The Ultimate Guide to Mastering Bill of Materials (BOM) Management
Contents
Welcome to our comprehensive guide on understanding and utilising a Bill of Materials (BOM). As a leading authority in the field, we are dedicated to providing you with the most insightful and detailed information available.
Whether you’re a novice or an experienced professional, this guide will equip you with the knowledge and strategies needed to optimise your BOM management and streamline your production processes.
What is a Bill of Materials (BOM)
A Bill of Materials, or BOM, is a document that lists all the components, parts and raw materials needed to make a product. As suppliers change over time access can be given to other parties involved in the production process.
An Engineering BOM (EBOM) is created during the product design phase and outlines the original design of a finished product, including detailed specifications, parts and components needed to make the product. It’s a roadmap for manufacturers to understand the composition and structure of a product and the quantities and specifications of each item.
Why an Accurate BOM is Important
An accurate and up-to-date BOM is important for:
- Product Development: A well-structured BOM helps the design and development process, ensuring all components are accounted for and integrated into the product.
- Cost Management: By breaking down all the materials the BOM allows for accurate cost estimation so manufacturers can plan their budgets.
- Inventory Control: An accurate BOM allows manufacturers to optimise their inventory levels, have enough stock of required components and minimal excess inventory.
- Production Efficiency: With a detailed BOM manufacturers can streamline their production process, reduce errors and improve overall efficiency which means cost savings and customer satisfaction.
Good Bill of Material Management involves using various tools and strategies to keep the BOM accurate. These tools are both hardware and software.
Components of a Bill of Materials
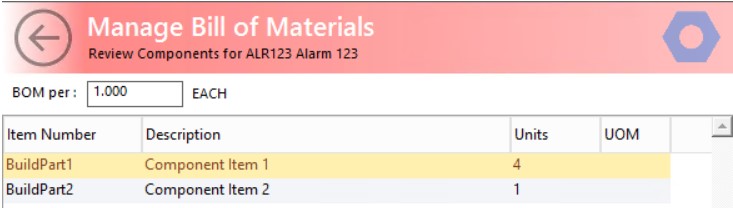
A well-structured BOM has the following components:
1. Item Number
Each component in the BOM has a unique item number or ID. This is for easy reference and identification throughout the production and assembly process.
2. Description
The description field is a summary of the component, so anyone reviewing the BOM can quickly understand what it’s for and what it does.
3. Quantity
The quantity column is the number of each component required for one unit of the final product. Accurate quantity calculations are key to avoid shortages or waste during production.
4. Unit of Measure
This field is the unit of measure for each component, piece, kilogram, meter or litre. Consistency in the unit of measure is key for inventory management and procurement.
5. Reference Designators
Reference designators use alphanumeric codes to identify where each component should be placed on the final product. They help the assembly process to ensure components are in the right place.
6. Manufacturer and Part Number
These fields provide information on the manufacturer and part number of the component. This is for sourcing and procurement of the right components for production.
7. Extra Information
Depending on the complexity of the product extra information fields can be added to the BOM, component specifications, revision numbers or alternative suppliers.
Best Practices for BOM Management
To improve your BOM management and overall efficiency consider the following best practices:
Advanced BOM management solutions help to improve accuracy and efficiency by moving away from manual processes to digital.
Good product lifecycle management (PLM) is key to BOM management as it helps product engineers and procurement specialists add value to products throughout their lifecycle.
1. Version Control
Update and maintain your BOM version regularly so everyone involved has access to the latest revision. This avoids errors, confusion and inconsistencies during production.
2. Standardise Naming
Have a clear and consistent naming convention for all components in the BOM. This makes communication easier, minimises errors and collaborates with suppliers and manufacturers.
3. Document Changes and Revisions
Keep a record of all changes and revisions to the BOM. This is useful for traceability and future reference especially when product iterations or improvements are needed.
4. Suppliers
Keep in touch with your suppliers to get accurate and up-to-date component information. Good supplier management is key to managing multiple suppliers and getting materials on time and quality. Building strong relationships with reliable suppliers will simplify your procurement process and reduce lead times.
5. BOM Management Software
Consider using BOM management software to centralise your data, automate processes and collaborate with your teams. These tools can improve efficiency and accuracy in managing BOMs by integrating materials management which is key to getting purchasing and manufacturing functions to talk to each other to create accurate BOMs.
Bill of Materials in Warehouse Management Software
Using warehouse management software with BOM functionality is the most efficient and accurate way to create BOMs. A Manufacturing BOM (MBOM) is the list of parts and assemblies required to build a shippable product, handle waste and manage material consumption during production. Having BOMs in inventory software gives you several advantages:
- Simplified Production Planning: Warehouse management software with BOM simplifies production planning by calculating the required quantity of each SKU based on the number of assemblies to be produced, taking into account the existing stock of parts or components. This automation reduces complexity and improves the planning of production runs. The manufacturing process is responsible for overseeing and coordinating many aspects of production, ensuring authorized personnel manage changes and document each component’s details.
- Version Control: Having one single source of truth for your BOMs is key. Cloud-based inventory management systems provide seamless document management so all stakeholders have access to the latest and most accurate BOM versions. This reduces confusion caused by outdated or conflicting BOMs.
- Demand-Driven Purchasing: A robust inventory system allows you to start production planning and purchasing from a sales order. This enables Just-in-Time manufacturing where production and procurement are driven by actual demand. By aligning your manufacturing to customer orders you can optimise inventory levels, reduce carrying costs and increase customer satisfaction.
How to create a Bill of Materials in a WMS
Creating a Bill of Materials (BOM) in WMS means listing the items required to build a new inventory item. Manufacturing BOMs are key to accurate assembly, and inventory management and to avoid delays by providing detailed information of the materials and components required to build a product. A BOM is the components required to build the item, like Coffee, Water, Milk and Sugar for a Café Latte. A BOM usually specifies the quantity for one built item.
- Open WMS.
- Go to the Items list register.
- Select the Assembly item for which you want to create the BOM.
- Open the Inventory detail card, go to Settings and tick the checkbox.
- This will show the Component Tab between the Details Tab and the Pricing Tab.
- Click on the “Components Tab”.
- To create a new BOM, click “Edit Bill of Materials (BOM)…”.
- A new screen to enter the Bill of Materials will appear.
- Enter the quantity for one built item.
- Enter the components manually or use the Stock Lookup with Ctrl+Enter to select multiple items.
- Enter the component quantity for one built item.
- Save BOM.
The Bill of Materials is the component items required to build the final product. A Work Order is an instruction to create new stock. A Work Order goes through the manufacturing workflow, components are assigned to it (removed from stock), and finally, the stock is added to the warehouse inventory.
Conclusion
Creating a Bill of Materials (BOM) is key for any manufacturing company to be efficient and cost-effective. By understanding the importance of a BOM, and knowing what are the components and best practices you can streamline your production, reduce costs and increase productivity.
Don’t forget, that a good BOM is the foundation of product development and manufacturing. Use BOM to take your company to the next level.
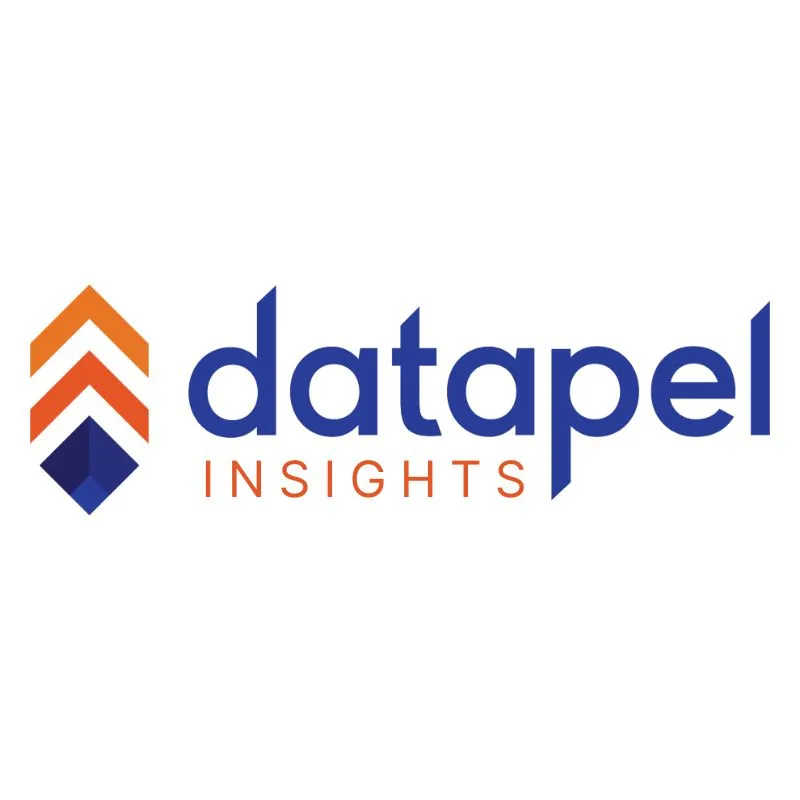
In my role, I oversee the development of insightful blogs that delve into the intricacies of warehouse management. Each piece reflects my dedication to empowering businesses through informative content. Through my team’s extensive experience in the industry, we aim to bring clarity to the complexities of WMS, helping businesses make informed decisions.
Join me on a journey through the ever-evolving landscape of warehouse technology as we explore the latest trends, industry insights, and practical tips to streamline your operations. Feel free to connect, and let’s embark on a collaborative exploration of how WMS can redefine your business efficiency.
Cheers to innovation, efficiency, and the exciting world of warehouse management!