8 Ways to Reduce Warehouse Costs and Increase Profits
Contents
Every business wants to operate as efficiently as possible, and reducing expenses can help achieve this goal. For warehouses, in particular, reducing costs is easier than you may think. Reducing expenses offsets the rising cost of labour and rent that are outside your span of influence.
Here are 8 of the most effective ones we’ve seen in our years of experience. Take a look, and see which ones you can implement immediately!
1. Inventory Visibility
Inventory visibility is one of the most essential factors in being able to support your customers.
As a warehouse manager or supply chain leader, you should be able to see what you have on hand and trust that your records are accurate. The entire supply chain is tasked with having the right amount of goods, in the right place, at the right time. This task is no easy feat.
Excess inventory
Excess inventory may sound like a good problem, but in the grand scheme of things, excess inventory costs the company money. Inventory sitting on the shelf has to be counted, moved to accommodate other products, and isn’t making any money for your organisation.
Implementing technologies such as RFID, barcode scanners, and warehouse management systems (WMS) can significantly improve your inventory visibility. This will help you track inventory levels and identify any excess stock quickly.
2. Storage Optimisation
A well-organised warehouse drives the efficient flow of goods, improves safety, and helps reduce warehouse costs.
Just like inventory, you want to maximise your warehouse space, so there is as little waste as possible. Solving space optimisation requires using shelves, racks, and other storage solutions to maximise space and make it easy to find products.
Rent for warehouse space continues to increase each quarter, reaching almost $10 per square foot and nearly $15 per square foot in markets like Los Angeles and New York.
Warehouse storage optimisation factors include:
- Warehouse flow
- Product placement
- Storage space
- Retrieval methods
An optimised warehouse will improve inventory flow, prevent stock loss, and significantly increase productivity. All these elements work together to improve overall efficiency and ensure you aren’t overpaying for space you don’t need.
This is a win-win situation for any organisation as it increases profits and improves customer satisfaction.
3. Reduce warehouse costs with Cross Docking
Cross-docking eliminates the need to store or put away products. Instead, cross-docking enables the moving of finished goods immediately supplied or manufactured to a customer or retailer with little or no handling or storage in the warehouse.
Cross-docking is ideal for businesses looking to reduce their warehouse costs, improve their order fulfilment process, and accelerate the time it takes for products to reach customers.
While cross-docking isn’t always feasible, it is often an excellent option for organisations that experience seasonal-based high demand or looking to practice just-in-time delivery to streamline their supply chain.
4. Optimise Your Picking Process
When picking orders, you want the order-picking process to be fast, safe, and accurate.
Does your team zig-zag or backtrack when picking orders? If so, your picking process is probably inefficient, so you’re wasting time and money. When your picking flow isn’t efficient, it could also lead to missed picks or missed line items and other errors that can negatively impact your customers.
Optimising the picking process is a review process that involves continually breaking down your order fulfilment process and making minor changes to improve it.
Ways to optimise your picking process
- Implementing technologies designed to improve accuracies, such as guided pick instructions, pick-to-light, and mobile or wearable devices.
- Improving communication between team members to reduce confusion or duplicate efforts
- Performing a daily Gemba walk to identify problem areas or inefficiencies
- Utilising lean production principles to streamline processes and eliminate waste
The cost of warehouse labour has risen 37% since January 2020, making it one of the most expensive costs in the warehouse.
By optimising your picking process, you can maximise your return on labour, improve order fulfilment times, and deliver better customer service. Ultimately, this will help maximise productivity for your business and increase success.
5. Warehouse Management System
A Warehouse Management System (WMS) is a game-changer in reducing costs and increasing efficiencies in your warehouse. This is especially true for warehouses operating on antiquated systems such as Excel or paper to handle warehouse processes.
A WMS can help you plan, schedule, and route orders more accurately, monitor inventory levels, manage labour resources, and, most importantly, reduce paperwork and manual processes.
Many WMS platforms integrate automation technologies with small-medium business accounting or enterprise resource planning (ERP) systems. This enables businesses to connect multiple systems and streamline their supply chain.
Cycle Counting
Cycle counting, if it happens at all without a WMS in place, often involves walking through and counting inventory from start to finish by hand. With a WMS in place, warehouses can automate the cycle counting process, saving both time and money.
Guided picking, packing, and putaway are a few other ways a WMS can reduce warehouse costs.
From an onboarding perspective, guided picking options can decrease the time it takes to train employees. Simplifying the picking process and reducing the possibility of human error means you can eliminate quality issues and reduce rework or returns, saving even more time and money.
6. Using the proper material handling equipment
Forklifts and pallet jacks are two of the most common material-handling equipment(MHE) found in warehouses. They can make the workload of manual labourers much more manageable, allowing them to pick and place orders more quickly and easily.
There are many different types of MHE available on the market today, so it’s essential to carefully consider your needs when selecting the right equipment for your warehouse. Factors to consider include:
- The size and weight of materials you typically move within your warehouse
- The frequency of the movement and whether it is a short or long distance
- The number of pallets you typically move at once
If space is a concern, a narrow aisle forklift allows warehouses to bring pallet racking closer together. Warehouses with standard forklifts need aisles around 14′, while a narrow aisle forklift can shrink that distance to under 10′. Compounding this amongst several aisles, you can save thousands of square feet in a warehouse.
If you are moving heavy loads, a standard pallet jack can help but can still cause strain and injuries to manual labourers. A battery-powered lift or tugger may be a better solution for the long term to reduce injuries and move products faster.
Fully automated or semi-automated MHE can significantly reduce walking and searching time and improve accuracy and efficiency. By incorporating data analytics or a digital twin into your process, you can understand where bottlenecks are occurring and make improvements accordingly.
7. Benchmarking
Benchmarking involves comparing your warehouse’s performance against industry standards and best practices. By doing so, you can identify areas for improvement, set goals for achieving those improvements, and track your progress over time.
Several key metrics are commonly used to benchmark a warehouse’s performance, including:
- Order fulfilment accuracy – the percentage of orders shipped with the correct items
- Throughput – the amount of material moving through the warehouse
- Pick rates – how many units can be picked per hour
- Inventory accuracy – the difference between systematic inventory and what is physically on hand
For smaller and medium-sized warehouses, industry standards may not apply but measuring these metrics helps establish a baseline. Knowing where you stand can allow you to set achievable goals and yield meaningful results.
8. Theft Prevention
Suitable security measures keep honest people honest. This includes installing security cameras and alarms, implementing RFID tags and locks, having clear labelling policies in place, properly vetting all employees, and carrying adequate insurance. Badge access systems can also help prevent theft by limiting access to specific areas.
One way to minimise the theft risk is to separate high-value items from low-value items and closely monitor them with security cameras or sensors.
However, only some theft can be prevented with these measures. The best approach is to reduce the motivation for people to steal by offering competitive salaries and benefits.
Bottom Line
While some of these solutions may require an investment on your part, the long-term savings and increased efficiency will be worth it. Reducing your warehouse costs can be challenging, but it’s important to remember that every little bit counts. Building a culture of continuous improvement is key to long-term success.
Customer expectations and labour costs are higher than ever. The good news is that technology is more accessible than ever and can help you reduce warehouse costs by automating processes, improving accuracy, and streamlining workflow. If you are ready to reduce warehouse costs, follow these tips and get started today!
If you’re looking for more ways to reduce warehouse costs, contact Datapel today. We can help you find ways to save money and reduce costs with an inventory management system.
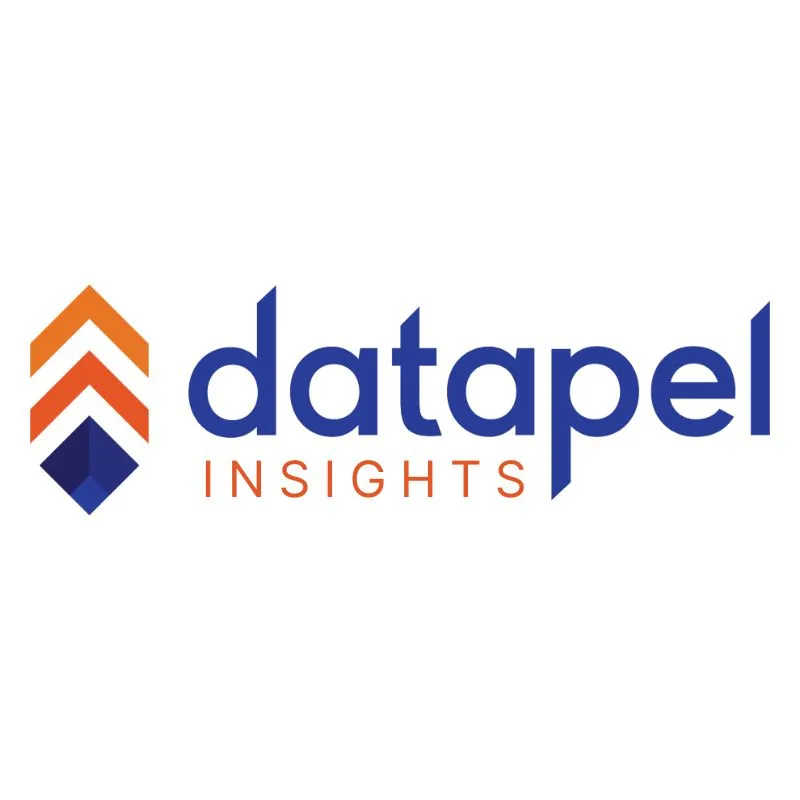
In my role, I oversee the development of insightful blogs that delve into the intricacies of warehouse management. Each piece reflects my dedication to empowering businesses through informative content. Through my team’s extensive experience in the industry, we aim to bring clarity to the complexities of WMS, helping businesses make informed decisions.
Join me on a journey through the ever-evolving landscape of warehouse technology as we explore the latest trends, industry insights, and practical tips to streamline your operations. Feel free to connect, and let’s embark on a collaborative exploration of how WMS can redefine your business efficiency.
Cheers to innovation, efficiency, and the exciting world of warehouse management!