages storage locations, makes better use of warehouse space, and can incorporate solutions like automated storage and retrieval systems (AS/RS).
WMS also streamlines packing processes by using technologies such as barcode scanning and RFID. This ensures accurate inventory control and faster shipping.
The goal of warehouse management system is to improve efficiency, accuracy, and overall warehouse operations.
Key Features of Warehouse Management Software
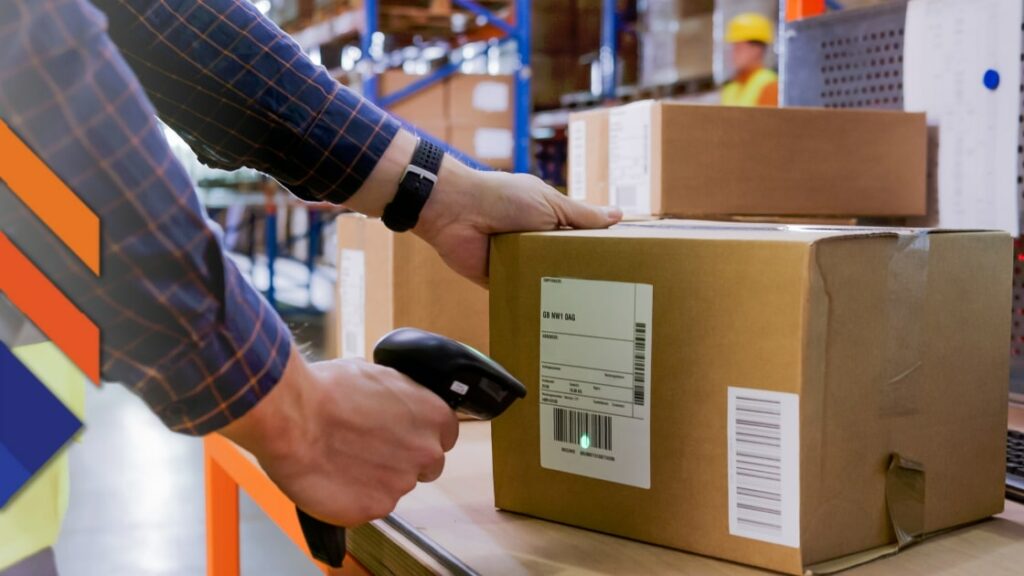
A robust warehouse management system (WMS) helps streamline operations and improve inventory management. Key features include:
- Inventory Tracking: Monitor stock movement, manage storage locations, and maintain accurate stock levels across sites.
- Automated Data Capture: Use barcode scanning and RFID to reduce manual entry and human error.
- Labour Management: Allocate tasks, track productivity, and automate job assignments.
- Real-Time Visibility: Make informed decisions quickly and respond to changes in customer demand.
- System Integration: Connect with ERP and TMS systems for end-to-end supply chain visibility.
- AI and Machine Learning: Predict demand, optimise picking routes, and spot potential disruptions.
- Multi-Warehouse Support: Manage inventory across multiple warehouses and scale with business growth.
Using these features, businesses can improve operations, cut costs, and boost customer satisfaction.
Types of Warehouse Management Systems
When choosing a warehouse management system, you’ll find a few types available:
- Standalone WMS: Installed on-site with high customisation and control, suited for unique needs and existing setups. These systems can have higher upfront costs.
- Cloud-Based WMS: Popular for their low setup costs, quick implementation, and scalability. These systems are accessible anywhere with an internet connection and reduce IT workload.
- Integrated WMS within ERP or SCM Systems: Combine warehouse management with other functions like finance, procurement, and transport for full supply chain visibility.
To choose the best warehouse management system, consider the complexity of your inventory management, warehouse size, future growth, and available IT resources. Aligning the right system with your goals helps improve efficiency and control costs.
4 Areas to Help Build Your Business Case for WMS
When investing in a warehouse management system, management will want to know the cost and how it leads to savings. Showing a clear ROI is key.
Most businesses that implement a WMS recover their investment within 8 to 12 weeks. Here are four core areas where you can expect strong returns:
1. Labour Savings
Labour is one of the biggest costs in warehouse operations. A major time drain is walking around the warehouse to pick products.
Warehouse management software reduces this by optimising picking paths and assigning tasks based on item locations. This cuts travel time—often up to 50%—and boosts productivity. Features like directed picking and wave picking improve accuracy and reduce manual planning.
A WMS also automates goods receiving. It checks deliveries against purchase orders and helps with quick, accurate intake.
2. Onboarding
High staff turnover in warehouses makes training time and costs a concern. A WMS with intuitive design and automation helps new hires get up to speed quickly.
Barcode scanning removes guesswork and reduces picking errors, even if new staff aren’t yet familiar with the products.
3. Increase Productivity
Staff shortages are affecting many supply chain businesses. A warehouse management system helps your team achieve more in less time.
It automates data entry, reduces paperwork, and makes warehouse data accessible on mobile devices. Staff can view, update, and act on information from anywhere in the warehouse.
With centralised data and digital tools, your team can spend less time on admin and more on value-adding tasks.
4. Reduce Errors
Errors in picking and shipping affect customer satisfaction and can lead to penalties—especially if you work with major retailers.
A WMS brings structure to your operations. It helps reduce fulfilment errors and avoid costly mis-shipments.
By introducing checks and balances, your team can get orders right the first time. Features like wave scheduling also help ensure orders are packed and shipped correctly and on time.
Warehouse Metrics and Analytics: Measuring ROI
To make the most of your warehouse management system, tracking performance is essential. Key metrics include:
- Inventory Accuracy
- Labour Productivity
- Order Fulfilment Rates
- Inventory Turnover
- Order Cycle Time
- Perfect Order Index
Using real-time data, you can identify gaps, fix issues, and continuously improve.
Built-in analytics and reporting help you monitor warehouse operations and make data-driven decisions. These insights lead to cost savings and improved service.
Warehouse Management Software that Generates ROI
A warehouse management system can pay for itself quickly—but only with proper use.
Ongoing training ensures your team knows how to get the most from the system. The right provider will support you after go-live and help you maximise the software’s features.
Measuring performance in real time is also critical. Without it, you can’t spot inefficiencies or track progress.
Read the case study: How Heebie Jeebies quadrupled in size after implementing Datapel Cloud.WMS
Final Thoughts
With the right warehouse management software, you can improve efficiency, reduce errors, and make more informed decisions—all of which contribute to a stronger bottom line.
If you’re exploring whether a warehouse management system is the right move for your business, Datapel Cloud.WMS is built for growing operations that need better control without the complexity.
“What we didn’t expect was the massive impact Datapel had across our business processes — especially reporting.”
– Sarah Marriott, Financial Controller, SC Botanicals
We offer a tailored solution backed by real support and experience in warehousing, wholesale, manufacturing, and eCommerce environments.
Book a demo to see what Datapel Cloud.WMS could do for your business.
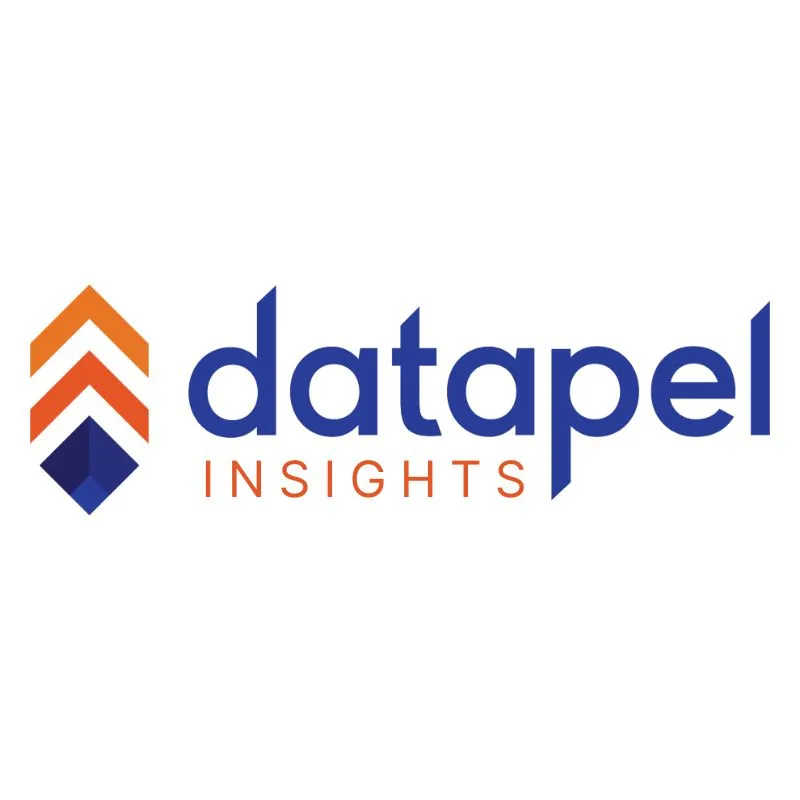
In my role, I oversee the development of insightful blogs that delve into the intricacies of warehouse management. Each piece reflects my dedication to empowering businesses through informative content. Through my team’s extensive experience in the industry, we aim to bring clarity to the complexities of WMS, helping businesses make informed decisions.
Join me on a journey through the ever-evolving landscape of warehouse technology as we explore the latest trends, industry insights, and practical tips to streamline your operations. Feel free to connect, and let’s embark on a collaborative exploration of how WMS can redefine your business efficiency.
Cheers to innovation, efficiency, and the exciting world of warehouse management!