6 Pain-Killing Tips to Streamline Inventory Control
Contents
Picture this: On top of your main products, you’ve just launched a new line. With the added SKUs, individually tracking each item is trickier, but your warehouse is big enough to handle the extra inventory. And your eCommerce store processes orders and collects data automatically, so you’ll always have a pulse on what’s selling and what needs restocking.
But when the orders start pouring in, you find yourself overwhelmed by the sheer number of items that need to be tracked, moved, and monitored.
- Your warehouse employees are having trouble locating items quickly.
- You’re losing count of which items are selling and where.
- You aren’t sure how to keep up with demand without making mistakes.
And after a few days of increased website traffic, you realise that you miscalculated and let some items go out of stock too soon.
This is one example of the countless challenges that come with inventory management. To keep those shelves stocked, you need a process for streamlining the supply chain from source to shelf.
That’s where efficient inventory control comes in—with the right system, you can manage your warehouse better, optimise stock levels, and make sure your products are always within reach.
What is Inventory Control, Exactly?
Inventory control is the complete process of tracking and managing stock to optimise its worth.
Several processes go into inventory control, including:
- Tracking purchase orders
- Forecasting future inventory needs
- Setting reorder levels based on customer trends
- Organising warehouse space efficiently
- Keeping accurate records of stock levels and movements
- Granting access to employees while maintaining security standards
- Loss and error prevention
Because it plays such a critical role in effective ordering, production planning, and cash flow management, inventory control is a critical aspect of running any retail or eCommerce business.
Inventory managers need to understand the general principles of warehouse management and the nuances of their specific product lines and customer behaviours.
Detailed analysis of past sales data can help drive demand forecasts which are essential for business growth.
How to Streamline Inventory Control: 6 Essential Tips
If you sell physical products, you already have some sort of inventory control process in place, whether you realise it or not. Every business that works with physical goods needs to keep track of stock, from the minute it’s purchased to the moment it’s sold.
But if you want to maintain a lean inventory system and ensure your products are always in stock, then manual processes won’t cut it.
Fortunately, there are many ways to streamline inventory control so that it becomes easier and more efficient. Here are six tips to get you started.
1. Invest in a Inventory Management System (IMS)
An inventory management system (IMS) is the Holy Grail of inventory management. Using an automated system, you can track inventory movements in real time, analyse your stock levels, and optimise your warehouse space.
An inventory management system also makes it easier to manage extensive inventories and allows for more accurate demand forecasting.
Benefits of using a IMS include:
- Decreased Labour Costs: When software carries out the tasks that your employees used to perform manually, your warehouse staff can focus on more essential tasks that require their attention (e.g., packing and shipping).
- Inventory Accuracy: Nearly half of the issues in retail and warehousing are the result of human error. IMS eliminates human error, ensuring that your inventory is always accurate—no more counting items twice or misplacing products.
- Improved Order Fulfilment Times: With an automated system, you can easily locate products and get them ready for shipment faster.
- Data and Actionable Insights: IMS gives you comprehensive reports on your inventory levels and movements, helping you make strategic decisions about stock replenishment and resource allocation.
- Improved Supply Chain Relationships: When it’s easier to stay in contact with suppliers and vendors, you can collaborate with them more efficiently and eliminate delays in your operations.
- Integrations: E-commerce, omnichannel (i.e., selling through multiple sales channels), and accounting are among the many tools and platforms that IMS can integrate with.
Although you could manage your warehouse on your own using spreadsheets and manual processes, the relative ease of a modern IMS makes it the best choice for most businesses.
If you’ve exhausted all your manual efforts and still can’t seem to streamline inventory control, then investing in a IMS is the first step you should take.
2. Automate Reordering
An inventory reordering system is a method of automatically replenishing stock when it reaches a predetermined low level. It enables businesses to reduce the time and effort spent on manually tracking and ordering inventory, freeing up resources for other tasks.
The typical automated reordering system involves setting a threshold for each item in the inventory. When an item drops below the threshold, a notification is sent to you or your staff, who then purchase additional supplies of that product (unless the software handles it).
Depending on the size of your business, you may be tempted to manage stock levels manually. But manual reordering leaves room for forgetfulness and doesn’t allow for flexibility or scalability.
Datapel’s IMS seamlessly integrates with web stores, and you can set up automated reordering triggers for each SKU. Reorder points can also be customised for each product, so you won’t have to worry about any surprises when inventory is low.
3. Optimise Warehouse Layout
Your warehouse layout has a significant impact on how efficiently goods get into, out of, and around your facility. A well organised warehouse design maximises warehouse productivity and ensures the best use of the available space.
There are 5 different spaces to consider when optimising your layout:
- Storage and inventory
- Inbound receiving dock
- Picking and packing areas
- Outbound shipping dock
- Employee area
The area designated for storage and inventory is the most important factor to consider when creating an optimised layout because it sets the foundation for efficient operations.
There are three main warehouse flows: U-shaped, I-shaped, and L-shaped
U-Shaped Flow
In the U-shaped warehouse flow, components are arranged in a half-circle with shipping and receiving next to each other while storage is kept in the middle.
The U shape keeps most warehouse traffic on the outside of the warehouse and reduces the risk of accidents and bottlenecks. The U-shaped layout also makes it easier to access goods stored in the middle of the warehouse, saving time on picking orders.
Since shipping and receiving share the same side of the building, incoming and outgoing packages require less space and employees can quickly move inventory into and out of the building.
One disadvantage of this flow is that if there is too much action between the shipping and receiving departments, congestion can occur.
I-Shaped Flow
The I-shaped flow is best for companies with large warehouses (e.g., enterprise eCommerce brands) because its in-and-out workflow is designed for high production volume.
The I-shape warehouse design is in assembly-line format, moving in a straight path from receiving to shipping, and vice versa. Its long hallways utilise the whole length of the warehouse while limiting back-and-forth movement.
The main disadvantage to this shape is that it requires plenty of loading and unloading space on each side of the warehouse building, which may increase costs when either choosing a warehouse or purchasing docking equipment.
L-Shaped Flow
The L-shaped flow is a hybrid of the U and I shapes, blending both layouts together. The warehouse moves in an L-shape from receiving to shipping, within the same building or separate buildings.
The L-shaped warehouse flow is not chosen as often as the other two flow types. Usually, it is only used to accommodate L-shaped buildings.
Like the I-shaped flow, the L-shaped layout requires plenty of space on both sides of the warehouse. It keeps inbound and outbound docks on opposite sides, which streamlines the entire process.
That said, it requires a lot of space to run efficiently, which is why it’s not the most popular option.
4. Create a Barcode System
Barcodes are an essential part of warehouse operations, as they allow for quick data capture and error-free processes. They can be used to track inventory, record order picking and packing, and manage returns.
Companies use barcodes at several different points in their warehouses:
- Inventory: Barcode labels can be placed on all products, allowing them to be scanned in and out quickly. They can also be used to track the location of bins and pallets of inventory throughout the warehouse.
- Boxes: When boxes are packed with multiple items, a barcode label can be placed on the box for easy identification.
- Shipping: When sending parcels to customers, a shipping label including a barcode is added to the package.
The barcode scanner is inventory control and tracking at its best. By scanning the code found on a product, you can keep track of items as they move throughout your warehouse. This information stored in the barcode will allow you to better monitor stock levels and know what products are available for shipping.
For an in-depth look at what this might look like for you, check out our blog on how to implement barcodes in your warehouse.
5. Forecast Demand Using Inventory Data
Forecasting demand is one of the most vital yet challenging tasks for any organisation. Without accurate forecasting, you risk ending up with too much or too little inventory on hand, resulting in lost opportunities as well as higher costs and delayed shipments.
There are a couple of essential functions that inventory data serves:
- Proactively Order Inventory: Using predictive analytics from your existing inventory data can help you better anticipate customer demand and plan accordingly. This will not only help you avoid overstocking, but it will also eliminate the need for rush ordering and ensure that your customers receive their orders on time.
- New Customer Insights: Our interactive BI and reporting dashboards give you visibility into customer trends, helping you make data-driven business decisions.
- Maximise Profit Margins: To increase profit margins, you need to be smart about the inventory you sell. Using customer data, you can consider quantity discounts, special orders, and wholesale prices when making decisions.
Use your inventory control software to run reports on the speed of stock sell-through, what products are out of stock, and sales performance by category or brand. This will give you the data you need for accurate inventory forecasting.
Remember that consumer demand can often fluctuate, so make sure to run these reports regularly.
6. Get the Complete Inventory Picture Using IoT Devices
The Internet of Things (IoT) has become an increasingly important part of inventory control. IoT devices can provide real-time data on the location and condition of goods in a warehouse, giving you a complete picture of your inventory at all times.
According to Forbes, 75% of global retail decision-makers are now adopting IoT devices to track the status of inventory for sale. They offer a wide range of benefits, from reducing the cost of inventory management to improving customer satisfaction and speed to market.
These devices typically come in the form of sensors or tags that can be placed on products or pallets.
Examples include:
- RFID tags and sensors: RFID tags allow you to track goods throughout the warehouse and quickly access information about them.
- Temperature sensors: These are important for monitoring temperature-sensitive products that may need to be stored in cool, dry conditions.
- Humidity sensors: Humidity sensors help monitor warehouse indoor climate control, ensuring products aren’t damaged due to moisture or high temperatures.
Many IoT devices integrate with your existing software and are easy to install and maintain, making them ideal for inventory control.
Taking Back Inventory Control: How Our WMS Can Help
Having a good inventory control system in place is essential for any business. It allows you to effectively manage your warehouse operations and ensure that products are available when customers need them.
Using Datapel’s warehouse management system, you’ll shave hours off every workweek, increase speed and accuracy, reduce labour and inventory costs, and boost customer satisfaction by ditching your manual processes.
And if you follow the tips in this guide, you’ll be well on your way to keeping everything in check—from first order to fulfilment.
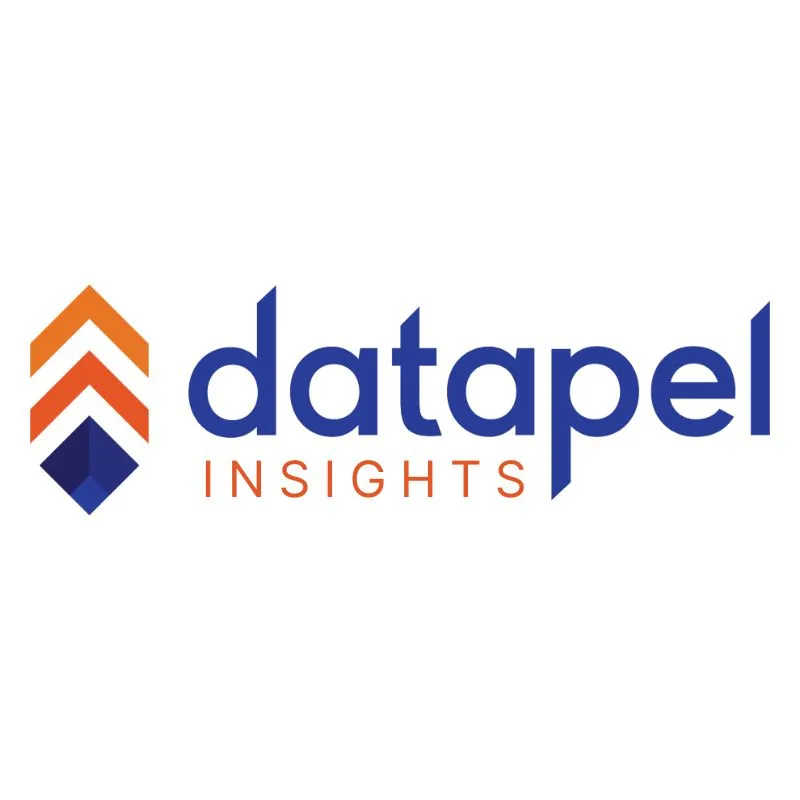
In my role, I oversee the development of insightful blogs that delve into the intricacies of warehouse management. Each piece reflects my dedication to empowering businesses through informative content. Through my team’s extensive experience in the industry, we aim to bring clarity to the complexities of WMS, helping businesses make informed decisions.
Join me on a journey through the ever-evolving landscape of warehouse technology as we explore the latest trends, industry insights, and practical tips to streamline your operations. Feel free to connect, and let’s embark on a collaborative exploration of how WMS can redefine your business efficiency.
Cheers to innovation, efficiency, and the exciting world of warehouse management!