5 Powerful Benefits of Paperless WMS Software
WMS software (warehouse management software) adoption is increasing. However, many smaller warehouses still rely on manual systems causing them to lag behind larger organisations in modernising their operations.
Some smaller warehouses record information on paper and then enter data in spreadsheets to monitor inventory, plan storage schemes, schedule labour, and manage goods movement.
Other small warehouses may have implemented custom tools based on Microsoft Access databases, FileMaker, or other business applications. However, in a busy warehouse with limited staff, these tools may demonstrate performance problems or other signs that they haven’t been maintained properly.
Furthermore, the person who developed them may have moved on to a different position or retired, an all-to-familiar story since The Great Resignation amplified the challenges created by the labour and skills shortage in nearly every sector.
To reduce dependence on specific employees or paper-based systems and upgrade to a future-proof strategy, warehouses of all sizes will benefit from implementing WMS software. Warehouses that transition to a WMS gain many improvements in their day-to-day operations.
Benefits of Paperless WMS Operations
Faster Training Time
Training can take months of shadowing experienced team members so new hires can learn the step-by-step processes required to follow paper orders, complete tasks, and accurately record data.
In warehouses that have historically experienced high turnover rates, it’s possible staff can’t train people fast enough to maximise productivity and never get costs under control. In addition, warehouses that rely on experienced team members to pass on their knowledge would be at a loss if those employees resigned.
With WMS software, warehouses can automate training. Employees receive role-based instruction via PDAs or other mobile devices, helping them focus on one task at a time rather than trying to learn the entire system.
For example, new hires can jump right into directed picking with a system that tells them precisely what to pick and where to find the right SKUs. Once the employee has completed a task, the order status changes. This can act as a trigger that notifies supervisors that the employee is ready for new assignments.
Additionally, with guided instruction, scaling staff with temporary workers to handle picking and receiving during peak season is also streamlined.
The training process becomes more streamlined, more straightforward, and more effective. It also helps build collaboration between team members and eliminates data silos so that managers and business leaders can monitor new hires’ progress and the status of projects.
More Productivity with Fewer Employees
WMS software accessible on mobile devices doesn’t only benefit new employees. It helps all employees increase their productivity. Paper orders require employees to stop what they’re doing after each job and retrieve their next orders. Those added steps take time – time that employees could spend on more productive work.
Additionally, when an employee returns paper orders, that employee or a support person has to enter information in the warehouse’s database or spreadsheets.
A paperless warehouse allows employees to move seamlessly from one task to the next with no wasted steps in between, increasing their productivity.
Employees with mobile devices can also enter data into the WMS at the point of the task, eliminating the need to enter it later. The warehouse can reassign people responsible for data entry to other tasks, further increasing overall business efficiency.
Reduce the Possibility of Human Errors
When processes rely heavily on humans, there is always the chance of human error. Handwriting can be difficult to read, especially if employees are under pressure to move quickly, and data can become smudged when employees work in an industrial environment. Moreover, employees can tear or misplace paper, leading to data loss.
Web based WMS software eliminates those pitfalls. Employees receive directions on mobile devices, down to bin and SKU levels.
Transitioning to a paperless warehouse allows employees to verify items again before they are packed and shipped, helping teams achieve near-perfect order accuracy. As a result, those software-directed checks and balances lead to fewer mis-ships, lower costs and happier customers.
Make the Most of Your Capital and Your Space
Paper-based inventory management processes can result in costly errors. Inaccurate inventory data may indicate that your warehouse is low or out of stock on an item and could even trigger a purchase order. However, when the order arrives, it becomes evident that stock was not low, and now capital is tied up in unneeded inventory.
Additionally, your team now has to rework the warehouse layout to accommodate the excess inventory.
WMS software allows you to maintain accurate inventory records that inform the correct purchasing decisions. It also helps you choose the best layout for your warehouse to make the best use of every square foot of space and enhance picking efficiency.
A WMS can even offer multi-binning, which enables locating two or more SKUs in the same bin for storage efficiency. Furthermore, WMS software can guide a team through first-in, first-out (FIFO) picking to minimise old, outdated, or expired stock.
Better Visibility and Reporting
With paper-based processes, there is always a delay from the time an employee performs work until data is recorded in a spreadsheet. However, WMS software solutions enable complete visibility into your entire operation, from orders to shipments, in real time.
Automated processes coordinated on your WMS software give you the advantage of a comprehensive set of standard reports covering inventory management, purchase, and sales orders for complete visibility.
Cloud based WMS software also provides traceability for each step of your processes, enabling documentation and an audit trail in case there is a dispute.
Detailed records from your WMS show the items picked and packed, shipping information, and even the weight of the shipment, which can support your case that you fulfilled the order as promised.
Without a WMS, determining what went wrong can take significant time as you dig through paperwork and may mean you can’t back up your claims that you fulfilled and shipped orders correctly.
Future-Proofing Your Warehouse Operations with Paperless WMS Software
While it will take planning, effort, and time to implement a WMS, the payoff will include positioning your operation better to keep up with industry changes and to meet customer demands. WMS software also streamlines and digitises processes, making your operation less dependent on employees.
Get ahead of the uncertain labour market and future-proof your operation by moving to a paperless warehouse with cloud-based WMS software.
FAQs
1. Why should I switch from spreadsheets to WMS software?
If you’re managing your warehouse with spreadsheets, you’re probably familiar with the headaches of manual updates, data errors, and wasted time. A Warehouse Management System (WMS) takes the guesswork out of inventory management. It automates repetitive tasks, improves accuracy, and gives you real-time insights into your operations—all things spreadsheets can’t do. Think of it as upgrading from a bicycle to a car for your warehouse processes!
2. Is WMS software expensive?
Not at all! Today’s WMS software is designed to be flexible, so even small businesses can find affordable solutions. Many systems are cloud-based, meaning you don’t need to worry about hefty upfront costs. Instead, you can choose a pricing plan that fits your business size and grow with it as your warehouse scales.
3. Will WMS software really save me time?
Absolutely. With WMS software, your team won’t need to shuffle between paperwork and spreadsheets. Tasks like picking, packing, and inventory updates are managed digitally, so employees can move seamlessly from one job to the next. That’s more time spent on getting orders out the door—and less on admin.
4. Is it hard to train my team on WMS software?
Not at all! A good WMS comes with intuitive tools and step-by-step training modules. Employees can use handheld devices to get real-time instructions, so they don’t need to memorise complex workflows. It’s especially handy if you hire temporary workers during busy seasons—they’ll hit the ground running in no time.
5. How does WMS software help reduce errors?
Ever dealt with messy handwriting or misplaced paperwork? WMS software eliminates these issues. Employees receive clear instructions on mobile devices and update data in real time. Plus, features like barcode scanning and automated checks ensure near-perfect order accuracy. That means fewer mistakes, happier customers, and cost savings for your business.
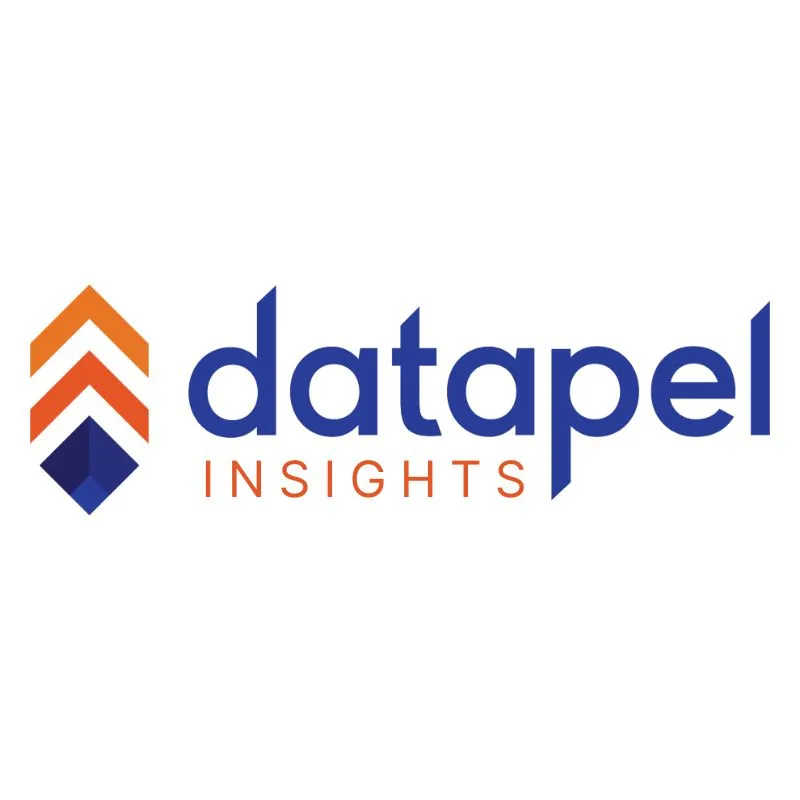
In my role, I oversee the development of insightful blogs that delve into the intricacies of warehouse management. Each piece reflects my dedication to empowering businesses through informative content. Through my team’s extensive experience in the industry, we aim to bring clarity to the complexities of WMS, helping businesses make informed decisions.
Join me on a journey through the ever-evolving landscape of warehouse technology as we explore the latest trends, industry insights, and practical tips to streamline your operations. Feel free to connect, and let’s embark on a collaborative exploration of how WMS can redefine your business efficiency.
Cheers to innovation, efficiency, and the exciting world of warehouse management!