Stockouts and How to Fix Them
Contents
In retail and warehousing, there’s nothing more frustrating than a stockout. It messes up your operations, lets down customers and ultimately hurts your profits. But what is a stockout and how can you prevent it in your business? Effective inventory management is key to preventing stockouts.
Stockouts are a big problem but businesses must also be careful of overstocking which can happen due to low sales and ongoing supply chain disruptions.
In this post, we’ll get into the details of stockouts and share practical tips to prevent them, including forecasting customer demand to prevent stockouts.
What is a Stockout?
A stockout is when out-of-stock items in inventory are not available for sale or use. This can happen for many reasons including poor inventory tracking, unexpected demand spikes, supply chain delays or poor inventory management practices. When stockouts happen customers will go elsewhere, lost sales and reputation, and poor inventory management will also result in excess inventory that must be written off.
Impact on Customer Satisfaction
Stockouts can have some big consequences for your business:
- Lost Sales: Customers can’t find what they want so they’ll go elsewhere.
- Customer Dissatisfaction: Frequent stockouts will annoy customers and damage your brand.
- Extra Costs: Emergency orders to top up stock will cost more due to rush shipping fees and lost economies of scale.
- Operational Disruption: Stockouts will stop production lines and delay order fulfilment and overall business efficiency.
- Poor Cash Flow Management: Poor cash flow management will lead to stockouts, missed sales, back ordering and customer service issues. Lack of working capital will prevent timely restocking and you’ll lose sales and customer satisfaction.
Types of Stockouts and Their Causes in the Supply Chain
Knowing the different types of stockouts and their causes will help you develop more targeted solutions to prevent them. Here are the common ones:
- Demand Stockouts: When demand for an item exceeds expectations, often due to poor forecasting or sudden market trends.
- Supply Stockouts: Caused by supply chain disruptions such as supplier delays, transportation issues or production problems.
- Administrative Stockouts: Caused by internal errors like poor inventory tracking, misplaced items or delays in reordering. Poor inventory tracking can also cause overstocking, resulting in excess inventory which will eventually become stockouts if not managed properly.
How to Prevent Stockouts with Inventory Management
Preventing stockouts requires a proactive approach to effective inventory management. Here’s how:
Get an Inventory Management System
Get a Warehouse and Inventory Management System like Datapel and you’ll see a big difference in your inventory control. Datapel allows you to track stock levels in real-time, set reorder points and automate replenishment so you’ll never be out of stock. Inventory management is key to preventing stockouts and maintaining optimal stock levels.
Forecasting
Use historical inventory data, market trends and seasonality to forecast demand accurately. This will allow you to maintain optimal stock levels and be prepared for peak periods without overstocking or understocking. Advanced forecasting tools can see patterns and provide insights that manual methods can’t.
Stock Audits
Conduct regular physical stock audits to ensure your actual stock matches your records. This will help you find discrepancies and fix them quickly. Regular audits will also help you find slow-moving items so you can adjust your stock levels accordingly. Track inventory better by training staff to set up warehouse inventory for better tracking.
Supplier Management
Make sure to keep good relationships with your suppliers so you get goods on time. Have backup suppliers in place if your primary supplier has issues. Establish clear communication channels and negotiate good terms to ensure reliability and flexibility.
Safety Stock
Keep a buffer stock of critical items to absorb unexpected demand spikes or supply chain delays. The amount of safety stock needed will vary depending on your business and risk tolerance. Review and adjust your safety stock levels regularly as demand and supply conditions change. Consider each item’s risk profile, target fill rate, forecast accuracy, lead time and replenishment cycle to determine how much safety stock is needed.
Automated Alerts and Notifications
Set up automated alerts for low stock levels and reorder points. This will alert you before stockouts happen and you can act fast. Modern inventory management software can send alerts via email or SMS, reminding you to reorder stock. Inventory management software also automates workload, maintains good customer relationships and provides real-time metrics and reporting.
Lean Inventory
Practice lean inventory to minimise waste and maximise stock turns. This means having just enough stock to meet demand without overstocking. Lean will reduce carrying costs and free up capital for other investments.
Cloud Software to Prevent Stockouts
In today’s digital age cloud software has changed the game for inventory management. Cloud systems have many benefits:
- Real-Time Data: Cloud inventory management gives you real-time access to your inventory data anywhere. This means better decision-making and all stakeholders have up-to-date information.
- Scalability: Cloud solutions can scale with your business, grow with you and change inventory needs without having to invest in big hardware.
- Integration: Cloud systems can integrate with other business tools like eCommerce platforms, accounting software and customer relationship management (CRM) systems. This will streamline operations and overall efficiency.
- Cost Savings: By using cloud solutions you can reduce the cost of maintaining on-premises hardware and software. This is especially good for small to medium-sized businesses looking to optimise their operations.
Real-Life Example of Lost Sales
LoChlor was experiencing supply chain disruptions. By using Datapel’s automated alerts and safety stock they were able to maintain optimal stock levels and avoid production delays. Overall efficiency improved.
Check them out: LoChlor Chemicals
End of Story
Stockouts are a fact of life but with the right strategies and tools, you can manage them. Datapel’s Order and Warehouse Management System has everything you need to keep accurate stock levels, forecast demand and automate replenishment. Try these and you’ll reduce costs, improve efficiency and have total inventory control so you never stock out your customers again.
Ready to get in control? Contact Datapel today to stop stockouts and simplify your operations.
Stockout FAQs
1. What is a stockout?
A stockout is when an item that is supposed to be in stock is out of stock and not available for sale or use. Stockouts can occur for many reasons such as inaccurate inventory tracking, sudden demand spikes, supply chain delays or poor inventory management. They can result in lost sales, customer dissatisfaction, extra costs and operational disruptions.
2. What does stocked out mean?
“Stocked out” means the item is not in stock at the moment. It means the inventory for that item is zero and can’t be sold or used until it’s replenished. This term is used in retail, warehousing and logistics to describe a product that’s not in stock.
3. What are stockouts in logistics?
In logistics stockouts means the absence of goods in inventory when they are needed for order fulfillment or production. Stockouts in logistics can disrupt the supply chain and cause delays in delivering products to customers or stop production. Good logistics management means minimising stockouts by keeping accurate inventory levels and a smooth supply chain.
4. What’s the difference between shortage and stockout?
A shortage means the supply of a product or resource is not enough to meet demand. This can be at a bigger scale and can be due to production issues, supply chain disruptions or increased demand across the whole market. A stockout is more specific to an individual business or location and means an item is out of stock and not available for sale or use at that time. All stockouts are shortages but not all shortages are stockouts; a shortage can mean reduced availability, not total unavailability.
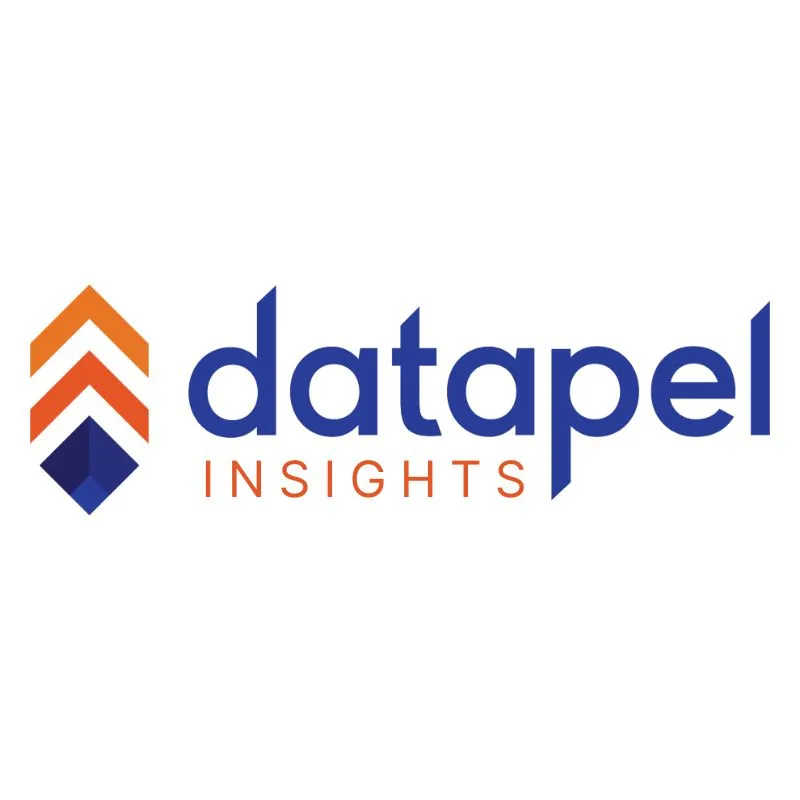
In my role, I oversee the development of insightful blogs that delve into the intricacies of warehouse management. Each piece reflects my dedication to empowering businesses through informative content. Through my team’s extensive experience in the industry, we aim to bring clarity to the complexities of WMS, helping businesses make informed decisions.
Join me on a journey through the ever-evolving landscape of warehouse technology as we explore the latest trends, industry insights, and practical tips to streamline your operations. Feel free to connect, and let’s embark on a collaborative exploration of how WMS can redefine your business efficiency.
Cheers to innovation, efficiency, and the exciting world of warehouse management!