How to Optimize the Pick and Pack Process in 2024
Contents
With customers wanting faster fulfilment, traceability, and accurate delivery of their orders, many fulfilment centres are leaning on the pick and pack process to meet these demands. Under the right conditions, pick and pack warehouses can be a very efficient and cost-effective way to fulfil orders. However, they can become bogged down if not properly managed.
Optimising the process can help reduce costs while improving customer satisfaction by ensuring orders arrive on time and accurately. It is essential to understand how different elements of the process interact with each other to optimise it successfully.
Define your picking and packing process goals.
KPIs like throughput, order accuracy and labour efficiency are essential metrics to consider when articulating the objectives of these processes. Doing so will help ensure a clear understanding of what success looks like and maximize the performance of both the picking and packing processes.
What is pick and pack fulfilment?
The pick and pack process is relatively simple. First, orders are received and then put into batches for workers to select. Once picked, the items are sent to a packing station, packed into boxes or envelopes, and prepared for shipment.
Other factors complicate the process, such as the nature of the business, the number of SKUs, and the order types. Depending on the facility, this process can involve one person doing both tasks or multiple people at separate stations.
The four most common ways to pick in this environment are batch, wave, piece, and zone picking.
Wave Picking – This method involves filling a batch of orders at once and is best suited for orders located in the same warehouse area. For example, a single-order picker could collect multiple orders with similar items nearby.
Batch Picking – Batch picking allows multiple customer orders to be retrieved simultaneously, allowing pickers to reduce warehouse travel time and boost operational efficiency. For instance, a warehouse may group multiple orders for customers in the same area in one batch for faster deliveries. Batch picking also reduces the inventory management load as it does not require frequent inventory checks for each order.
Piece Picking – Piece picking is the process of filling individual orders one item at a time. Since this method requires a picker to go through every item on an order list, it’s best suited for small orders.
Zone Picking – Zone picking divides the warehouse into zones, each with its picker assigned to it. Once they pick items in their zone, the order moves to the next zone for additional items. This method is more efficient than piece picking as it allows more orders to be filled at once but still requires some travel between zones for the pickers.
Once you’ve determined the picking and packing goals and methodologies that work best for your fulfilment needs, the next step is to develop efficient procedures for these tasks. Optimizing the pick and pack process requires an understanding of how different elements of the workflow interact with each other.
Four ways to optimise your pick and pack process
By analysing your workflow, you can identify areas where improvements can be made, such as reducing travel time between picking locations or increasing accuracy with barcode scanning systems. Organising inventory into zones based on the frequency of use can reduce the time spent searching for items during order fulfilment. Separating slower-moving items from faster-moving ones helps prevent congestion in warehouses.
Minimise Travel Time
Increasing efficiency by minimising the time spent travelling between pick locations can help optimise the picking process. You don’t want your employees zig-zagging around during the picking process when they should be following the most efficient path. For this reason, you should carefully consider where you place high-volume items and place them strategically.
Develop a Standard and Repeatable Process
Keep in mind you aren’t just trying to eliminate wasted movement; you are also trying to negate the opportunity for human error. By developing a standard and repeatable process, you can reduce the chances of an order being filled incorrectly.
Mobility
Using mobile carts or devices can speed up the process by allowing pickers to move quickly between aisles. Additionally, these mobile devices can scan items, reducing the chance of an item being picked incorrectly and eliminating the need for manual data entry.
Integrate Technology
Implementing barcode scanners, warehouse management systems (WMS), or printers into the process will help to ensure accuracy and efficiency. This type of technology can quickly scan orders, update inventory levels, print labels or documents, provide tracking to the consumer, and track the progress of an order.
Choose the right technology to optimise your pick and pack process
Finding the right balance of technology will enhance efficiency, reduce human errors, and provide a strong ROI. Automation and robotics are all the rage in material handling but may be optional for your business. Choosing the right technology for your needs can be daunting, but it doesn’t have to be!
Technology intends to streamline your business and make life easier, so a good WMS (warehouse management system) and barcode scanning are essential to optimise this process.
Warehouse Management System
A WMS is no longer a luxury in warehousing. A good WMS will provide automation, real-time visibility into processes and inventory levels, and guided picking and putaway, allowing for faster picking/packing cycles. Order fulfilment is at the forefront of the customer experience, making a WMS essential.
Barcode Scanners
Barcode scanners are ideal for accurate order fulfilment as they ensure the correct items are picked and packed out. Implementing a barcoding system will improve speed and accuracy, ultimately improving the customer experience.
Several solutions bring the goods to the selector, such as automated storage and retrieval systems (AS/RS) or automated put walls. While these speed up the process and improve accuracy, these solutions can be expensive.
If you want to improve accuracy, pick-to-light, voice-to-pick, or wearable technology are all affordable and easy to implement.
Try to look ahead and foresee any potential future issues that might crop up from utilising less robust technologies. Also, think about your industry and the most critical KPIs.
Evaluate, improve, and repeat
When evaluating and adjusting a business’s processes, being willing to change is the best thing to do. After all, an effective process isn’t just an initial undertaking but a continuous journey.
It’s an essential part of running the business – a proper evaluation and thoughtful adjustments will make all the difference between stagnation and success. With that positive message of assurance in mind, may we never forget that evolution and transformation are not only valuable concepts – they’re essential!
Key Takeaways!
- Define your picking and packing process goals
- Choose the right picking process for your business
- Implement ways to optimise the process
- Choose the right technology for your needs
- Evaluate and adjust the process to ensure it works optimally for your business
Unlock the potential of your pick and pack process with Datapel’s cloud-based Warehouse Management Solution. Streamline order management, improve accuracy and product tracking, and boost your team’s efficiency simultaneously with our pay-as-you-go monthly pricing plan and free trial – see what Datapel can do for you today!
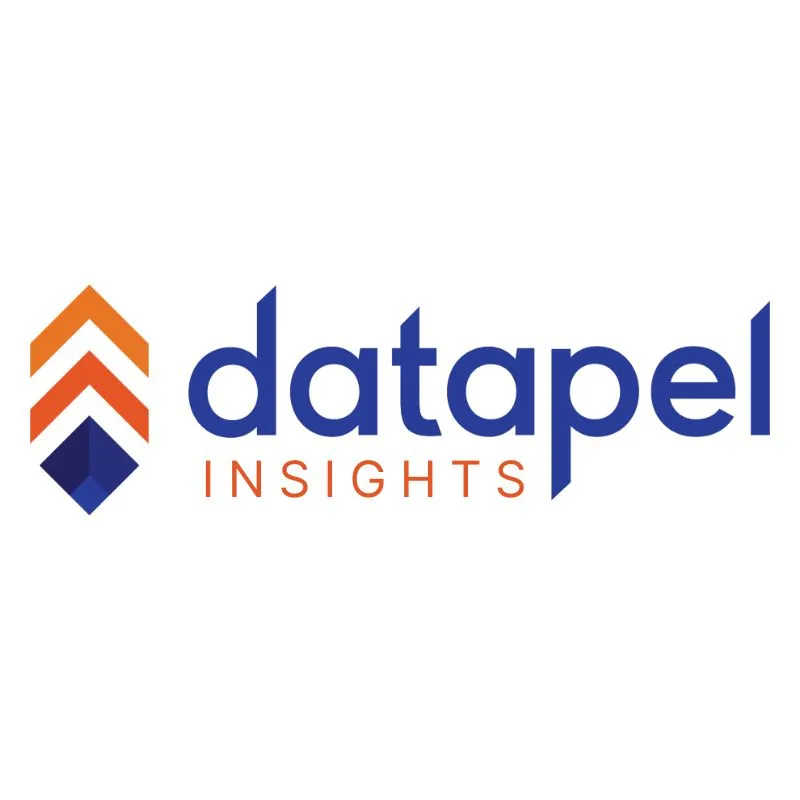
In my role, I oversee the development of insightful blogs that delve into the intricacies of warehouse management. Each piece reflects my dedication to empowering businesses through informative content. Through my team’s extensive experience in the industry, we aim to bring clarity to the complexities of WMS, helping businesses make informed decisions.
Join me on a journey through the ever-evolving landscape of warehouse technology as we explore the latest trends, industry insights, and practical tips to streamline your operations. Feel free to connect, and let’s embark on a collaborative exploration of how WMS can redefine your business efficiency.
Cheers to innovation, efficiency, and the exciting world of warehouse management!