Signs You Need a Warehouse Management System
Contents
The supply chain disruptions of the early 2020s are driving investments in more effective supply chain management systems.
Analysts point to growing eCommerce and the need for greater transparency as primary reasons for the transition from paper, spreadsheets, and legacy on-premise systems to cloud-based warehouse management systems (WMS) and other supply chain management tools.
Evaluating the Pace of Your Warehouse
KBV Research predicts that supply chain management market growth in the Asia Pacific (APAC) region to grow at a 12.1% CAGR from 2021 to 2027 to reach a market value of $7,809.6 million.
Growth of the APAC market is outpacing growth in North America, predicted at an 8.8% CAGR, and in Europe, forecast at a 9.6% CAGR, during the same timeframe. However, it shows that operations worldwide prioritise supply chain management as part of their business continuity and growth strategies.
The question you need to answer is whether or not your warehouse is keeping up.
5 Signs You Need a Warehouse Management System
Consider these five signs that your operation may be falling behind your competitors and putting profitability and customer relationships at risk.
1. Inefficient Picking Processes
To maximise key performance indicators (KPIs) like picking cycle time, picking and packing cost, and picking efficiency, your employees must have clear directions, work accurately, and transition smoothly and quickly from order to order. This is possible with a warehouse management system.
Paper-based processes add time to picking, open the door to errors from misreading or recording data incorrectly, and are a barrier to gaining real-time process insights. Traditional workflows also depend on employees’ knowledge of the warehouses and processes, resulting in little consistency in pick rates across your team.
Furthermore, workers who experience pressure from using a disorganised system while still trying to stay on schedule can suffer burnout and may cause a turnover, something operations can’t afford at a time of customer demand and widespread labour shortages.
A warehouse management system allows you to digitise processes and enable guided picking processes that standardise worker performance and enhance picking efficiency and accuracy.
2. Lack of Inventory Visibility
How many items do you have in stock right now?
Access to accurate inventory data in real-time is crucial. It allows you to ensure that you can provide up-to-date information to customers, fulfil orders, and make informed purchasing decisions.
If you notice that you are running out of stock or overstocking certain items, backorders are increasing, or if some pickers claim your entire inventory is out-of-stock while others find items without issue, you need a better system for inventory tracking.
Additionally, if you store, pick, pack and ship perishables, you need visibility into “best before” dates. This allows you to provide customers with safe, quality products and minimise waste and loss.
A warehouse or inventory management system will help you keep track of inventory locations and keep inventory management metrics moving in the right direction. You can monitor stock by item number, name, batch or serial number, bin, custom field, or barcode.
A warehouse management system also keeps your team informed of items that are committed, allocated and on hold at multiple warehouses, in addition to the projected days until out-of-stock items are due at receiving for better planning.
3. Increased Customer Claims
If your Net Promoter Score is falling as more people report they’d not recommend you to a colleague, it’s time to make a change. Mistakes, including shipping to the wrong address, incorrectly picking orders, or falling short of your delivery in full on time goals, create poor customer experiences and, in some instances, lost business.
In this dynamic, competitive marketplace, you must meet customers’ expectations and keep revenue coming in.
By automating your order management processes with a warehouse order management system, you can ensure the accuracy of orders to minimise these claims. Plus, with a solid system backing returns management, you’ll ensure you’re only accepting returns on valid customer orders.
4. Recurring Issues that Need Root Cause Analysis
Occasional errors can happen at any time during the whole order fulfilment process. However, warehouse operations must address recurring issues to control costs and protect their brand reputation. With manual warehouse management procedures, it can be extremely time-consuming to get to the bottom of problems and determine the best way to correct them.
A warehouse management system provides visibility into your processes, enabling you to track, step-by-step, where things went wrong and indicating changes you need to make. Your warehouse software also documents activities, providing you with records you can use to settle customer disputes.
5. Limited Scalability
If you experience any of the four abovementioned issues, your operation isn’t positioned for growth. Warehouses need to carefully consider the impact that an increase in eCommerce orders and greater dependence on a global supply chain have on business operations and their warehouse operations.
Your warehouse won’t be able to handle higher volumes of orders if you can’t establish efficient picking processes, track inventory, manage inventory, have visibility into accurate inventory management and shipping data, and meet customers’ expectations.
A warehouse tracking system WMS solutions will enable you to establish effective processes, guide employees through them, and analyse operational data for continual improvement. Data from your warehouse management system wms) will also help you manage finances, minimise waste and loss, and improve your bottom line.
Benefits of a modern, cloud-based warehouse management system
Digital technology has transformed the way consumers buy—changing supply chains and markets and changing customers’ buying behavior and complicating the supply chain. Moving to Cloud warehouses will offer an integrated fulfillment solution that offers visibility in realtime, scalable flexibility, and market response.
Scalability and flexibility of supply chain operations
Modern global markets demand rapidity. Oracle’s Cloud Solution allows for rapid expansion to meet market changes. Scale as necessary for handling peak season and managing other changes.
When a new opportunity comes around you are ready. You can enjoy the agility of your company without a fixed cost. Capital expense is wiped out from all internal hardware and labor costs. It also allows for investment in IT—not just your IT.
Fulfillment process—Rapid implementation
To stay competitive with new fulfillment economies you must adjust fast. Cloud-based systems allow you to quickly grow the supply chain. The most advanced logistics capabilities are delivered week rather than month. It integrates seamlessly with multiple systems, supporting multiple locations and channels of fulfillment.
It has the same storage functionality as on site systems, but with reduced IT costs for a single cloud based system. Cloud Technology reduces the need to hire hardware and technical experts for maintaining the systems. It’s quick to get started and cheaper.
Order Picking, Packing, and Fulfilment
WMS systems help decrease these costs by real time visibility providing efficient transportation management systems and storage methods. It also supports technologies to speed up pick up including the RF (RF) RF scan verification, Pick-tolight and Pick-to-Voice technology, and robot and software algorithms to optimise pick paths.
Seamless Integration—Warehouse management and ERP
Cloud storage services are built for integration. Integrate with host ERP and Merchandising management software, and SCM systems, it supports integration with a host ERP system.
It was built to integrate and to be integrated rather than isolated. Data transmission is made using the industry standard RESTful web services or XML. This integration point can easily be used by the manufacturers for automated warehouse integrations.
Labour Management
Gaining knowledge of labour and production costs can make warehouse management efficient. A WMS provides realtime data on warehouse operations, workers costs, response times, productivity problems, trends in planning and other areas – so that companies can adjust accordingly. The system also supports task interleavability based on priorities or proximity, thus reducing warehouse workers’ travel time in addition to preventing the “deadheading” and time waste. They can help plan a project or schedule directly or via integration.
Warehouse Metrics and Analytics
It’s possible to capture real time information through a cloud WMS automatically rather than using manual methods, which reduces keying errors and dramatically speeds up the process. The data can be used as a basis for several analytics to measure important indicators, such as on-time delivery of goods, stock availability, distribution costs and the quantity of goods in a single place. The software then creates visually displayed reports that can be shared with stakeholders or used for adjustments.
Customer and Supplier Relationships
A Warehouse Management System (WMS) provides real-time visibility into inventory levels, enabling businesses to share accurate stock levels and delivery timelines with suppliers. This transparency fosters trust, facilitates better coordination, and helps avoid stockouts and overstock situations.
Through a Cloud WMS, you can automate order processing and reduce errors. This ensures that your orders are accurate and delivered on time, which strengthens your supplier relationships as they can rely on your orders being correct and timely.
How Do You Use a Warehouse Management System?
Warehouse management systems are used in managing key warehouse functions such as warehouse organisation: By inputting warehouse size and stock information such as pallet size or product sizes the WMS software may create warehouse diagrams to assist with optimising inventory storage and improving product performance.
Warehouse management systems can plan a work week by calculating the required time and estimating the costs of the job. Warehouse management systems are also capable of contacting transport suppliers to arrange shipment, delivery time and locations. It ensures truck drivers arrive at the right dock in the right place.
Is Your Operation Ready for a Warehouse Management System?
If you see any of these red flags in your operation – or are experiencing other challenges created by manual, paper-based processes – it’s time to upgrade to a warehouse management system.
However, the first step isn’t purchasing technology. An upgrade that will provide real value to your organisation begins with evaluating your operation and identifying processes that need improvement. The adage “garbage in, garbage out” applies universally.
Only after you implement best practices can you expect technology to support them and deliver the gains in productivity and efficiency you need.
Take stock (pun intended) of your operations’ strengths and weaknesses, your market and supply chain position, and plan a strategy that leverages a warehouse management system to keep your operation competitive.
FAQ’s
Why are businesses moving towards cloud-based Warehouse Management Systems (WMS)?
The shift towards cloud-based WMS solution is driven by the need for greater efficiency and transparency in your supply chain operations, exacerbated by supply chain disruptions in the early 2020s. These systems offer real-time insights, scalability, and integration capabilities that paper-based, spreadsheets, and legacy systems cannot provide.
How is the WMS market growing in the Asia Pacific region?
The WMS market in the Asia Pacific (APAC) region is predicted to grow at a Compound Annual Growth Rate (CAGR) of 12.1% from 2021 to 2027, reaching a market value of $7,809.6 million. This growth rate surpasses that of North America and Europe, indicating a strong focus on supply chain management in the APAC region.
What are the signs that my warehouse needs Warehouse Management Software?
Five key signs indicate the need for a WMS: inefficient picking processes, lack of inventory visibility, increased customer claims, recurring issues requiring root cause analysis, and limited scalability. These signs suggest that manual and outdated systems are hindering your warehouse’s efficiency and growth potential.
How can Warehouse Management Software improve the picking processes?
A WMS digitises picking processes, enabling guided picking that standardises performance and enhances efficiency and accuracy. It eliminates the time and errors associated with paper-based processes and ensures consistent pick rates across the team.
What benefits does modern, cloud-based Warehouse Management Software offer?
Modern, cloud-based WMS offer scalability, rapid implementation, and seamless integration with ERP and other systems. They support advanced picking technologies, provide real-time visibility into inventory and labour management, and enable comprehensive analytics for improved decision-making and streamlined warehouse operations.
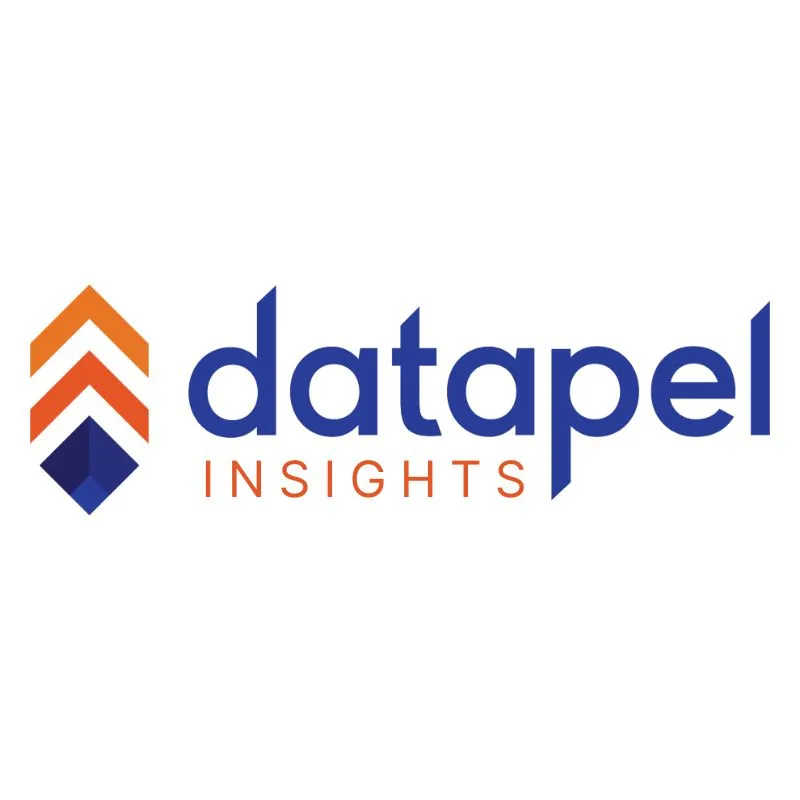
In my role, I oversee the development of insightful blogs that delve into the intricacies of warehouse management. Each piece reflects my dedication to empowering businesses through informative content. Through my team’s extensive experience in the industry, we aim to bring clarity to the complexities of WMS, helping businesses make informed decisions.
Join me on a journey through the ever-evolving landscape of warehouse technology as we explore the latest trends, industry insights, and practical tips to streamline your operations. Feel free to connect, and let’s embark on a collaborative exploration of how WMS can redefine your business efficiency.
Cheers to innovation, efficiency, and the exciting world of warehouse management!