Simplify Complex Manufacturing Supply Chains with a WMS
Contents
Manufacturing supply chains are like intricate machines, with raw materials and components moving through various stages to become finished products ready to ship. But let’s be real, this gets messy. Inventory management, multiple locations, meeting deadlines—it’s not a walk in the park.
This is where an advanced Warehouse Management System (WMS) comes in to save the day. A WMS simplifies workflows and reduces material waste and ensures on-time delivery.
Let’s look at the common challenges manufacturers face and how a WMS delivers.
Manufacturing Supply Chain Challenges
Running a manufacturing supply chain isn’t simple. It comes with its own set of challenges that slow things down and cost you money. Here are some of the biggest:
1. Complex Inventory Management
You’re not just managing finished products. You’re managing raw materials, components and in-progress items—each with its own tracking requirements. Some materials require batch or serial number tracking for traceability and compliance, adding another layer of complexity.
2. Assembling Kits and Bundles
Many manufacturers assemble products from smaller components.
For example, a home appliance manufacturer might bundle motors, screws and casings into a finished washing machine. Tracking all those parts as they come together is no easy task.
3. Central Warehouse with Decentralised Needs
Many manufacturers use a central warehouse to store products but need to ship to customers with specific order requirements. Picking individual orders from central stock is a logistical nightmare.
4. Inventory Across Multiple Sites
Materials and products are often spread across multiple sites. Raw materials might be stored at one location, assembled at another and shipped from a third. Without the right system, things get confusing fast.
5. Reducing Material Waste
Material waste eats into profits and hurts sustainability efforts. From unused raw materials to expired stock, waste is a problem manufacturers need to control.
6. Meeting Deadlines
Late deliveries can damage your reputation and lose your customers. On-time delivery requires precise coordination.
How a WMS Fixes These Problems
An advanced WMS is designed to handle manufacturing complexity.
Here’s how it helps:
1. Track Inventory like a Pro
Modern WMS solutions let you track by batch and serial numbers so you have complete visibility across every stage of production. For example, if you’re a food manufacturer, batch tracking lets you track products for quality checks and recalls.
Real-time updates so you always know what’s in stock, where it’s located and how much you have left.
2. Assembly Management
With a WMS assembling is easy. The system tracks individual components as they’re used to build kits or bundles and updates stock levels automatically.
Take a furniture manufacturer as an example. When a customer orders a flat-pack desk the WMS ensures all the components—from screws to tabletops—are accounted for and deducted from inventory in real time. This reduces errors and saves time.
3. Picking and Packing
For manufacturers with a central warehouse, a WMS simplifies the picking and packing process. Advanced systems support wave picking and zone picking which speeds up and reduces mistakes.
For example, a toy manufacturer might have orders ranging from single items to bulk shipments. A WMS lets pickers organise and fulfil those orders without wasting time or making mistakes.
Read the case study: Heebie Jeebies Quadruples in Size
4. Sync Multiple Sites
Managing inventory across multiple sites becomes easy with a WMS. The system gives you a single view of stock levels so you can allocate resources where they’re needed most.
Imagine a medical device manufacturer. If a critical component is low at the main warehouse the WMS can quickly identify another site with stock and facilitate a transfer. No production delays and everything keeps moving.
5. Reduce Waste
A WMS minimises waste by ensuring older stock is used first. Automated tracking of expiration dates and stock rotation so materials don’t sit idle until they’re no longer usable.
In industries like food and beverage where shelf life is key, this can save big and reduce environmental impact.
6. Meet Deadlines Every Time
Delivery is critical in manufacturing. A WMS ensures everything from picking to dispatch runs smoothly so your products get to customers on time.
For example, an automotive parts manufacturer can use a WMS to prioritise urgent orders and allocate resources effectively. Real-time tracking lets them see order progress and fix issues before they cause delays.
Benefits You Can See
A WMS doesn’t just fix problems it delivers results. Here are the benefits manufacturers can expect:
- 50% More Efficient: Automation and streamlined processes save time and reduce manual labour.
- 99% Inventory Accuracy: No more costly mistakes and stock discrepancies.
- 50% Labour Savings: Get your team working on high-value tasks, not repetitive tasks.
What to Look for in Manufacturing Warehouse Management Systems
Choosing the right WMS is key. Here’s what to consider:
- Batch and Serial Number Tracking: Must have for traceability and compliance.
- Assembly Management: Look for features that track components and finished goods.
- Scalability: Your WMS should grow with your business.
- Integration: Make sure it integrates with your existing tools like accounting or enterprise resource planning software.
- Usability: A simple interface means less training time and faster adoption.
Conclusion
Manufacturing supply chains are complex but they don’t have to be complicated. With the right WMS, you can streamline, reduce waste and meet deadlines every time.
Datapel’s warehouse management system is designed to help manufacturers like you tackle that. With real-time inventory management, assembly management and multi-site synchronisation, Datapel’s WMS lets your business thrive.
Ready to take the next step? Learn more about how Datapel can revolutionise your manufacturing supply chain today.
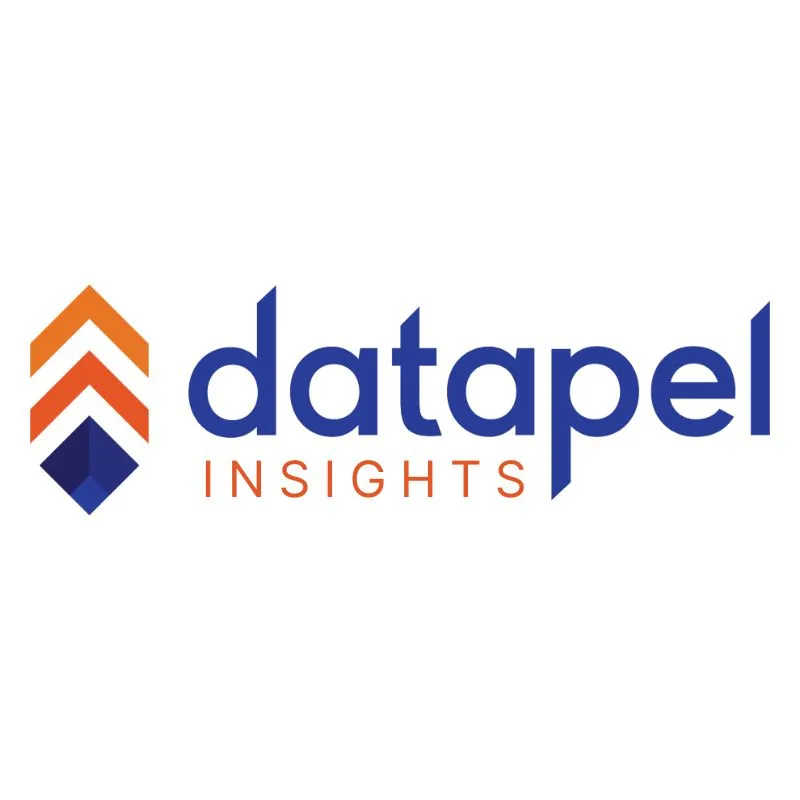
In my role, I oversee the development of insightful blogs that delve into the intricacies of warehouse management. Each piece reflects my dedication to empowering businesses through informative content. Through my team’s extensive experience in the industry, we aim to bring clarity to the complexities of WMS, helping businesses make informed decisions.
Join me on a journey through the ever-evolving landscape of warehouse technology as we explore the latest trends, industry insights, and practical tips to streamline your operations. Feel free to connect, and let’s embark on a collaborative exploration of how WMS can redefine your business efficiency.
Cheers to innovation, efficiency, and the exciting world of warehouse management!