Uncovering Warehouse Bottlenecks: Effective Strategies for Improvement
Contents
Warehouse management is key to keeping the operation running smoothly and meeting customer demand. But even small warehouse bottlenecks can slow you down, increase costs and impact service levels.
This guide will show you how to find these bottlenecks and use automation to improve your operation through continuous improvement.
What Causes Supply Chain Bottlenecks in Warehousing?
Bottlenecks occur when a process can’t keep up with the workload and it backs up the whole operation. In a warehouse these can be caused by:
- Manual Sorting: Research shows a third of warehouse workers spend over 50% of their time on manual tasks. Without automation, inefficiencies multiply, labour costs increase and it’s hard to manage high volumes of orders.
- Complex Processes: When staff have to remember item locations or decipher complex labels, sorting becomes prone to errors and delays.
- Peak Season Pressure: In peak season, small inefficiencies magnify. A few seconds per package can add up to big time, missed service level agreements (SLAs) and customer dissatisfaction.
Supply chain management is key to preventing these bottlenecks by forecasting demand, communicating and using technology for better visibility and decision-making.
Identifying Bottlenecks in the Warehouse
Identifying bottlenecks in the warehouse is crucial for maintaining a smooth and efficient supply chain. Bottlenecks can occur at any stage of the warehouse process, from receiving to shipping, and can significantly impact the entire supply chain. By pinpointing these bottlenecks, you can implement targeted solutions to enhance overall efficiency and prevent supply chain disruptions.
Data Collection and Analysis
To find bottlenecks in the warehouse you need to collect and analyse data on various aspects of the warehouse operation. This includes data on inventory levels, lead times, cycle times and other key performance indicators (KPIs).
By analysing this data warehouse managers can spot trends and patterns that indicate bottlenecks. Using supply chain data gives you a more precise view of where the delays and inefficiencies are occurring so you can take proactive action to fix supply chain bottlenecks.
Key Performance Indicators (KPIs)
KPIs are metrics that measure the warehouse operation. Common wa are:
- Lead Time: Time from receiving to shipping.
- Cycle Time: Time to process a product through the warehouse.
- Inventory Levels: Amount of inventory in the warehouse.
- Fill Rate: Percentage of orders filled and on time.
- Order Accuracy: Percentage of orders accurate and error-free.
By monitoring these KPIs you can see how the operation is performing and where bottlenecks may be occurring.
Lead Time, Cycle Time, and Inventory Levels
Lead time, cycle time and inventory levels are key KPIs that can indicate bottlenecks in the warehouse. By analysing these metrics you can see where bottlenecks may be:
- Lead Time: Long lead time means bottlenecks in receiving or shipping.
- Cycle Time: Long cycle time means bottlenecks in processing or picking.
- Inventory Levels: High inventory levels mean bottlenecks in storage or entire supply chain.
By understanding these metrics you can take targeted action to improve warehouse efficiency and prevent supply chain bottlenecks.
Manual Systems Have Limits
Manual processes work fine in normal circumstances but struggle under pressure. Without automation you can’t track productivity, accuracy and order status so managers are in the dark about the operation.
The result? More errors, less efficiency and no visibility for customers waiting for their deliveries.
Predictive analytics can help improve warehouse efficiency by forecasting bottlenecks and managing inventory through historical data analysis.
Strategic Automation: A Practical Approach
A full automation overhaul may not be possible for every warehouse. But strategic automation – implementing specific automated solutions to fix critical bottlenecks – can bridge the gap. This approach allows you to gradually move away from manual processes, and improve efficiency and accuracy without having to rip and replace the whole infrastructure.
Datapel’s Warehouse Management System (WMS) supports this by offering flexible inventory and workflow management. Datapel Cloud WMS has advanced barcode scanning, pick-and-pack workflows and multi-bin or location-based sorting all of which help to organise and direct items in complex warehouses.
Automation: The Way to More Efficient Warehouse Operations
Strategic automation including Datapel’s configurable workflows and API compatible systems can unlock your warehouse’s hidden capacity. By investing in targeted automation you can fix the inefficiencies that causes bottlenecks and get:
- More Productivity: Automating repetitive tasks lets your workers focus on value add activities, so your warehouse can do more with less.
- More Accuracy: Reduce human error in sorting and packing and orders will be fulfilled correctly, improve customer satisfaction.
- Deeper Insight: Integration with warehouse management system gives you real-time data to monitor and make data driven decisions.
- Cost Savings: Automation manages labour costs better, optimises floor space and energy efficiency.
Also fixing supply chain bottlenecks is key to efficient operations and can be done through strategic automation and technology integration.
Datapel WMS is designed to support automation at every step. From barcode tracking and custom reporting to multi-location management our software gives you the flexibility to implement automation solutions seamlessly.
Automation Tools to Simplify Warehouse Operations
Beyond flexible workflows there are many automation tools available today that can help warehousing and fix common bottlenecks. Solutions like sort-to-light systems and modular automation tools are automation options that can work with warehouse management systems to improve efficiency and accuracy across key processes.
- Sort-to-Light Systems: Sort-to-light (or put-to-light) solutions use visual cues to guide employees, reduce sorting errors by illuminating the correct bins for each item. Minimises time spent reading labels, gets new or temporary staff productive fast with minimal training.
- Modular Automation for Sorting: Modular sorting systems like SLAM/SPA (Scan, Label, Apply, Manifest) systems can handle complex parcel processing with ease. These systems can handle multiple parcel types and can be scaled to match warehouse demand, replaces manual sorting desks and optimise space.
- Advanced Analytics and IoT: AI and IoT gives you more insight by identifying bottlenecks and improving real-time decision making. By integrating with a WMS these tools can give you visibility into stock flow and manage resources better during peak seasons.
These tools give you many benefits – whether it’s reducing labour costs, improving accuracy or productivity. When combined with Datapel’s flexible workflows they are a way to fix inefficiencies and tackle supply chain bottlenecks.
Practical Steps to Tackle Warehouse Bottlenecks
Implementing automation can feel overwhelming, but you can start small and build up gradually. Here’s how you can begin:
- Identify Bottlenecks: Use data to find where delays occur, sorting, picking or packing. Look for tasks that waste time and resources.
- Choose the Right Automation Tools: Select automation solutions that target your bottlenecks. Start with sort-to-light for sorting tasks or modular solutions for parcel processing.
- Integrate with Existing Systems: Use a WMS to connect new automation tools to your existing processes, give you a single view of operations and smoother workflows.
- Train Staff Quickly: With sort-to-light systems staff can be operational fast, reduces downtime and training costs.
- Monitor and Optimize: Use real-time data from your WMS to track performance, find areas to improve and adjust processes as needed to optimise.
Disruptions in global supply chains, caused by factors such as the COVID-19 pandemic, labour shortages, and geopolitical tensions, can significantly impact warehouse operations. Addressing these disruptions with agile supply chain management strategies is crucial for maintaining efficiency and competitive advantage.
Inventory Management
Inventory management is a key part of warehouse operations and optimising the way you manage your inventory can fix bottlenecks. Optimised workflows means the right products are in the right place at the right time, reduced delays and improved overall warehouse efficiency.
Inventory Control and Reduction
Inventory control and reduction can fix bottlenecks in the warehouse. This includes:
- Just-in-Time (JIT): Reducing inventory levels by receiving stock as it’s needed in the production process.
- Inventory Management: Tracking and managing inventory levels with advanced software to get accurate and real-time data.
- First-In, First-Out (FIFO): Selling or using older stock before new stock to prevent obsolescence and reduce storage costs.
- Lean operations: Minimise excess inventory and streamline operations.
By following these steps warehouse managers can improve inventory management, reduce costs and fix bottlenecks and ultimately improve warehouse and supply chain operations.
Configurable Workflows
Datapel WMS has highly configurable workflows that simplifies and enhances sorting processes, allows warehouses to direct inventory to specific bins or areas based on real-time needs.
With modular configurations, users can configure workflows to match changing demands, such as dynamically re-assigning order-picking tasks based on bin locations and stock levels. This simplifies manual sorting steps, reduces errors, increases sort accuracy improves supply chain efficiency and reduces costly bottlenecks.
Datapel WMS key workflow features:
- Smart Inventory Allocation: Multi-bin and multi-location-based sorting allows warehouses to direct items to specific bins based on bin location and stock levels, reduces manual handling and increases sort accuracy.
- Automated Task Distribution: Configurable workflows mean dynamic task assignment, reduced time spent on manual re-assignment allowing staff to focus on high-priority tasks and increase productivity.
- Real-Time Inventory Visibility: With real-time updates managers can see stock locations, order status and inventory levels across all warehouse zones to make proactive decisions and get on time fulfilment.
With these workflows, Datapel WMS allows for smooth item movement and optimises manual processes even in high-speed or high-turnover environments where accuracy and speed are critical.
Get the Most Out of Your Warehouse with Datapel
Bottlenecks can limit your warehouse’s performance but they don’t have to. By investing in strategic automation and using Datapel’s WMS you can increase productivity, accuracy and visibility and reduce costs and provide better service to your customers.
Ready to fix your warehouse bottlenecks? Contact Datapel today to see how our WMS can help you transform your operations and get more efficiency.
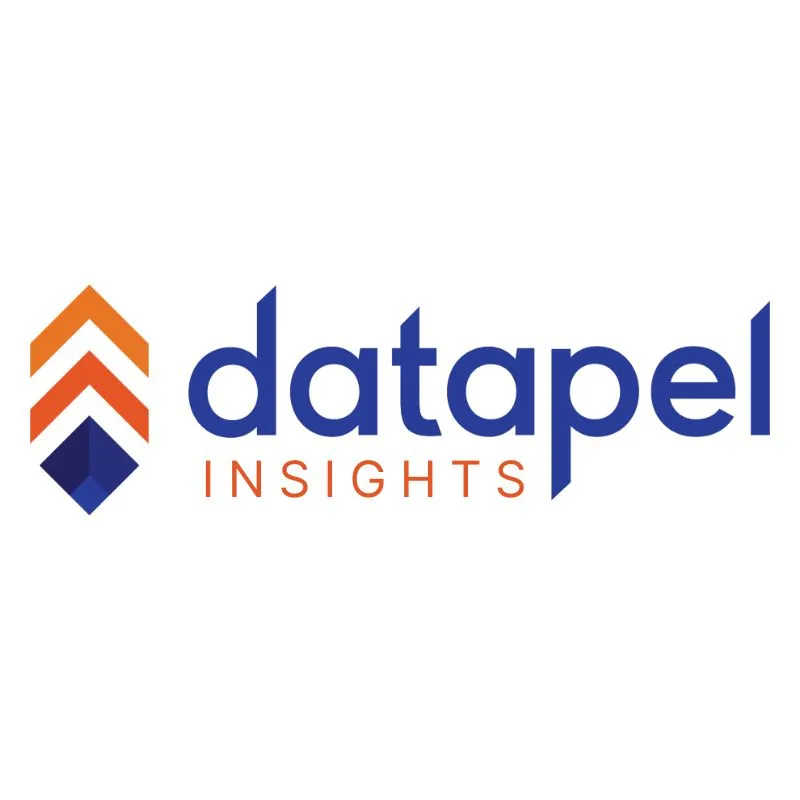
In my role, I oversee the development of insightful blogs that delve into the intricacies of warehouse management. Each piece reflects my dedication to empowering businesses through informative content. Through my team’s extensive experience in the industry, we aim to bring clarity to the complexities of WMS, helping businesses make informed decisions.
Join me on a journey through the ever-evolving landscape of warehouse technology as we explore the latest trends, industry insights, and practical tips to streamline your operations. Feel free to connect, and let’s embark on a collaborative exploration of how WMS can redefine your business efficiency.
Cheers to innovation, efficiency, and the exciting world of warehouse management!