Cycle Count Mastery: Elevate Your Inventory Accuracy with These Proven Strategies
Contents
A well-oiled machine needs all its parts to work harmoniously, and the same goes for a successful business. Inventory management is one such vital cog in the business machinery, with cycle count being the grease that ensures smooth operations.
Key Takeaways
- Decipher the cycle counting process & optimize inventory accuracy with an effective program.
- Leverage the ABC method to prioritize higher-value items and maximize accuracy.
- Follow best practices such as establishing a control group & regularly reviewing processes for reliable cycle counts.
Decoding the Cycle Counting Process
Picture a room full of different items, each with its place on the shelves. Now imagine having to count each one, ensuring the physical items match your records. Cycle counting involves a systematic approach to maintaining inventory accuracy. It involves regularly counting small portions of inventory to ensure alignment between the physical stock and recorded data. This method is key to the smooth operation of inventory management.
The cycle counting process, including random sample cycle counting, involves selecting a limited number of items at regular intervals and conducting a count. The count is then compared with the count stored in the system to determine if there is a match. Constant population counting and diminished population counting are two inventory cycle counting methods commonly used in cycle counting.
These methods help to accurately measure and monitor inventory levels. Inventory counts, which play a crucial role in determining the inventory accuracy percentage, are usually performed when operations have ceased for the day or before they begin.
The Anatomy of Effective Cycle Counting Programs
Like a maestro conducting an orchestra, an effective cycle counting program coordinates multiple elements to maximize inventory accuracy. This involves setting up a cycle count calendar, prioritizing items using ABC analysis, and fine-tuning the counting technique.
Setting Up Your Cycle Count Calendar
Imagine trying to organize a party without setting a date and time. It would be chaotic, right? The same applies to your inventory. Before starting a cycle counting routine, it’s advisable to create a plan that details the schedule and frequency of inventory counts.
This process includes:
- Segmenting your inventory based on factors such as value, turnover rate, and criticality
- Determining the frequency and schedule for counting each category of inventory
- Developing a schedule based on the assessment
- Finalizing transactions for the items under consideration to maintain accuracy.
Prioritizing Items with ABC Cycle Counting
Think of your inventory as a classroom of students. The ABC cycle count is like a teacher who prioritizes students based on their academic performance, giving more attention to those who need it. ABC cycle counting is a method of assigning a particular value to each product in counting inventory, with items of higher value being counted more frequently than those of lower value.
In addition to value, other metrics like transactions and production numbers can be used in ABC cycle counting. This method classifies inventory into three groups according to their sales performance and holding cost. The analogy could be a shopping mall that displays the most sought-after and costly items prominently to draw in customers.
Nevertheless, one downside to ABC cycle counting is the risk of over-counting certain prioritized sections, potentially leading to an unrepresentative sample.
Fine-tuning the Counting Technique
A finely tuned instrument produces the most harmonious melody, and so it is with the cycle counting technique. Effective methods for training staff in inventory cycle counting techniques include setting cycle counting goals, educating employees on the process, and rewarding them for their accomplishments.
To ensure checks and balances, it’s necessary to review inventory records, establish accuracy level targets, perform regular counts, reconcile discrepancies, and implement corrective actions as needed. Continuous improvement strategies include implementing regular cycle counts, using technology, analyzing root causes, and providing regular training.
Strategies to Maximize Inventory Accuracy
Just as a ship relies on a compass for navigation, businesses require strategies for optimal accuracy. These strategies include double-checking counts, addressing variances in inventory records, and implementing best practices.
Double-Checking Counts for Accuracy
In inventory management, two heads are indeed better than one. Double-checking counts ensures that human errors are minimized, leading to more accurate inventory data. To ensure accurate inventory counts, a few methods are recommended:
- Conduct a physical count of year-end inventory.
- Compare multiple completed inventory count reports.
- Double-check the count by cross-referencing physical inventory against the most current inventory records.
Errors like mislabeling items with varying identification numbers, miscounting similar items, and creating mistakes while managing multiple locations can be minimized by:
- Repeatedly verifying the count
- Comparing the count with identification numbers or product descriptions
- Using inventory control software for cycle counting.
Addressing Variances in Inventory Records
It’s like finding a mismatch in your bank statement; no one likes variances in inventory records. They can be tackled by:
- Performing regular cycle counts
- Making use of inventory management software
- Training employees
- Implementing quality control measures
- Promptly investigating and rectifying discrepancies.
Errors such as:
- Physical counting
- Scanning
- Picking and placement
- Cycle counting frequency
- Shrinkage
- Inventory systems
- Storage
- Recordkeeping
should be taken into account to ensure accuracy in inventory counts. Ensuring accurate inventory records is like keeping a tidy house; it requires regular cleaning and maintenance.
Integrating Technology into Cycle Counting
In the same way that GPS has revolutionized navigation, technology has transformed cycle counting. Integrating technology, like barcode scanners and RFID, enables real-time data updates and enhances accuracy in inventory management systems.
Leveraging Barcode Scanners and RFID
Think of barcode scanners and RFID as the superheroes of inventory management, streamlining the counting process and reducing manual errors.
- Barcode scanners and RFID technology read and write data to tags, allowing for more precise and frequent inventory cycles
- Automating data collection via handhelds
- Providing real-time tracking of inventory throughout the supply chain.
Real-time inventory level updates and barcode scanners offer the following benefits:
- Lower the chance of errors
- Provide dependable and precise data for inventory counting, order picking, and stock management
- Significantly improve the accuracy and efficiency of cycle counting
Real-Time Data with Inventory Management Systems
Picture a control room with screens displaying real-time data from across a city. That’s what real-time data in inventory management systems is like. These systems provide up-to-date information on stock levels, ensuring that the counts are always in sync with the actual inventory.
This real-time data significantly improves inventory management by:
- Providing precise and current data on inventory levels
- Facilitating the optimization of processes
- Reducing stockouts
- Streamlining workflow
- Enhancing decision-making
- Making it easier to meet delivery schedules.
Physical Inventory Count vs. Cycle Count: A Comparative Analysis
Just as a runner chooses between a sprint and a marathon based on their strengths and goals, businesses must choose between physical inventory counts and cycle counts. Physical inventory count involves counting the entire physical inventory in a given facility, while cycle counting involves periodically counting limited portions of inventory.
Physical inventory counting condenses the counting into a single, intensive period, while cycle counting distributes it across the year. Cycle counting enables businesses to update their inventory records without disrupting operations or closing time, thereby preserving inventory control and maintaining ongoing processes. On the other hand, physical inventory counting allows for a complete and thorough count at specific time points, usually once or twice annually.
Navigating Common Cycle Counting Challenges
Like navigating a maze, cycle counting can present challenges such as multiple inventory locations, delayed paperwork, and unprocessed transactions. However, just as a skilled maze runner can overcome obstacles, these challenges can be effectively navigated by implementing proper procedures and best practices.
Businesses can address paperwork lags during cycle counting by implementing digital solutions, automating data entry, improving communication and collaboration, training employees, and regularly reviewing and updating processes.
To manage outstanding transactions, it’s necessary to finalize all open transactions for the items being counted before initiating a cycle count, update inventory records first, and record all outstanding inventory transactions before launching the cycle count.
Best Practices for Reliable Inventory Cycle Counts
Just as a pilot follows a pre-flight checklist to ensure a safe journey, businesses can follow best practices to ensure reliable inventory cycle counts. These include establishing a control group for benchmarking and continuously reviewing and improving the process.
Establishing a Control Group for Benchmarking
In the realm of cycle counting, a control group serves as a compass, helping to identify errors and areas for improvement. Control group cycle counting involves:
- Repeatedly counting a limited set of items over a brief period
- Validating the process
- Detecting any discrepancies before applying it to the entire inventory.
To set up a control group for cycle counting, follow these steps:
- Select a small group of items from your inventory.
- Count these items multiple times over a specific period.
- Use the control group as a benchmark for accuracy and to enhance your cycle counting process.
- Count high-priority items as frequently as daily.
- Conduct a full cycle count at least once every three months.
Continuous Improvement through Regular Reviews
Continuous improvement to a business is akin to regular exercise for maintaining fitness. Periodic reviews of the cycle counting process are needed to guarantee consistent optimization and alignment with changing inventory needs and business goals.
Regular counts and adjustments, ABC analysis, a barcode system, staff training and empowerment, and periodic evaluation of the process are some techniques employed to review and enhance the cycle counting process. It’s like regular health check-ups, with the inventory as the patient and the business as the doctor, constantly monitoring and adjusting to ensure optimum health.
Summary
From decoding the cycle counting process to navigating common challenges and implementing best practices, we’ve journeyed through the intricacies of inventory cycle counting. By integrating technology, prioritizing items, and continuously improving the process, businesses can maintain the accuracy of inventory, streamline operations, and ultimately, drive growth. Like a well-tuned instrument, a well-managed inventory system can create harmonious business operations.
Frequently Asked Questions
What is the purpose of a cycle count?
The purpose of cycle counting is to check and confirm the accuracy of a company’s inventory records by counting a select portion of products at regular intervals. This method allows businesses to keep tabs on their inventory without having to conduct an annual audit of everything they stock.
What is the difference between cycle count and stock count?
Stock counts involve the physical counting of all inventory items at once, while cycle counts are done continuously and only focus on specific products, batches, locations, or stock conditions. Cycle counts occur much more frequently than stock counts, allowing for a more thorough and timely overview of inventory.
How accurate is a cycle count?
Cycle counting is a reliable and efficient way to maintain high inventory accuracy levels, with industry benchmarks set at 95% or higher. Regular inspections reduce errors and can provide accuracy rates across the entire facility.
What is ABC cycle counting?
ABC cycle counting is a method of assigning higher-value items a higher frequency of inventory counts compared to lower-value items. It allows for efficient inventory management and stock control.
How does technology enhance cycle counting?
Technology allows for real-time updates and increased accuracy in inventory management systems, such as with the use of barcode scanners and RFID. This enhances cycle counting by providing more reliable data and minimizing manual labour.
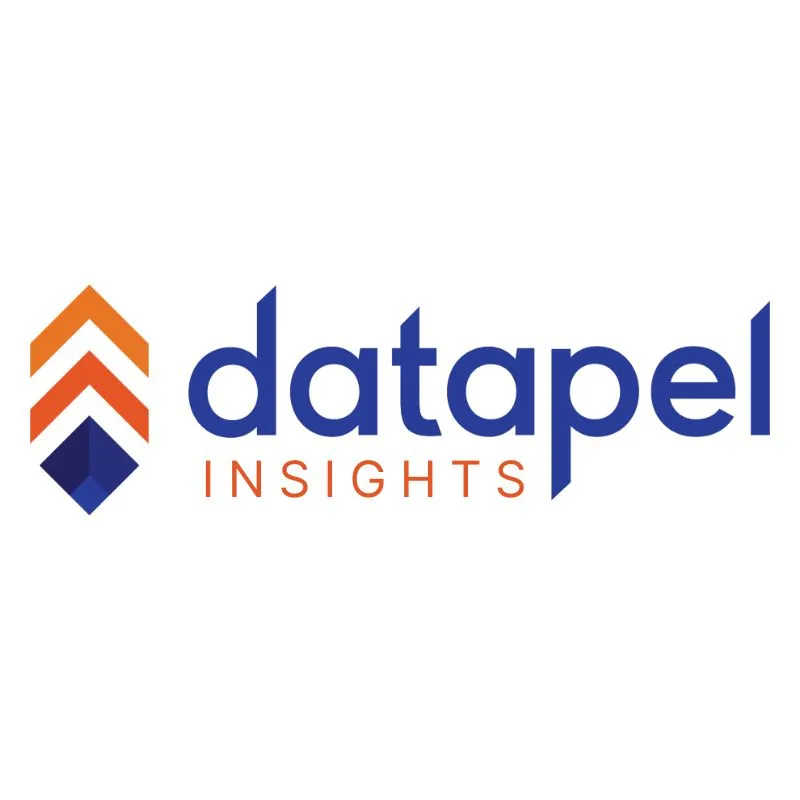
In my role, I oversee the development of insightful blogs that delve into the intricacies of warehouse management. Each piece reflects my dedication to empowering businesses through informative content. Through my team’s extensive experience in the industry, we aim to bring clarity to the complexities of WMS, helping businesses make informed decisions.
Join me on a journey through the ever-evolving landscape of warehouse technology as we explore the latest trends, industry insights, and practical tips to streamline your operations. Feel free to connect, and let’s embark on a collaborative exploration of how WMS can redefine your business efficiency.
Cheers to innovation, efficiency, and the exciting world of warehouse management!