Finished Goods Inventory: Definition, Formula, and Best Practices
Contents
Finished goods inventory is products that are fully completed and ready to sell to customers. This inventory is an asset on the balance sheet and is key to meeting customer demand while being operationally efficient.
Proper management of finished goods inventory ensures stock is available when needed, minimises excess inventory costs and keeps production flowing.
The finished goods inventory formula is key to managing inventory and cash flow as it helps you calculate inventory on hand, prevent stockouts and provide data for accounting and financial decisions.
In this article, we’ll define finished goods inventory, and explain the formulas and best practices.
What are Finished Goods?
Finished goods are products that have completed the entire manufacturing process and are now ready for sale to customers.
These are the result of a process that starts with raw materials and ends with a marketable product. Unlike raw materials or work in progress, finished goods are fully assembled, tested, packaged and ready to ship.
For example in the electronics industry finished goods would be fully assembled and packaged laptops or mobile devices. In the clothing industry finished goods would be ready-to-wear garments that have passed quality control and are ready to ship.
These products are stored in warehouses or distribution centres until they are shipped to customers or retailers.
What is Finished Goods Inventory?
Finished goods inventory includes all products that have gone through the production process, and quality control and are ready to sell. Unlike raw materials or work-in-progress (WIP) inventory finished goods are the result and are ready to ship to customers.
In financial reporting finished goods inventory is classified under inventory accounts as current assets as they have short-term value and can generate profit for the business.
For example in a business that manufactures electronics finished goods would be packaged laptops and mobile devices, inspected and ready to ship. This is different from WIP which is partially assembled products and raw materials which are basic components like circuit boards or screens.
From Raw Materials to Finished Goods
The journey from raw materials to finished goods goes through several stages, each is critical to the production process. It all starts with procurement of raw materials which are the basic inputs to create the final product. These can be sourced from suppliers or extracted from natural resources depending on the industry.
Once the raw materials are procured, they undergo the manufacturing process, including assembly, testing, and packaging to create a marketable product.
This can include assembly where components are put together; testing to ensure the product meets quality standards, and packaging to prepare the product for sale. Quality control is a critical step in this journey to ensure each finished good meets the specifications and is defect-free.
Finally, the distribution stage is where the finished goods are shipped to customers or retailers. This is key to getting the products to market on time and efficiently. By managing each stage well businesses can turn raw materials into high-quality finished goods that meet customer demand.
Why Finished Goods Inventory Matters
Having the right amount of finished goods inventory has several benefits:
- Accurate Valuation: Knowing the true value of your finished goods inventory or finished goods inventory value helps with financial reporting, budgeting and understanding of stock value which is critical for asset management.
- Demand Buffer: Finished goods inventory acts as a buffer to help you meet unexpected demand, maintain a steady supply and reduce the risk of stockouts.
- Cost Efficiency: By inventorying in bulk businesses can reduce production cost per unit and get economies of scale.
- Customer Satisfaction: Having the right amount of finished goods inventory allows for on-time order fulfilment, meets customer expectations and is more reliable.
- Better Cash Flow: Reducing excess inventory reduces storage costs and frees up capital to be re-invested in growth or other business needs.
How to Calculate Finished Goods Inventory
Calculating finished goods inventory accurately is critical to monitor stock levels and plan for future production. The formula is:
Finished Goods Inventory = Beginning Finished Goods Inventory + Cost of Goods Manufactured (COGM) – Cost of Goods Sold (COGS)
This finished goods inventory formula helps you know how much inventory is available for sale so you can manage your inventory well to avoid stockouts and optimise production and sales.
Let’s break it down:
- Beginning Finished Goods Inventory: This is the value of finished goods at the start of an accounting period, this is the starting point for inventory calculations.
- Cost of Goods Manufactured (COGM): This is the total cost to produce finished goods including raw materials, labour and overhead costs.
- Cost of Goods Sold (COGS): These are the direct costs of goods sold during the period including labour and material costs to calculate ending inventory value.
Example
A business has $40,000 in beginning finished goods inventory. During the period COGM is $150,000 and they sell goods totalling $120,000 in COGS. The ending finished goods inventory would be:
Ending Finished Goods Inventory = $40,000 + $150,000 − $120,000 = $70,000
Calculating finished goods inventory accurately helps you know your stock levels, track inventory value and plan financially.
Best Practices for Finished Goods Inventory Management
Here are four ways to manage finished goods inventory in the supply chain:
1. Conduct Regular Inventory Audits
Regular audits help maintain accurate inventory records and identify discrepancies between actual stock and recorded inventory. Audits can reveal old or unsellable stock help reduce waste and improve operational efficiency.
2. Use Inventory Management Software
Modern inventory management software provides real-time tracking and gives you insights into finished goods levels, demand forecasting and low stock alerts. By automating updates you can reduce errors and have instant access to inventory status.
3. Forecast with Precision
Accurate demand forecasting prevents overstocking or understocking, so you can meet customer demand without tying up capital in excess stock. Analyse historical sales data and market trends to get reliable forecasts that match production with demand.
4. Optimise with Just-in-Time (JIT) Strategy
JIT‘s inventory strategy is to hold only the stock for immediate demand, to reduce waste, free up cash flow and maintain stock levels that match production needs. Monitor turnover rates and adjust inventory levels accordingly to manage inventory effectively.
Common Mistakes in Finished Goods Inventory Management
Finished goods inventory management is crucial for any business but it can be tricky to get it right. Here are some common mistakes:
- Overstocking: Holding too much inventory can lead to waste, obsolescence and increased storage costs. You need to balance your inventory levels to avoid tying up capital in unsold goods.
- Understocking: On the other hand holding too little inventory can lead to stockouts, lost sales and disappointed customers. Make sure you have enough stock to meet customer demand.
- Inaccurate Forecasting: Failing to forecast demand accurately can lead to inventory imbalance and bad decisions. Analyse historical sales data and market trends to get more reliable forecasts.
- Poor Inventory Tracking: Without proper tracking of inventory levels and movements businesses can face discrepancies and lost sales. Implement robust tracking systems to maintain accurate records.
- Inadequate Inventory Management Software: Relying on old or inadequate inventory management software can lead to inaccurate tracking, bad reporting and poor decisions. Invest in modern inventory management software to streamline your operations and get real-time insights.
So avoid these mistakes by implementing good inventory management practices. This means using advanced inventory management software, tracking inventory levels and movements accurately and forecasting demand with precision.
By doing so you can improve your finished goods inventory management, reduce costs and improve overall performance.
Summary
Finished goods inventory management is key to balancing customer demand with cost-effective stock levels. Know your finished goods inventory calculation and follow best practices like regular audits, demand forecasting and optimised stock levels to reduce costs and increase customer satisfaction.
FAQs
What is finished goods inventory?
Finished goods inventory are products that are fully manufactured and ready for sale to customers. This includes all items that are complete and stored for distribution.
How do you calculate finished goods inventory?
Calculate finished goods inventory using the formula: Finished Goods Inventory = Beginning Inventory + Cost of Goods Manufactured – Cost of Goods Sold. This will give you a clear picture of your finished goods inventory value.
What are the benefits of managing finished goods inventory?
Managing finished goods inventory will help you to meet customer demand cost-effectively and cash flow efficiently. This will increase profitability and operational efficiency.
What are the challenges of finished goods inventory management?
Finished goods inventory management has challenges such as avoiding excess and obsolete stock and accurate forecasting. Addressing these will ensure efficiency and cost reduction.
How is the finished goods inventory recorded in accounting?
Finished goods inventory is recorded as a current asset on the balance sheet, the total cost of goods manufactured less the cost of goods sold. This will give you an accurate picture of the stock available for sale.
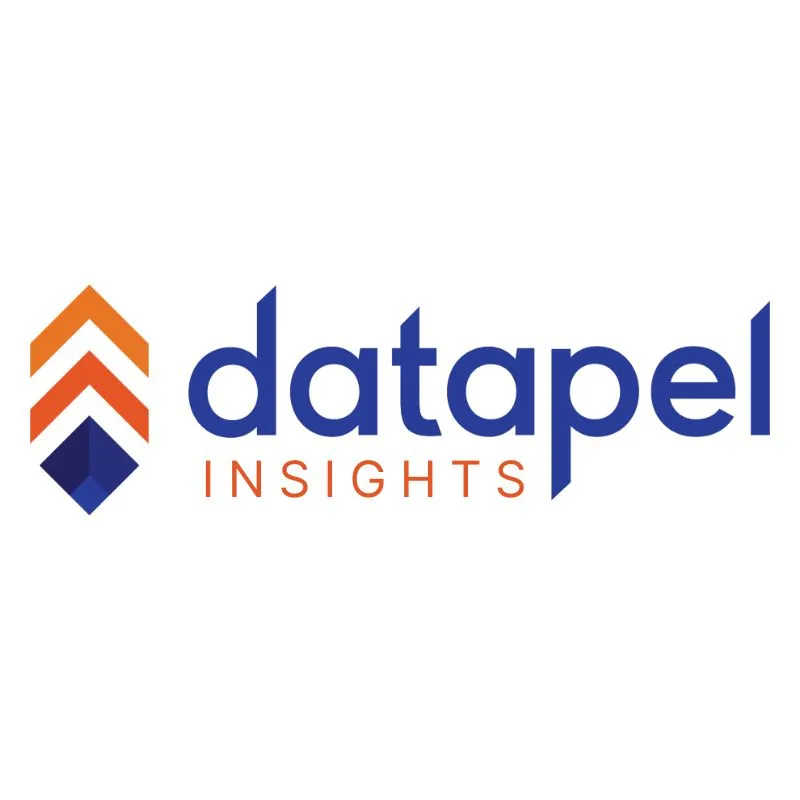
In my role, I oversee the development of insightful blogs that delve into the intricacies of warehouse management. Each piece reflects my dedication to empowering businesses through informative content. Through my team’s extensive experience in the industry, we aim to bring clarity to the complexities of WMS, helping businesses make informed decisions.
Join me on a journey through the ever-evolving landscape of warehouse technology as we explore the latest trends, industry insights, and practical tips to streamline your operations. Feel free to connect, and let’s embark on a collaborative exploration of how WMS can redefine your business efficiency.
Cheers to innovation, efficiency, and the exciting world of warehouse management!