Mastering the Art of Order Picking: Strategies, Tips, and Best Practices
Contents
In the bustling world of retail and wholesale operations in Australia and New Zealand, efficient order picking is the backbone of successful logistics management. It’s the process that ensures products are selected accurately and swiftly for delivery to customers, and when done right, it can be a game-changer for your business.
In this article, we’ll delve deep into the world of order picking, providing you with strategies, tips, and best practices to help you master this critical aspect of your operation. Whether you’re a seasoned professional or just starting out, we’ve got you covered.
What is Order Picking?
At its core, order picking is the process of selecting items from your inventory to fulfil customer orders. It’s a pivotal stage in the supply chain, bridging the gap between having products in your warehouse and getting them into the hands of your customers. The goal of order picking is to do this efficiently, accurately, and cost-effectively.
The Importance of Efficient Order Picking
Efficient order picking is not just a nicety; it’s a necessity for businesses operating in the retail and wholesale sectors. It directly impacts customer satisfaction, operational costs, and overall profitability. Inefficient order picking can lead to errors, delays, and increased expenses, which can quickly erode your bottom line and tarnish your reputation.
Strategies for Optimising Order Picking
Now that we understand the significance of efficient order picking, let’s explore some strategies to optimise this crucial process:
1. Warehouse Layout and Organisation
A well-organised warehouse is the foundation of efficient order picking. Consider the layout of your storage areas, ensuring that frequently picked items are easily accessible. Implement a logical organisation system, such as bin locations or alphabetical arrangement, to minimise search times.
2. Choosing the Right Equipment
Invest in the right order picking equipment for your specific needs. This might include pallet jacks, forklifts, or automated systems like conveyor belts or pick-to-light systems. The right equipment can significantly increase the speed and accuracy of the picking process.
3. Training and Staffing
Your order picking team plays a pivotal role. Ensure they receive proper training on picking techniques, safety procedures, and the efficient use of equipment. Consider cross-training your staff to handle different types of orders, providing flexibility in your workforce.
4. Implementing Technology Solutions
Embrace technology to streamline order picking. Warehouse management systems (WMS) and order management software can help track inventory, prioritise orders, and provide real-time data for decision-making. These tools can significantly reduce errors and enhance productivity.
Order Picking Methods: Batch vs. Wave Picking
In the realm of order picking, efficiency is the name of the game. To achieve peak efficiency, businesses often employ various picking methods, each tailored to specific operational needs. Two common methods are batch picking and wave picking.
Let’s delve into these methods, exploring how they work and when to use them.
Batch Picking: Maximising Efficiency
Batch picking, also known as multi-order picking, is a method where a picker selects items for multiple orders simultaneously. It’s akin to a waiter efficiently carrying multiple plates to serve various tables in a restaurant.
Here’s how it works:
- Grouping Orders: In batch picking, orders with similar items or locations are grouped together. This minimises the number of trips a picker needs to make to retrieve items.
- Single Trip: Armed with a picking list for all grouped orders, the picker navigates the warehouse once, selecting the required items and placing them in separate totes or bins designated for each order.
- Sorting and Packing: After the batch-picking process, items are sorted and packed into individual order boxes, ready for shipping.
Advantages of Batch Picking:
Efficiency: Batch picking reduces travel time within the warehouse, making it faster and more efficient.
Reduced Labour Costs: Fewer trips mean fewer man-hours, ultimately reducing labour costs.
Increased Accuracy: Handling similar items at once reduces the chance of picking errors.
When to Use Batch Picking:
High Volume: Batch picking shines when dealing with a high volume of orders.
Similar Orders: It’s most effective when orders share common items.
Wave Picking: Streamlining Complex Operations
Wave picking, on the other hand, is like conducting an orchestra, where each picker focuses on a specific instrument (order). This method is well-suited for complex operations that require careful orchestration:
- Order Waves: Orders are grouped into “waves” based on various factors like order priority, delivery schedules, or product availability.
- Assigning Pickers: Each wave is assigned to specific pickers who focus solely on the orders within their assigned wave.
- Sequential Picking: Pickers work through their assigned orders sequentially, following the predetermined wave sequence.
- Consolidation: After picking, items from each wave are consolidated into separate packing stations for final packaging.
Advantages of Wave Picking:
Order Priority: Allows prioritisation of critical orders.
Complex Operations: Ideal for operations with various order types, sizes, or delivery schedules.
Error Reduction: Minimises confusion as pickers focus on specific orders.
When to Use Wave Picking:
Diverse Orders: Wave picking is valuable when dealing with diverse orders with varying priorities.
Complex Operations: It’s especially useful when juggling different product types or delivery requirements.
Combining Methods for Efficiency
While batch and wave picking each have their strengths, some operations benefit from a combination of both. This hybrid approach is particularly effective in larger warehouses with diverse product lines and fluctuating order volumes.
Here’s how it can be implemented:
- Prioritise Orders: Use wave picking to prioritise orders based on criteria like delivery deadlines.
- Group Similar Orders: Within each wave, employ batch picking to efficiently handle orders with common items.
- Coordinate Picking: Ensure proper coordination between wave pickers and batch pickers to maximise efficiency.
- Consolidate Orders: After picking, consolidate items for each order into packing stations.
Advantages of Combining Methods:
Flexibility: Allows you to adapt to changing operational needs.
Efficiency: Maximises efficiency by combining the strengths of both methods.
When to Use a Hybrid Approach:
Complex Operations: Ideal for large operations with diverse needs.
Fluctuating Order Volumes: Adapts well to changing order volumes and priorities.
In the world of order picking, there’s no one-size-fits-all solution. Your choice of picking method should align with the unique requirements of your business. Whether you opt for batch picking, wave picking, or a combination of both, the key is to continuously evaluate and refine your approach to achieve optimal efficiency and customer satisfaction.
Remember, the art of order picking is a dynamic journey, and mastering it involves choosing the right methods that best suit your operational symphony.
Quality Control in Order Picking
Implement a robust quality control process to catch errors before they reach customers. Regularly audit orders, conduct spot checks, and create a feedback loop with your pickers to identify and rectify issues promptly.
Monitoring and Continuous Improvement
Monitor key performance indicators (KPIs) related to order picking, such as pick accuracy, picking rate, and order cycle time. Use this data to identify areas for improvement and implement changes to enhance efficiency continually.
Conclusion
Mastering the art of order picking is not an option; it’s a necessity for businesses in the retail and wholesale sectors in Australia and New Zealand.
By focusing on warehouse organisation, equipment selection, staff training, technology integration, picking methods, quality control, and continuous improvement, you can optimise your order picking process and boost your bottom line.
Frequently Asked Questions
1. What are some common challenges in order picking?
Common challenges in order picking include inaccurate picking, slow pick rates, inventory errors, and inefficient warehouse layouts. These challenges can lead to customer dissatisfaction and increased operational costs.
2. How can I improve pick accuracy in my warehouse?
To improve pick accuracy, invest in employee training, implement technology solutions like barcode scanning, conduct regular quality checks, and maintain an organised warehouse layout.
3. Is batch picking or wave picking better for my business?
The choice between batch picking and wave picking depends on your business’s size and complexity. Batch picking is suitable for smaller operations, while wave picking is more efficient for larger, high-volume warehouses.
4. What role does technology play in order picking?
Technology, such as warehouse management systems (WMS) and order management software, plays a significant role in optimising order picking. It helps streamline processes, reduce errors, and improve overall efficiency.
5. How can I measure the effectiveness of my order picking process?
You can measure the effectiveness of your order picking process by tracking key performance indicators (KPIs) like pick accuracy, picking rate, and order cycle time. Use this data to identify areas for improvement and make data-driven decisions.
By implementing these strategies and best practices, you can elevate your order picking game and ensure that your customers in Australia and New Zealand receive their orders accurately and on time.
Remember, mastering the art of order picking is an ongoing journey, and continuous improvement is key to staying competitive in today’s market.
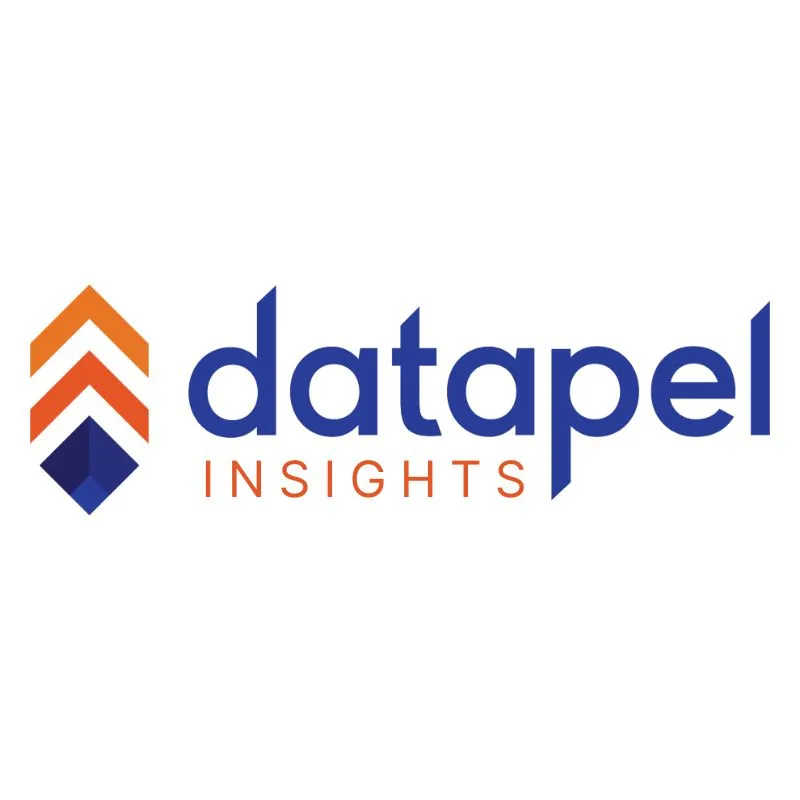
In my role, I oversee the development of insightful blogs that delve into the intricacies of warehouse management. Each piece reflects my dedication to empowering businesses through informative content. Through my team’s extensive experience in the industry, we aim to bring clarity to the complexities of WMS, helping businesses make informed decisions.
Join me on a journey through the ever-evolving landscape of warehouse technology as we explore the latest trends, industry insights, and practical tips to streamline your operations. Feel free to connect, and let’s embark on a collaborative exploration of how WMS can redefine your business efficiency.
Cheers to innovation, efficiency, and the exciting world of warehouse management!