Reduce Returns and Improve Customer Satisfaction with Smart Strategies
Contents
For retailers, wholesalers, and manufacturers, returns can be a big problem. They eat into profits, waste time, and upset customers. However with better inventory management, you can reduce returns and improve customer satisfaction.
Let’s look at how improving your inventory practices with help from systems like a warehouse management system (WMS), can solve these issues.
Why Returns Happen: Common Problems
Knowing why returns happen is the first step to fixing them. Here are some common reasons:
Wrong Items Sent
Mistakes in picking and packing often lead to customers receiving the wrong product. Whether it’s the wrong size, colour, or model, these errors cause frustration and extra shipping costs.
Damaged Goods
Bad handling, poor packaging, or improper storage can result in products arriving damaged. This is especially bad for fragile or perishable items.
Inaccurate Stock Levels:
Without accurate stock data, businesses might oversell or send items that aren’t actually in stock. This leads to delays, replacements, or incomplete orders, which often result in customer complaints and returns.
All these problems come from inefficiencies in inventory management. Fixing them reduces returns and keeps the loyal customers happy.
How Better Inventory Management Helps
Good inventory management is the backbone of a smooth supply chain. Here’s how it can significantly reduce returns:
- Improved Accuracy: Tools like barcode scanning and batch tracking help ensure the right products are picked, packed, and sent. These features minimise human error.
- Safer Storage and Handling: Clear guidelines for storing products and tracking their movement reduce the chances of damage during storage or shipping.
- Real-Time Stock Visibility: A WMS like Datapel gives you up-to-date information about your stock. This stops overselling and ensures your team knows what’s available.
- Meeting Customer Expectations: With accurate stock data, you can set realistic delivery times and avoid disappointing customers with delays or substitutes.
- Automated Processes: Eliminate manual order processing through automation and get returned items back in your store faster.
Steps to Reduce Returns and Improve Customer Satisfaction
Reducing returns isn’t just about using the right tools; it’s also about taking the right steps. Here’s what you can do:
Check Your Processes
Take a close look at your operations to identify weak spots. Are picking and packing mistakes common? Is your stock data often out of date? Focus on areas that frequently cause errors and returns and optimise stock rotation.
Train Your Team
Make sure your staff understands best practices for inventory management and knows how to use tools like barcode scanners and batch tracking effectively. Regular training sessions ensure your team stays sharp and up to date.
Organise Your Warehouse
A well-organised warehouse makes it easier for staff to find the right items quickly and without errors. Group products logically, such as by type, product descriptions or frequency of orders, and clearly label storage locations.
Double-Check Orders
Before an order is shipped, have a second person review it to ensure accuracy. This is especially important for customer orders of high-value items or those prone to returns.
Use Quality Packaging
Invest in sturdy, protective packaging to prevent damage during transit. For fragile items, use bubble wrap, foam inserts, or other cushioning materials to keep products safe.
Improve Stock Visibility
Real-time inventory tracking ensures you always know what’s in stock, preventing overselling and delays. This helps you fulfil orders accurately and on time to maximise customer satisfaction.
Establish Clear Return Policies
Set clear guidelines for returns to manage customer expectations. Provide detailed instructions on how to return items and make the returns process as smooth as possible for both your team and the customer. Offer store credit where possible to keep them engaged.
Leverage Customer Feedback
Pay attention to why customers return products. Look for patterns in the feedback, such as the return rates or complaints about sizing, quality, or packaging. Use this information to make improvements.
Conduct Regular Audits
Regularly check your inventory for accuracy. Compare physical stock counts with your records to spot and resolve discrepancies before they cause problems.
Adopt the Right Technology
Implement a WMS like Datapel’s to streamline your processes. A robust system can automate repetitive tasks, minimise errors, and give you the tools needed to reduce returns effectively.
Why Reducing Returns Makes Customers Happier
Cutting down on returns doesn’t just save money and reduce costs; it also creates an outstanding customer service experience. Here’s how:
- Building Trust: Customers will stick with a business they can rely on. Sending the right products every time builds loyalty and trust.
- Clear Communication: Real-time inventory visibility lets you keep customers informed about their orders. This helps manage expectations.
- Quick Problem-Solving: When mistakes do happen, a good WMS helps you fix them fast, turning a bad experience into a positive one.
Customer Reviews
Reducing returns has ripple effects that go beyond the immediate transaction. Customers who receive excellent customer service and the right product on time are more likely to leave positive reviews and recommend your business to others.
These good reviews can attract new potential customers, creating a cycle of growth and trust. Repeat customers, meanwhile, are more valuable over time because they tend to spend more and cost less to serve than first-time buyers.
Building Trust
Transparency in your inventory management also strengthens relationships with other stakeholders, like suppliers or distributors. If you’re able to provide accurate forecasts or manage stock levels effectively, you’re seen as a reliable partner. This trust can lead to better terms, priority service, and smoother operations across your entire supply chain.
Also read: Efficient Returns Management Strategies
How Datapel’s WMS Can Help
Datapel’s Warehouse Management System is designed to make inventory management simple and efficient. Here are some key features that can help:
- Batch and Serial Number Tracking: This feature lets you track products from your warehouse to the customer. For industries like food and pharmaceuticals, batch tracking also ensures compliance and prevents serious errors.
- Barcode Scanning: Scanning technology removes the need for manual data entry, making picking and packing faster and more accurate. This means fewer wrong-item shipments.
- Customisable Workflows: Datapel’s WMS lets you create workflows that fit your business. For example, you can set up double-checking for high-value items to avoid errors.
- Valuable Insights: With instant access to stock data, you can confidently promise accurate delivery times, prevent overselling, and quickly fix any stock problems.
Conclusion
Returns don’t have to be a constant struggle. With the right inventory management practices and tools, you can cut down on errors, reduce returns, and keep your customers happy. Datapel’s WMS offers the features you need to make this happen.
Whether you’re in retail, wholesale, or manufacturing, a system that ensures accurate, efficient, and customer-focused operations is key to success. Ready to make product returns a thing of the past? Contact Datapel today to see how we can transform your inventory management.
By taking these steps and using the right tools, you’ll not only save money but also build customer relationships and a reputation for reliability. And that’s what keeps customers coming back.
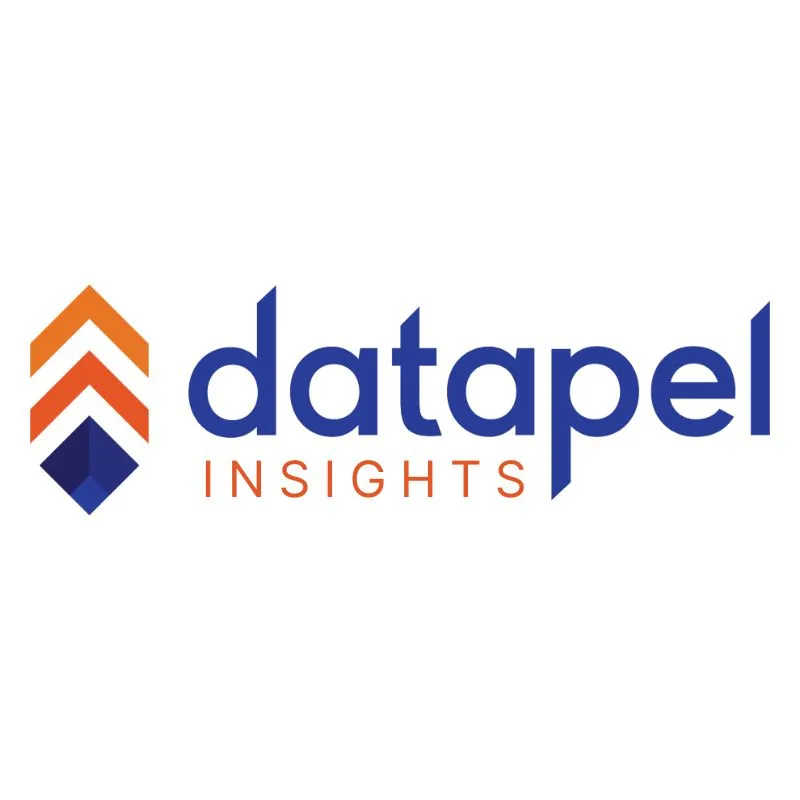
In my role, I oversee the development of insightful blogs that delve into the intricacies of warehouse management. Each piece reflects my dedication to empowering businesses through informative content. Through my team’s extensive experience in the industry, we aim to bring clarity to the complexities of WMS, helping businesses make informed decisions.
Join me on a journey through the ever-evolving landscape of warehouse technology as we explore the latest trends, industry insights, and practical tips to streamline your operations. Feel free to connect, and let’s embark on a collaborative exploration of how WMS can redefine your business efficiency.
Cheers to innovation, efficiency, and the exciting world of warehouse management!