Mastering Stocktake: Proven Strategies for Success
Contents
As the financial year approaches its end, it becomes important to conduct a comprehensive stocktake of your inventory.
If you are a business owner, the task of stocktaking can feel overwhelming. To assist you in mastering this process, we have created a practical guide that will help you conduct a stocktake like a pro.
What is stocktaking?
Stocktaking, which is also referred to as inventory counting or inventory audit, is the procedure of physically counting and validating the amount and condition of goods or assets possessed by a company.
It entails comparing the real stock available with the records kept in the company’s inventory management system. The level of complexity involved in stocktaking can differ depending on the industry.
For instance, a clothing store would allocate dedicated time to count and document the number of clothing items they have. Employees would move through the store, counting and recording each item using either a stocktake sheet or a barcode scanner connected to an inventory system.
After the counting is finished, the recorded stock levels are compared to the expected levels in the system. Discrepancies are investigated and reconciled to maintain accurate inventory records.
Why are stocktakes important?
Inventory management and stocktaking play a significant role in driving down supply chain costs. This reduction in costs can potentially double your profits by reducing them from 9% to 4%.
For product-based organisations, it is crucial to maintain optimum inventory levels as part of the inventory control mechanism. In fact, in several countries, it is a legal obligation to do so. Even if not legally required, there are compelling reasons to conduct stocktaking.
Stocktaking helps accurately assess inventory levels, identify discrepancies between recorded and actual stock, detect theft or pilferage, and facilitate efficient inventory management and financial reporting.
By regularly conducting stocktaking, you gain better control over your assets, optimise ordering and production processes, and maintain accurate financial records. This ultimately contributes to cost reduction and improved profitability.
How to Stocktake?
Now that we have established the importance of stocktaking in your business, let’s look at the different steps you must follow for a systematic stocktaking process.
1. Plan your stocktake
Before you start your stocktake, it’s important to plan ahead. This will help you keep track of your inventory more effectively. For example, make sure you have all the necessary tools readily available for the stocktaking process.
2. Choose the right time for your stocktake
When planning your stocktake, choose a suitable time that won’t clash with or disrupt your normal business operations.
Select a time when you can focus without feeling rushed and with minimal distractions. This will allow you to dedicate your full attention to the stocktaking process, ensuring accuracy and efficiency.
3. Assign supervisors for each stocktake location
Stocktaking can be a complex process, so it’s beneficial to have a dedicated supervisor at each stocktake location. This supervisor will help coordinate your workers and ensure that everything runs smoothly.
4. Provide training and guidance to your employees
Ensure that your employees are well-informed about their roles and responsibilities during the stocktake. Equip them with the necessary tools, such as stocktake sheets and pens, to help them accurately record the items they have counted.
5. Consider employing temporary staff
If you are conducting the stocktake during business hours, consider hiring temporary employees to assist with the process. This allows your regular staff to continue serving customers while the stocktake is underway.
6. Explore the option of running a stocktake sale
Performing a stocktake can be more expensive when you have a large amount of inventory. To reduce your stock levels before the stocktake, you can consider running a stocktake sale.
This not only helps lower your inventory but also offers benefits such as increased sales, improved customer satisfaction, and the opportunity to sell items before they become outdated or go out of season.
6 Stocktaking Best Practices to Help You Succeed
Clearly, stocktaking is no walk in the park. It can be time-consuming, tiring, and frustrating for anyone involved. Without a clear plan, there’s a risk of serious errors. While there’s no magic formula, there are several ways to improve your chances of success.
Here are 6 helpful tips to guide you.
1. Plan and Schedule in Advance
Create a clear plan and schedule for your stocktake in advance.
Allocate resources and consider involving friends or family to help with the counting process. Remember, many hands make light work. Prepare for potential downtime during the count and avoid rushing this stage to ensure accuracy and efficiency.
2. Define Clear Goals and Responsibilities
Appoint a champion or project leader to coordinate the stocktake. If possible, designate a Counter Team Leader and a Data Entry/Analysis Team Leader to manage specific tasks and responsibilities effectively.
3. Only Use Current or Updated Inventory Data
Ensure that all received orders are closed and shipped orders are cleared both in the system and physically before taking a snapshot of your inventory. If necessary, quarantine any items that should not be included in the count.
4. Use a Barcode Scanner
To minimise errors and increase efficiency, consider using a barcode scanner. This technology allows you to quickly record stock levels while storing the data simultaneously. Barcode scanners provide a reliable way to manage large amounts of data accurately.
5. Consider using Dedicated Stocktaking Software
Manual stocktaking processes, especially when relying on spreadsheets, can be cumbersome and prone to inaccuracies. Switching to specialised stocktaking software can greatly improve precision and expedite the procedure.
6. Understand What and How to Count
Before starting your stocktake, make sure you know what items to count and decide how you will count them (individual items, cases, or pallets). Establish guidelines for handling scenarios like damaged items, returns, or items in transit.
For instance, you can use colour-coded sticky notes to tag stock groups. Remove or change the note colours as you progress to visually track completed and remaining tasks.
Also read: 10 Tips for an Effective Stock Count Without a WMS
How can Datapel help you?
As a business owner, managing your inventory stock is crucial. It affects production planning, resource allocation, and understanding of customer demand.
That’s where Datapel can help! With Datapel, stocktaking becomes easier than ever.
It’s a scalable and cost-effective inventory management solution that grows with your business. You can track sales, inventory levels, and profits accurately, ensuring you have all the information you need to stay compliant and successful.
Embrace a simpler, more efficient way to manage your stock with Datapel. Find out more about Datapel Stock Count Manager
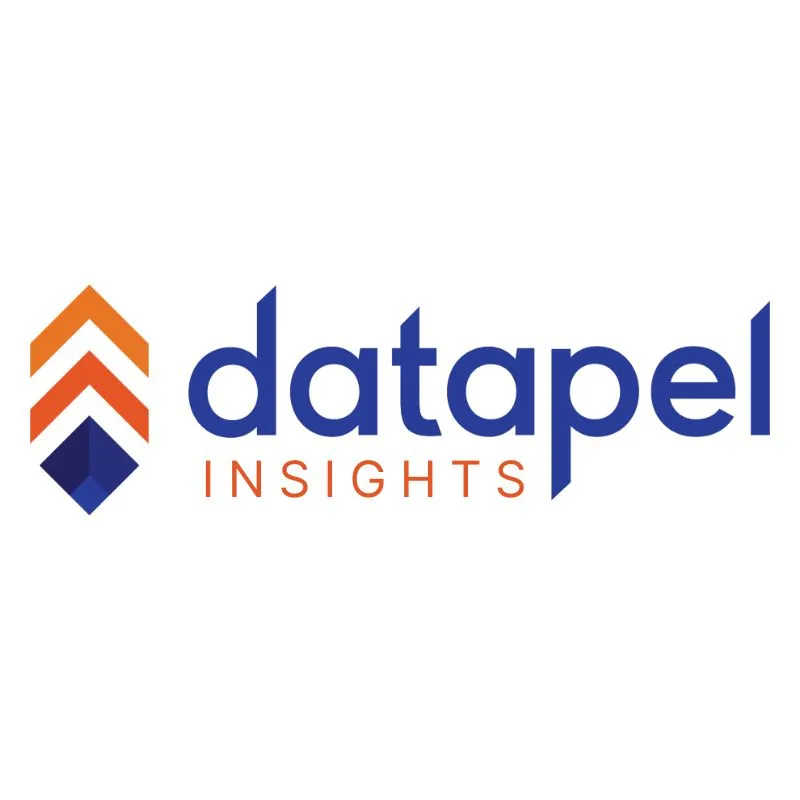
In my role, I oversee the development of insightful blogs that delve into the intricacies of warehouse management. Each piece reflects my dedication to empowering businesses through informative content. Through my team’s extensive experience in the industry, we aim to bring clarity to the complexities of WMS, helping businesses make informed decisions.
Join me on a journey through the ever-evolving landscape of warehouse technology as we explore the latest trends, industry insights, and practical tips to streamline your operations. Feel free to connect, and let’s embark on a collaborative exploration of how WMS can redefine your business efficiency.
Cheers to innovation, efficiency, and the exciting world of warehouse management!