Mastering Multi-Location Warehouse Management for Wholesale & Distribution
Contents
Wholesale and distribution businesses rely on inventory accuracy, fast order fulfilment, and smooth operations to stay competitive. But as operations expand across multiple warehouses, tracking stock levels, managing orders, and keeping operations efficient becomes increasingly difficult. Let’s explore how mastering multi-location warehouse management can up your game!
What is Multi-Location Management?
Multi-location management refers to the process of tracking, organising, and optimising inventory across multiple warehouses or storage locations. Instead of managing stock from a single warehouse, businesses using multi warehouse management can distribute inventory strategically across different warehouse locations to reduce shipping and delivery costs, improve order fulfilment speeds, and prevent stock shortages.
Effective multi-location inventory management ensures that stock is allocated in the best way possible, helping businesses scale while maintaining customer satisfaction. It also enables real-time visibility, allowing warehouse teams overseeing inventory, and managers to make informed decisions based on the latest inventory data.
Why Multi-Location Warehouse Management Matters
Without a centralised inventory management system, businesses may struggle with stock discrepancies, delays in fulfilment, and high operational costs. Managing inventory data manually often results in missing or duplicated stock records, making it harder to track real-time changes. If these challenges sound familiar, you are not alone.
Many wholesale and distribution businesses face the same supply chain issues when scaling their operations. The key to success lies in multi location inventory management, which allows businesses to keep control of their stock across different locations while improving efficiency and reducing costs.
Common Challenges in Multi-Location Inventory Management
1. Manual Processes and Data Fragmentation
Many businesses still rely on spreadsheets or disconnected systems to manage inventory. While this may work in a single warehouse, managing stock across multiple locations and with manual methods it creates issues such as inaccurate stock levels, delays in updating inventory data, and errors in order fulfilment due to outdated records.
Without real-time inventory tracking, businesses risk overstocking, understocking, and costly fulfilment delays. The lack of data accuracy makes it harder to track trends and forecast customer demand effectively.
2. Managing Stock Across Multiple Locations
Stock stored across multiple warehouses can lead to increased picking errors due to multi-bin inventory management, slower fulfilment times when stock allocation is unclear, and higher shipping costs when orders are sent from the wrong location.
A multi-location inventory solution provides real-time visibility into stock movement, allowing businesses with multi location warehouse management to allocate stock more effectively and reduce wasted resources. This visibility helps track stock levels across warehouse locations, ensuring the right inventory is available at the right place at the right time.
3. Inefficient Returns Management
Handling returns manually across different warehouses can cause delays in processing refunds, errors in stock reallocation, and increased operational costs. Without a structured process, inventory data from as many warehouses becomes inconsistent, leading to inaccurate stock levels and warehouse inefficiencies.
An automated returns system ensures that products are checked against batch numbers and expiry dates, improving accuracy and reducing delays. Businesses that integrate returns management with real-time inventory tracking can update inventory data immediately, ensuring that returned stock is processed without disrupting operations.
4. The Backorder Bottleneck
Many businesses still track backorders manually, which can lead to orders being missed or delayed, poor communication between sales and warehouse operations teams, and missed revenue when available stock is not updated in the system. Without proper data accuracy, backorders may be overlooked, causing unnecessary fulfilment delays.
A WMS with real-time inventory tracking ensures that backorders are updated immediately, preventing fulfilment delays. Keeping track of stock levels in real time allows businesses to process backorders efficiently, reducing errors and improving customer experience.
How to Effectively Manage Inventory Across Multiple Warehouses
To more effectively manage inventory across multiple warehouses, businesses need an approach that balances visibility, automation, and efficiency.
1. Use a Centralised Inventory Management System
A centralised inventory management system ensures that all stock levels, orders, and returns are tracked in real time. This helps businesses reduce stock discrepancies across multiple inventory locations, improve demand forecasting, and automate stock allocation across different warehouses.
2. Automate Picking and Order Allocation
Efficient picking and order fulfilment can be achieved with multi-bin inventory management software, allowing businesses to manage multiple warehouses with full visibility. Automated order splitting assigns pickers to the right zones, ensuring that stock is picked from the best possible location. With real-time inventory tracking, errors are minimised, and fulfilment speeds increase.
3. Implement an Efficient Returns Process
A structured returns process helps businesses validate returns against batch numbers and expiry dates, speed up refunds and restocking across multiple locations, and keep inventory records up to date. Improving data accuracy ensures that stock levels are maintained correctly, preventing discrepancies.
4. Automate Backorder Tracking
An automated system ensures that when stock arrives, it is automatically updated in the system, immediately allocated to fulfil backorders, and tracked in real-time to prevent delays. By maintaining accurate data accuracy, businesses can ensure that stock is always allocated to the right orders without confusion.
Scaling Your Business with Smarter Inventory Management
Managing stock across multiple warehouses is a challenge, but with the right multi-location inventory management approach, businesses can improve stock accuracy, prevent shortages, and reduce fulfilment delays.
As wholesale and distribution businesses expand, efficiency and accuracy become even more important. If inventory issues are slowing you down, now is the time to explore strategies that improve efficiency and customer satisfaction.
What is your biggest challenge with multi-location inventory? Let us know in the comments.
How Datapel Supports Wholesale & Distribution Businesses
Wholesale and distribution businesses need more than just to track inventory—they require a solution that provides real-time visibility, automates processes, and ensures data accuracy across multiple locations. Datapel’s warehouse management system (WMS) is designed to help businesses overcome common, inventory control challenges and improve operational efficiency.
1. Real-Time Inventory Tracking for Smarter Decision-Making
Datapel’s WMS provides real-time inventory tracking, giving businesses complete insight into stock and inventory levels across multiple warehouses. This ensures that stock is always allocated correctly, reducing the risk of overstocking, stock shortages, or unnecessary transfers between warehouse locations.
2. Automated Order Fulfilment and Multi-Bin Management
Managing inventory across multiple locations can slow down fulfilment if not handled correctly. Datapel streamlines the process by offering multi-bin inventory management, ensuring that pickers can locate stock quickly and accurately. Orders are automatically assigned to the correct zones, reducing errors and speeding up dispatch times.
3. Advanced Backorder Management to Prevent Lost Sales
Tracking backorders manually can lead to delays, miscommunication, and lost revenue. Datapel’s system updates inventory data automatically, ensuring that backorders are fulfilled as soon as stock arrives. Businesses no longer need to rely on spreadsheets or manual updates—every order is processed efficiently, with full visibility at every stage.
4. Seamless Returns Management for Greater Efficiency
Processing returns across different locations can become complicated, but Datapel simplifies the workflow. The system validates returns based on batch numbers, expiry dates, and stock levels, ensuring only eligible products are accepted. This reduces errors, speeds up processing, and keeps inventory records accurate.
5. Integration with Accounting and eCommerce Platforms
Wholesale and distribution businesses often operate across multiple sales channels and need seamless integration with existing systems. Datapel connects directly with MYOB, Xero, and leading eCommerce sales platforms, allowing for automatic synchronisation of orders, stock levels, and financial data. This eliminates the need for manual data entry, improving accuracy and saving time.
6. Optimised Stock Allocation to Reduce Costs
By distributing stock strategically across warehouse locations, businesses can cut down on shipping and delivery costs. Datapel’s system provides insights into where stock should be placed to minimise fulfilment times and transport expenses. Businesses can set up multi-warehouse strategies that prioritise faster deliveries while keeping costs under control.
7. Full Visibility with Data-Driven Insights
Datapel’s detailed reporting and analytics tools help businesses track market trends, optimise stock levels, and improve demand forecasting. With real-time visibility, managers can make informed decisions on restocking, seasonal demand shifts, and warehouse efficiency, ensuring they always stay ahead of operational challenges.
Supporting Growth with Datapel
Whether a business is expanding into more warehouses, increasing order volume, or improving fulfilment and delivery speeds, Datapel’s WMS is built to scale. Its flexible features ensure that wholesale and distribution businesses can adapt to market changes while maintaining inventory accuracy and operational efficiency.
By leveraging Datapel’s advanced inventory management processes, businesses can reduce manual tasks, lower operational costs, and improve customer satisfaction—ensuring they stay competitive in a rapidly evolving industry.
Final Thoughts
Managing inventory across multiple warehouses does not have to be complicated. By focusing on real-time inventory visibility, automation, and structured processes, businesses can stay ahead of customer demand, reduce costs, and improve overall efficiency.
Ensuring data accuracy and maintaining real-time visibility of stock levels across warehouse locations helps businesses scale without losing control over their inventory.
For more insights on multi-location inventory management, stay connected with us for the latest updates.
Additional FAQs on Multi-Location Inventory Management
1. How Does Multi-Warehouse Inventory Management Reduce Costs?
By distributing stock across multiple locations, businesses can lower delivery costs by shipping from the nearest warehouse, minimise overstocking and free up working capital, and reduce labour costs with automated workflows.
2. What Are the Key Features of a Multi-Warehouse Strategy?
A successful multi-warehouse strategy includes real-time inventory visibility across all locations, automated stock allocation to reduce picking errors, and accurate demand forecasting to optimise stock for optimal inventory levels.
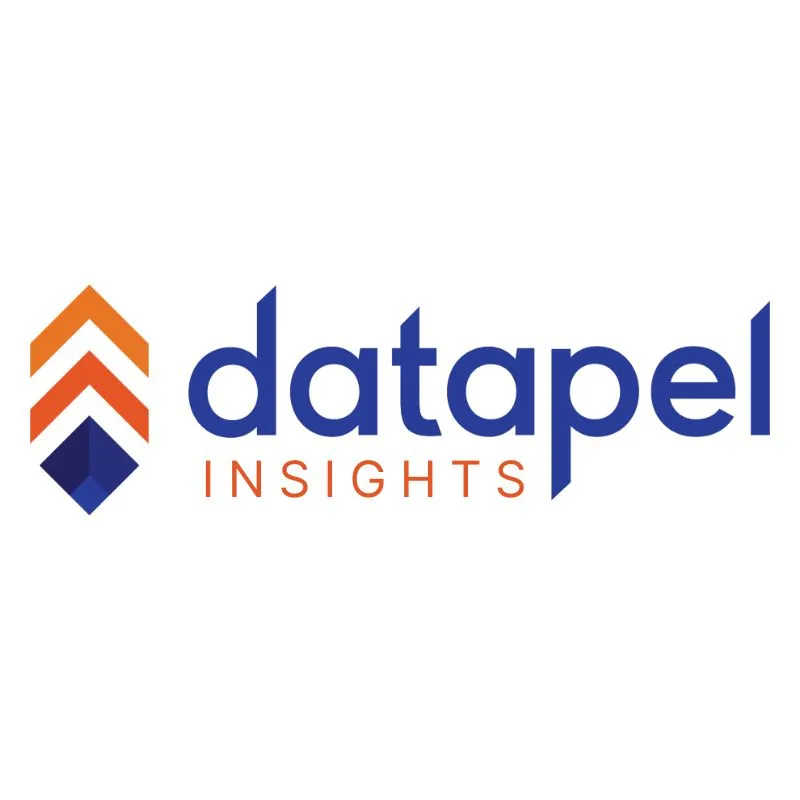
In my role, I oversee the development of insightful blogs that delve into the intricacies of warehouse management. Each piece reflects my dedication to empowering businesses through informative content. Through my team’s extensive experience in the industry, we aim to bring clarity to the complexities of WMS, helping businesses make informed decisions.
Join me on a journey through the ever-evolving landscape of warehouse technology as we explore the latest trends, industry insights, and practical tips to streamline your operations. Feel free to connect, and let’s embark on a collaborative exploration of how WMS can redefine your business efficiency.
Cheers to innovation, efficiency, and the exciting world of warehouse management!