How to Evolve to an Automated Warehouse in 2023
Contents
Utilise Your Warehouse Management System to Reach Peak Performance
The supply chain crisis has caused massive shifts over the past year. Many warehouse operations are looking for ways to improve operational efficiency to keep up with these changes. To ease the pressure of meeting demand, operators may consider implementing automated warehouse processes by adjusting workflows and utilising management software.
Why Automation?
According to Shopify’s 2023 commerce trends, 68% of respondents indicated the current supply chain crisis negatively impacts their ability to fulfil customer demand. With the need to reduce costs, improve efficiency, and meet growing customer demand for fast shipping, operations that shift to automated warehouse solutions will thrive.
While adjusting workflows and introducing new technology may seem intimidating, operators can take the following steps to ease the processes of evolving into an automated warehouse.
1. Get Organised
Optimise Workflows
While it may be tempting to jump straight to technology for automation, organising internal workflows is the first step to becoming an automated warehouse. Having efficient inventory management is a smart place to begin your workflow organisation process.
Choosing effective inventory management is crucial to accurately tracking stock levels. This is most efficient when it’s on one system with capabilities to search for partial items, names, batches, bins, barcodes, and custom field lookups.
With a solid inventory management system, you can begin to match your business needs to picking strategies that create optimised stock rotations. Common picking strategies include first-in-first-out (FIFO), last-in-first-out (LIFO), bin number ascending, descending, minimum, maximum, and expiry date based.
The right picking strategy will depend on the industry and business type, but once implemented will save time and reduce the risk of spoilage or expired goods.
Once you have implemented the right picking workflow, warehouse management software (WMS) can help operations become even more efficient and automate parts of the process. For example, a WMS can utilise business data to create custom pick paths. Or, tap into solutions like real-time location tracking and automated intelligent pick paths to further reduce one of the most costly parts of the warehousing process – employee travel time.
Start Reporting
Once basic processes are in place, it’s time to introduce BI and warehouse reporting. Warehouses can begin collecting data to gain insights on inventory holdings, stock movement, replenishment alerts, receiving and despatch forms, and how long your inventory will last. Also, role-based dashboards with pre-built industry KPIs and valuable metrics provide insights into business operations you can comprehend without being an expert statistician.
These may seem like simple statistics, but basic reporting is an excellent way to ease into more complex data that an automated warehouse needs.
Continue Consultation
Becoming an automated warehouse only begins with implementing processes and reporting with a WMS solution. After your initial setup, continue working with your WMS provider to identify your core needs for the next step of warehouse automation, maximising efficiency.
2. Boost Efficiency
Implement Barcodes
Once you have solid workflows and warehouse standard operating procedures (SOPs), automate further with barcodes. A WMS and barcoding solution work together to create powerful workflows and inventory management.
With a barcode WMS system, operators can efficiently manage multiple users. Assign administrators and workers different access to provide granular permissions for functionalities relevant to their work. Plus, with unique users, it’s simple to perform an audit trail review to determine efficiency by workers or analyse process compliance.
Barcodes allow the warehouse to dig deeper into processes to determine if systems are efficient by tracking worker events and times down to order numbers and item references.
In addition, barcodes can further accelerate processes by advancing simple inventory management. Once barcodes begin to work with your WMS, features like bin audits, rolling stock counts, and managing stock movement between locations become possible. Or, take your simple picking strategy further with barcode scanning to improve accuracy and increase picking speed.
Automated Reports and Alerts
While basic reporting is vital for learning key insights, operators can take a more detailed look at their processes with custom reports. Most systems offer default reports that can be customised or seamlessly connected with other applications using open API, so your data is unified. Keep your team informed with automated reporting by scheduling daily, weekly, or monthly auto-emails and selecting which employees receive reports.
Automate further with alerts from your WMS. If you have known backorders present, your WMS can flag employees once that stock is received so they know to prioritise the items for upcoming picks. Or, create an alert to help staff to implement effective logistics techniques like cross docking. A WMS can alert staff to move incoming stock to outbound vehicles without needing storage or handling in a warehouse.
Utilise your WMS to implement automated, smart purchase orders. Set demand-based triggers based on inventory minimums/maximums or user-selected levels. Once the inventory level is reached, your WMS can create purchase orders from primary and alternate suppliers. With effortless purchase order creation, there’s less chance of backorders or out-of-stock items.
3. Become a Fully Automated Warehouse With Best Practices
Utilise Integrations
Once your operation has optimised and efficient processes, it’s time to ensure you’re following best practices. With warehouse software integrations, operators gain complete visibility into every aspect of the business.
Link your inventory management system directly to your ERP, business applications, or eCommerce systems. Plus, API technology ensures you can build any integration you want to create an end-to-end automated business platform without the risk of data silos.
Synchronise on the Cloud
Many operations are moving toward cloud-based applications and databases capable of collecting, processing, and storing large datasets. Operators can drive data analytics around warehouse operations further with a cloud WMS. A cloud-based system offers workers access to real-time data sets and can act as a central repository for inventory information, correspondence, and business transactional documentation. It’s all there at the click of a button.
Track Key Performance Indicators
Key performance indicators (KPIs) help warehouse operators better understand their top productivity levels and whether they are under or overperforming. However, old KPIs from a manual environment may not fit an automated warehouse. To take your warehouse to the next level, you must use your WMS to pull data and monitor KPIs that will help you understand where your team excels and where there’s room for improvement.
After all, the primary goal of automation is to increase throughput.
Software to Evolve to an Automated Warehouse
Becoming an automated warehouse with a warehouse management system is crucial to keep operations on track with today’s demands. With supply chain disruptions and changing customer expectations, operators must reduce costs, improve efficiency, and increase fulfilment speeds to stay competitive. Investing in the technology needed for automation can help operators meet these demands and offer opportunities to scale their business.
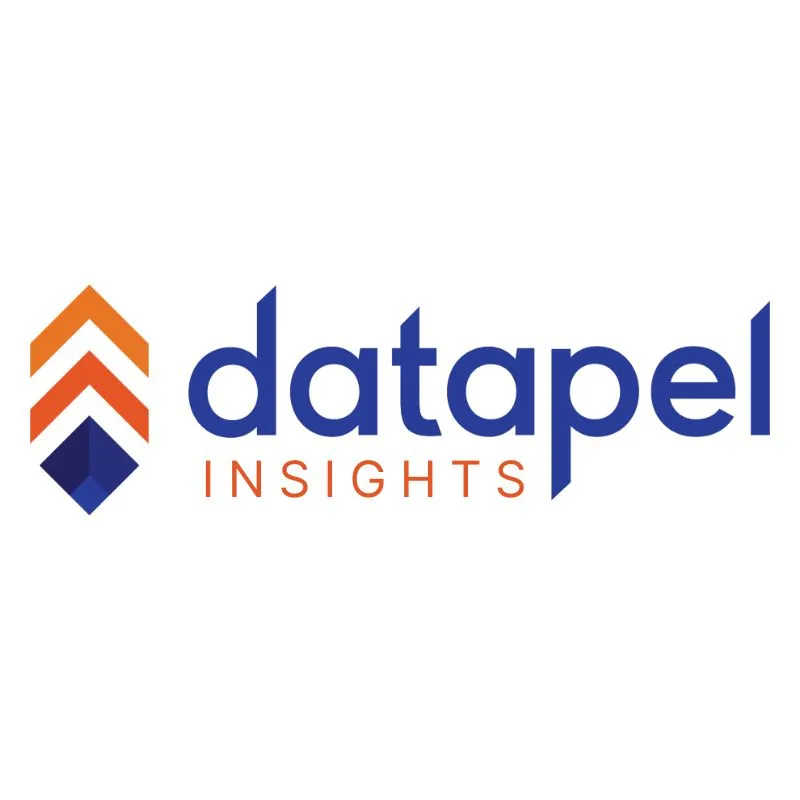
In my role, I oversee the development of insightful blogs that delve into the intricacies of warehouse management. Each piece reflects my dedication to empowering businesses through informative content. Through my team’s extensive experience in the industry, we aim to bring clarity to the complexities of WMS, helping businesses make informed decisions.
Join me on a journey through the ever-evolving landscape of warehouse technology as we explore the latest trends, industry insights, and practical tips to streamline your operations. Feel free to connect, and let’s embark on a collaborative exploration of how WMS can redefine your business efficiency.
Cheers to innovation, efficiency, and the exciting world of warehouse management!