How to calculate PAR levels
Contents
Ever wondered how companies don’t bring in too much or too little stock into their warehouse when they stock many products? You’re in luck.
PAR levels are a key part of inventory management for any business with perishable goods (or any business with limited warehouse space). Here’s what you need to know about them: what they are, why they’re important and how to calculate PAR levels.
Let’s get started!
What are PAR Levels?
PAR stands for ‘Periodic Automatic Replacement’ and is the inventory level a warehouse should hold to meet customer demand. This means stock levels are never too high or too low at any time.
Maintaining par levels is crucial in inventory management to align inventory levels with customer demand, avoid stockouts and overstock, save time and resources, and ensure effective management. PAR levels (also known as inventory PAR levels) come into play when you need to replenish your inventory and decide how much new stock to order. For example if a product’s PAR level is 50 and there are 10 of that product in stock then 40 more will be ordered.
Why are PAR Levels Important?
PAR levels are most important to businesses that deal with perishable goods such as food and beverage, healthcare, cosmetic and pharmaceutical industries. In these industries managing inventory levels is a fine balance: understocking means customer shortages and delays, overstocking means goods spoiling before they ever reach the customer. Overstocking means spoilage and a mountain of food waste.
Efficient inventory management is crucial in these scenarios as it helps in reducing costs and boosting margins. PAR levels are the perfect measure to determine a healthy balance of stock for your warehouse: not too little, not too much. When calculated correctly they will allow your business to absorb a small amount of increased demand without major overstocking decimals.
And when you track replacement levels you can see which stock is depleting the slowest and quickest so you can make more accurate replacement orders.
What are the benefits of using PAR levels in efficient inventory management?
The benefits of PAR level calculations can be obvious and surprising for multi-unit restaurant businesses.
There are many benefits to using PAR levels as part of your inventory management.
- Reduced expired goods costs
- Reduced product waste
- Under and overstocking prevention
- Inventory turnover
- Control over inventory and customer demand
- Customer satisfaction
- Maintaining a healthy inventory turnover rate to reduce waste, avoid stockouts and overstock, meet customer demand reliably, and increase overall efficiency and profits
How to calculate PAR Levels?
PAR levels are calculated based on several factors including historical data (how well the item sold last year), trends, modelling, expiry dates and the ins-and-outs of the supply chain for each product. The PAR level formula involves analysing sales and inventory usage data, taking into account lead time and safety stock to determine the PAR level for each inventory item.
Calculating PAR levels involves digging into these factors to get it right.
Unfortunately, there is no simple formula for the perfect par levels for your business. Each product is different. For example, milk expires much faster than cereal so PAR levels will need to be adjusted for that. Safety stock is also a key factor in this process as it acts as a buffer against unexpected demand or supply chain issues.
2 Things to consider when setting PAR levels
1. Expiration
Products with fast expiration dates require lower PAR rates than non-perishable products with similar demand rates. Products with fast expiration dates (eg. dairy, fish/meat, temperature sensitive medications) are more at risk of spoiling if demand decreases. And safety stock helps to buffer against demand spikes.
When this is the case, power PAR levels reduce the financial penalty to the business. Here are some reasons why PAR levels are important in warehouse management:
- No stockouts: PAR levels ensure inventory doesn’t fall below a critical level and you don’t run out of stock. Stockouts can lead to lost sales, unhappy customers and damage to the business reputation.
- Reduce excess inventory: Setting PAR levels prevents overstocking which ties up capital and leads to increased storage costs, obsolescence and waste.
- Simplify ordering: With PAR levels in place businesses can simplify their ordering process by automating the reordering of inventory when it falls below the PAR level. This reduces the risk of human error in manual ordering and ensures inventory is replenished on time.
- Improve forecasting: By analysing inventory levels and demand trends businesses can use PAR levels to improve forecasting and anticipate future demand for products. This helps businesses plan for future growth, optimise pricing and promotions and overall profitability.
2. Seasonality and Demand Patterns
PAR levels need to be calculated with the seasonality and demand patterns of your product in mind. For products with high seasonality (ie. demand changes dramatically from season to season) you may want to have different PAR levels for different times of the year.
For example most warehouses don’t need 10,000 Christmas trees to occupy their warehouse all year round. And calculating restaurant inventory par levels by considering lead time, usage rate, safety stock and sales report data can help avoid food waste or overstocking.
Example of Calculating PAR Levels for Milk vs Cereal
When calculating PAR levels, we consider historical sales data, trends, expiry dates, supply chain specifics, lead time and safety stock. Here’s how you might do this for milk and cereal:
Milk:
- Historical Data: How much milk did you sell last year during the same period? Let’s say you sold 200 units a week.
- Trends and Modelling: What trends might impact sales? Holidays and seasons can increase demand.
- Expiry Dates: Milk has a short shelf life of 7-10 days. You can’t hold too much stock.
- Lead Time: It takes 2 days for a new shipment of milk to arrive, so you need to factor that in.
- Safety Stock: To buffer against unexpected demand or supply chain delays you might want to hold 20 extra units of milk.
Calculation:
- Average weekly sales: 200 units
- Lead time: 2 days (approximately 1/3 of a week)
- Safety stock: 20 units
PAR Level = (Average weekly sales / 7 days) * Lead time days + Safety stock
PAR Level for Milk = (200 units / 7) * 2 + 20 ≈ 57 units
So, your PAR level for milk would be around 57 units.
Cereal:
- Historical Data: How much cereal did you sell last year during the same period? Let’s say you sold 100 units a week.
- Trends and Modelling: What trends might impact sales? A promotion might increase sales.
- Expiry Dates: Cereal has a much longer shelf life, several months, so you can hold more stock.
- Lead Time: It takes 5 days for a new shipment of cereal to arrive, so you need to factor that in.
- Safety Stock: To buffer against unexpected demand or supply chain delays you might want to hold 10 extra units of cereal.
Calculation:
- Average weekly sales: 100 units
- Lead time: 5 days (5/7 of a week)
- Safety stock: 10 units
PAR Level = (Average weekly sales / 7 days) * Lead time days + Safety stock
PAR Level for Cereal = (100 units / 7) * 5 + 10 ≈ 81 units
So, your PAR level for cereal would be around 81 units.
Now you can set your PAR levels for each product and balance demand with waste.
Get in control of your inventory
Inventory management software is key to setting PAR levels, tracking inventory, and having visibility of all your warehouse operations. Calculating PAR and tracking inventory manually is a time-consuming process and the administrative effort would offset many of the benefits of having PAR levels in the first place. PAR level management will help you avoid stockouts, reduce waste and meet customer demand.
Datapel gives you visibility, so you can manage inventory with less admin. PAR level management will improve inventory accuracy, and reduce purchasing stress and customer dissatisfaction. Try Datapel free today.
FAQ’s
What does par level mean?
PAR level stands for ‘Periodic Automatic Replacement.’ It is the inventory level a warehouse should hold to meet customer demand, ensuring that stock levels are neither too high nor too low at any time.
What is an example of par levels?
An example of par levels is if a product’s PAR level is set at 50 units. If the current stock of that product is 10 units, then an order will be placed to bring the stock back up to 50 units, meaning 40 more units will be ordered.
What are the benefits of PAR level?
The benefits of PAR level in inventory management include:
- Reduced expired goods costs
- Reduced product waste
- Prevention of understocking and overstocking
- Improved inventory turnover
- Better control over inventory and customer demand
- Increased customer satisfaction
- Maintaining a healthy inventory turnover rate
- Meeting customer demand reliably
- Increased overall efficiency and profits
What does par level stand for?
PAR level stands for ‘Periodic Automatic Replacement.’
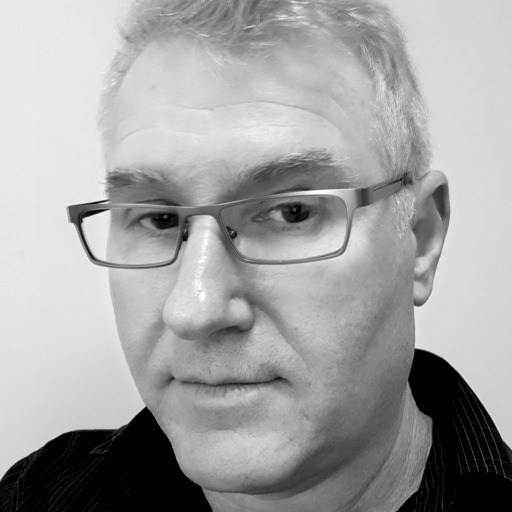
Adam Wesley is the Founder and Managing Director of Datapel Systems, where he serves as an agile Operational Leader with a fervent dedication to problem-solving, strategic thinking, and process improvement. With a remarkable career spanning over two decades in the IT landscape, Wesley brings a wealth of knowledge and expertise.
For the past 15 years, he has honed his skills in the niche field of warehouse workflow solutions. Wesley firmly believes that effective business systems should not only meet the needs of warehouse operations but should also empower and support warehouse workers. His vision revolves around achieving the precise shipment of orders while simultaneously minimising order fulfilment time.
Adam Wesley’s commitment to innovation and efficiency in the ever-evolving IT industry has positioned him as a respected figure, and his leadership at Datapel Systems continues to drive the company towards excellence in warehouse management solutions.