How to Implement a Barcode System in Manufacturing
Contents
Implementing a barcode system in manufacturing can transform efficiency, accuracy, and traceability, making it an essential tool for inventory management and supply chain visibility. Whether you’re looking to streamline inventory tracking, improve order fulfilment, or ensure regulatory compliance, a well-designed barcode system is a game-changer.
In this guide, we’ll walk you through the implementation process and show you how Datapel’s Cloud WMS can take your barcode workflows to the next level.
Why Use a Barcode System in Manufacturing?
Barcodes take the hassle out of tracking and reduce mistakes from manual entry, making manufacturing operations smoother and more efficient. By scanning a barcode, your team can instantly access real-time data, track materials, and move goods through production efficiently. A barcode inventory system helps businesses streamline operations by ensuring inventory accuracy and reducing human error. Key benefits include:
- Enhanced Accuracy: No more manual errors—barcode scanning ensures precise tracking of materials, work-in-progress (WIP), and finished goods.
- Improved Inventory Management: Real-time updates help prevent stock shortages or overstocking.
- Increased Productivity: Scanning barcodes is faster than writing down or typing data manually.
- Better Traceability: Track every product from raw material to finished goods.
- Cost Efficiency: Reduces labour costs and minimises waste.
- Compliance & Quality Assurance: Meets industry regulations while ensuring high production standards.
Step-by-Step Guide to Implementing a Barcode System in Manufacturing
1. Define Your Objectives
Before rolling out a barcode system, clarify your goals. Are you looking to:
- Track raw materials?
- Monitor WIP more effectively?
- Improve inventory accuracy?
- Ensure compliance with industry standards?
By understanding your priorities, you can tailor the system to meet your needs.
2. Assess Your Current Processes
Evaluate your existing production processes and workflows to determine where barcoding will bring the most value. Identify manual processes that can be automated and areas prone to errors or inefficiencies.
3. Choose the Right Hardware
Choosing the right tools is key to making your barcode system work smoothly. Consider:
- Barcode Printers: Ensure they support 1D and 2D barcodes if required.
- Scanners: Handheld or fixed scanners depending on your setup.
- Labels: Durable labels that can withstand manufacturing conditions like heat, chemicals, or abrasion.
4. Select the Right Barcode Symbology
Different barcode data types suit different applications:
- 1D Barcodes (e.g., Code 128): Ideal for encoding product codes.
- 2D Barcodes (e.g., QR Codes, GS1 DataMatrix): Suitable for complex data, such as batch numbers or expiry dates.
If your industry requires compliance with GS1 barcode standards, Datapel Cloud WMS fully supports GS1 barcodes for seamless global supply chain accounting systems integration, helping manufacturers implement a barcode system that improves inventory accuracy and enhances traceability.
5. Integrate with Your Existing Systems
Your barcode system should work seamlessly with your Warehouse Management System (WMS) or Enterprise Resource Planning (ERP) software, ensuring inventory management processes run efficiently and tracking key metrics is effortless. This integration ensures that every scan updates your inventory system in real time, helping you avoid errors, speed up processes, and improve overall efficiency.
With Datapel Cloud WMS, barcode-based inventory tracking becomes effortless. From doing inventory counts to scanning incoming stock to managing multi-location tracking, everything stays connected in real-time.
6. Develop a Labelling Strategy
Decide on a standardised approach for labelling raw materials, WIP products, tools, and finished goods. Labels should include key details like product codes, lot numbers, or manufacturing dates.
7. Train Your Employees
Your barcode system is only as effective as the people using it. In a manufacturing setting, training employees to use barcode scanners and mobile devices correctly is key to ensuring accurate tracking of inventory items and minimising human error.
Imagine a team using barcode scanners incorrectly or skipping scans altogether—errors can still creep in. That’s why hands-on training is essential. Show employees how scanning improves accuracy, makes their jobs easier, and keeps operations running smoothly. Provide hands-on training to ensure employees understand how to:
- Use barcode scanners and printers.
- Scan at each step of production to maintain accurate data.
- Troubleshoot common scanning issues.
8. Test the System
Before rolling out across the entire facility, run a pilot test in a controlled environment. This allows you to:
- Identify bottlenecks.
- Fix scanner or label issues.
- Ensure seamless integration with other systems.
9. Roll Out Across the Facility
Once testing is successful, expand the implementation across all relevant areas in your manufacturing process. Ensure every workstation has the necessary scanners and labels.
10. Monitor & Optimise
Barcode systems should evolve with your business. Regularly review performance and resolve any inefficiencies, such as scanner malfunctions or incorrect label printing.
When Do You Need a Barcode System in Manufacturing?
If your manufacturing operations are facing inefficiencies, a barcode system can help. Here are some signs that indicate it’s time to implement a barcode inventory system:
- Frequent Stock Discrepancies – If your inventory records often don’t match actual stock levels, barcode scanning can improve accuracy.
- High Manual Data Entry Errors – Entering data manually is time-consuming and prone to mistakes. A barcode system automates data entry, reducing errors.
- Slow Order Fulfilment – If picking, packing, or shipping takes too long, barcode workflows can speed up the process.
- Difficulty Tracking Raw Materials and Work-in-Progress (WIP) – Barcodes enable real-time tracking of raw materials and production stages, ensuring smooth operations.
- Challenges with Compliance and Reporting – If your industry has strict regulations, a barcode system helps maintain audit-ready inventory records.
- Poor Supply Chain Visibility – Barcode integration provides real-time updates on stock movement, improving supply chain efficiency.
- Scaling Business Needs – If your business is growing and inventory complexity increases, a barcode system can scale with your operations.
Barcodes play a vital role in supply chain visibility, ensuring that businesses can track products from raw materials to final shipment. They also contribute to compliance and reporting, helping manufacturers adhere to industry regulations by maintaining accurate, audit-ready records.
Supported Barcode Workflows in Datapel Cloud WMS
With Datapel’s Cloud WMS, barcoding extends across multiple manufacturing workflows, ensuring efficiency and real-time tracking. Supported workflows include:
- Receiving & Goods Inwards: Scan barcodes upon receipt to verify stock against purchase orders. Supports batch and serial number capture.
- Stock Put-Away: Assign received goods to warehouse locations with barcode scanning.
- Inventory Management: Perform stocktakes in real-time by scanning items to check quantities, locations, and expiry dates.
- Order Picking: Guided barcode workflows ensure accurate picking, supporting wave, batch, and zone picking.
- Packing & Dispatch: Scan items before shipping to ensure order accuracy and attach shipping barcodes for tracking.
- Production Tracking: Track raw materials and WIP to maintain full traceability throughout the production cycle.
- Returns Management: Barcode scanning simplifies returns processing, ensuring correct identification and sorting.
- Replenishment: Identify low-stock items and assign replenishment tasks automatically.
GS1 Barcode Compatibility in Datapel Cloud WMS
For manufacturers needing GS1 barcode compliance, Datapel supports:
- GS1-128: Encodes batch numbers, expiry dates, and serial numbers—ideal for food, healthcare, and logistics.
- GTIN (Global Trade Item Number): Standardised product identification for retail and manufacturing.
- GS1 DataMatrix: A compact 2D barcode used in industries like pharmaceuticals for traceability.
- GS1 QR Code: Provides additional product details or marketing content via encoded URLs.
- SSCC (Serial Shipping Container Code): Tracks shipping containers and pallets.
How Datapel Supports GS1 Standards
- Product Identification: GS1 barcodes enable seamless scanning across the supply chain.
- Batch & Lot Traceability: Helps businesses track products from manufacturing to end-users.
- Expiry Date Tracking: Automates FIFO/FEFO stock rotation with quality control barcodes.
- Pallet & Shipment Tracking: Streamlines logistics processes.
- Compliance with Industry Regulations: Helps meet food safety (FSMA) and pharmaceutical (FMD) standards.
- Retail & E-commerce Integration: Ensures compatibility with trading partners and marketplaces.
- Supplier & Partner Collaboration: Facilitates smooth communication across the supply chain.
Frequently Asked Questions
What is a barcode in the manufacturing process?
A barcode in manufacturing is a visual representation of data that helps track and manage raw materials, work-in-progress items, and finished goods. By scanning barcodes, manufacturers can automate inventory management processes, reduce manual inventory data and entry, and enhance efficiency.
What are barcode systems?
Barcode systems consist of barcode labels, barcode scanners, and other inventory management software that work together to streamline operations. They help businesses improve inventory accuracy, track inventory items in real-time, and ensure seamless integration with other supply chain management tools.
How to use a barcode system for inventory?
Using a barcode system for inventory involves assigning barcode labels to products, raw materials, and storage locations. Employees scan barcodes using barcode readers or mobile devices to update inventory records, monitor inventory levels, and manage stock control. This improves efficiency, reduces human error, and uses inventory management barcodes to enable companies to track key metrics.
What is a barcode on a product from a manufacturer?
A barcode on a product from a manufacturer is a unique identifier used for inventory control, tracking and supply chain visibility. It typically includes a GTIN (Global Trade Item Number) or batch tracking barcodes that store product details, expiry dates, or serial numbers. These barcodes help manufacturers streamline operations, improve efficiency, and ensure regulatory compliance.
Final Thoughts
Still managing inventory the old way? A barcode system isn’t just nice to have—it’s a must for efficient operations and competitive stock control. By integrating barcoding with Datapel Cloud WMS, businesses gain real-time inventory visibility, seamless automation, and compliance with industry standards.
Looking to implement a full barcode inventory system for manufacturing? Book a demo to see how Datapel Cloud WMS can help you take control of your inventory with barcode-powered efficiency.
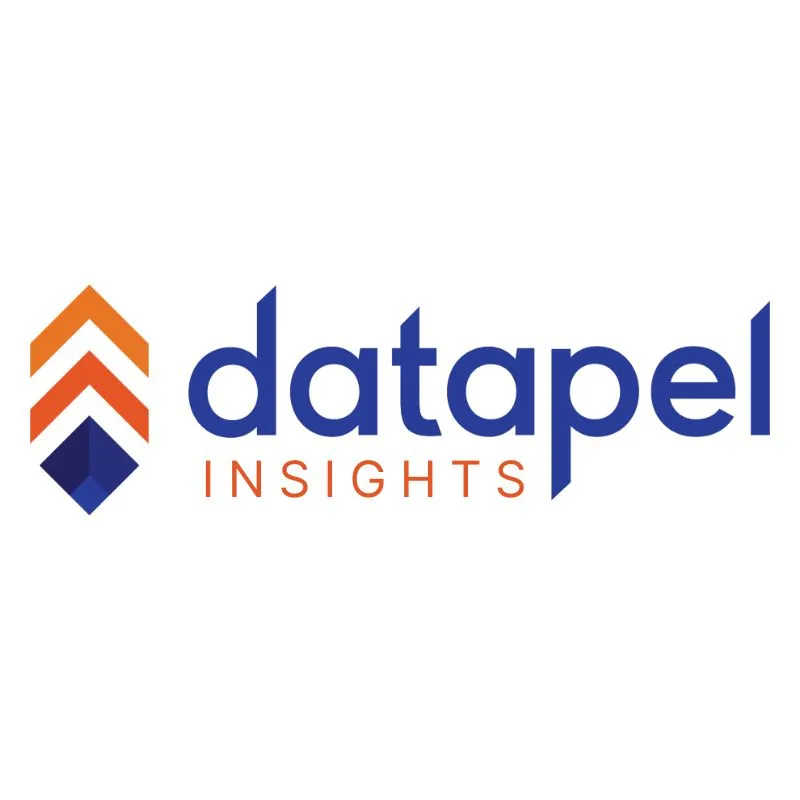
In my role, I oversee the development of insightful blogs that delve into the intricacies of warehouse management. Each piece reflects my dedication to empowering businesses through informative content. Through my team’s extensive experience in the industry, we aim to bring clarity to the complexities of WMS, helping businesses make informed decisions.
Join me on a journey through the ever-evolving landscape of warehouse technology as we explore the latest trends, industry insights, and practical tips to streamline your operations. Feel free to connect, and let’s embark on a collaborative exploration of how WMS can redefine your business efficiency.
Cheers to innovation, efficiency, and the exciting world of warehouse management!