Streamlining Consumable Inventory Management for SMBs
Contents
For small and medium-sized businesses (SMBs), the track and managing consumable inventory efficiently is not just a necessity—it’s a strategic advantage. Consumables, the items used and replaced regularly within your operations, from office supplies to manufacturing materials, can significantly impact your bottom line and operational efficiency if not managed properly.
This guide explores the essence of consumable inventory management and introduces Datapel’s Warehouse Management System (WMS) as a pivotal tool for SMBs aiming to enhance inventory control, reduce costs, and boost efficiency.
Understanding Consumable Inventory
Consumable inventory refers to any items that are regularly used up and need frequent replenishment. These range from day-to-day office supplies to essential operational equipment and raw materials in manufacturing processes. The main challenge with consumables lies in maintaining an optimal stock level: too much inventory ties up valuable resources, while too little can halt your operations.
Effective Strategies for Managing Consumables
Implementing efficient practices for packaging and consumable inventory management is essential for small and medium-sized businesses (SMBs) aiming to streamline operations and enhance cost-effectiveness. Here’s a deeper dive into six strategic approaches tailored for SMBs:
1. Centralise Inventory Data
A unified system for tracking inventory data is crucial. Such a system not only simplifies the monitoring of stock levels but also ensures accuracy in predicting reorder times. When all raw materials and consumable inventory information is accessible in one place, it eliminates the confusion and inefficiencies associated with disparate data sources.
This unified approach ensures that everyone within the organisation, from procurement to operations, has access to the same up-to-date information, fostering a more cohesive and informed decision-making process.
2. Embrace FIFO (First-in, First-out)
The FIFO method is particularly effective for managing perishable or time-sensitive consumables and food. By using the oldest stock first, businesses can significantly reduce waste and avoid the financial impact of having to write off stock due to obsolescence or expiry.
This practice not only conserves resources but also promotes a more sustainable approach to inventory management. Implementing FIFO requires meticulous tracking and organisation of stock, ensuring that items are used in the order they are received.
3. Conduct Regular Audits
Regular, manual audits of inventory are essential for maintaining accuracy in stock levels and understanding consumption patterns. These audits can reveal discrepancies between physical stock and paper inventory records, highlighting areas for improvement in both ordering and stock management processes.
By identifying these discrepancies, businesses can adjust their inventory practices to better match actual needs, ensuring that they are neither overstocking nor understocking consumables.
4. Set Intelligent Reorder Points
Determining and setting reorder points for each consumable ensures that stock is replenished just in time, avoiding interruptions in operations due to stock shortages and reducing the risk of overstocking. Automated alerts for low stock levels can be established through inventory management systems, allowing for timely reordering.
This strategy requires a good understanding of consumption rates and lead times for each item consumed, ensuring that reorder points are set at levels that maintain operational efficiency without tying up unnecessary capital in excess inventory.
5. Optimise Supplier Relationships
For SMBs, strong relationships with suppliers are a cornerstone of efficient consumable inventory management. These relationships can lead to better pricing, more reliable stock availability, and flexible delivery schedules, which are invaluable for managing the flow of consumables.
Regular communication and negotiation with suppliers and manufacturers can also open up opportunities for bulk-purchasing discounts or more favourable payment terms, further enhancing cost efficiency and inventory flexibility.
6. Implement Inventory Management Software
The adoption of inventory management software revolutionises the way consumables are tracked, ordered, and analysed. Such technology automates many of the manual processes involved in inventory management, from tracking inventory and updating stock levels in real-time to predicting future inventory needs based on historical consumption patterns.
This reduces the likelihood of human error and frees up staff to focus on more strategic tasks. Additionally, advanced inventory management systems often offer integration with other business systems, providing a holistic view of business operations and facilitating more informed decision-making across the organisation.
By adopting these strategies, SMBs can significantly improve their management of consumable store inventory, leading to reduced costs, improved operational efficiency, and enhanced overall business performance.
Environmental Considerations and Sustainability in Consumable Inventory Management
In the quest for efficiency and cost reduction in consumable inventory management, small and medium-sized businesses (SMBs) also face the pressing challenge of environmental responsibility.
Sustainability in inventory management is not just about meeting regulatory requirements or bolstering a company’s green credentials; it’s increasingly recognised as a strategic approach that can drive long-term savings, enhance brand reputation, and contribute to global environmental conservation efforts.
Adopting Eco-Friendly Consumables
One of the first steps towards sustainable inventory management is the selection of eco-friendly consumables. This means prioritising products that are made from recycled materials, have a lower environmental impact during production and use and can be recycled or disposed of safely after use.
For example, choosing biodegradable cleaning supplies or recycled paper products can significantly reduce a business’s carbon footprint.
Reducing Waste Through Efficient Management
Efficient inventory management plays a crucial role in waste reduction. By adopting practices such as the First-In, First-Out (FIFO) method and setting accurate reorder points, SMBs can ensure that consumables are used before they expire or become obsolete, minimising waste.
Additionally, regular audits of consumable inventory can help identify areas where waste can be reduced, such as overordering or the use of unnecessarily high-specification materials for simple tasks.
Recycling and Repurposing
SMBs can further their commitment to sustainability by implementing recycling and repurposing initiatives for their consumable inventory. Encouraging the segregation of waste and setting up recycling stations can facilitate the recycling of paper, plastics, and metals.
Moreover, businesses can explore opportunities to repurpose items that are no longer needed or have been partially used. For example, partially used office supplies could be donated to local schools or community centres, extending their lifecycle and supporting the community.
Elevating SMB Success with Datapel
Datapel’s Warehouse Management System is designed with the needs of SMBs in mind, offering a powerful yet user-friendly solution for consumable inventory management.
With Datapel, you can:
- Centralise Your Inventory Management: Keep all your consumable inventory data in one place, accessible to your team anywhere, anytime. This streamlines operations and enhances decision-making.
- Automate Reordering: Set up automatic reorder points within Datapel to ensure you never run out of key consumables. This system helps maintain optimal inventory levels without manual intervention.
- Access In-depth Reporting: Datapel provides detailed reports on inventory usage, costs, and turnover rates, offering valuable insights for more informed purchasing decisions.
- Seamlessly Integrate: Datapel integrates with a wide range of business systems, including accounting and eCommerce platforms, offering a comprehensive view of your business operations and inventory needs.
For SMBs, managing consumable inventory effectively is crucial for sustaining operations and supporting growth. By adopting strategic inventory management practices and leveraging the services of Datapel’s WMS, businesses can achieve significant efficiency gains, cost savings, and improved inventory control.
Datapel empowers SMBs to focus on what they do best, secure in the knowledge that their consumable inventory is optimally managed.
FAQ’s
1. What is consumable inventory, and why is it important for SMBs?
Consumable inventory refers to items like office supplies and manufacturing materials that need regular replacement. It’s vital for SMBs as efficient management affects costs and operational smoothness.
2. How can Datapel’s WMS help SMBs manage their consumable inventory more effectively?
Datapel’s WMS streamlines inventory management by centralising data, automating reorders, and offering detailed reports. This helps keep stock levels optimal and reduces manual work.
3. What are some common challenges in managing consumable inventory for SMBs?
SMBs often struggle with overstocking, understocking, and scattered inventory data, which can lead to wasted resources and operational disruptions.
4. How does the FIFO method improve consumable inventory management?
FIFO, or using the oldest stock first, reduces waste by preventing the expiry of perishable goods, making inventory management more sustainable.
5. How often should SMBs conduct inventory audits, and why?
Regular audits help maintain accurate stock levels and reveal consumption patterns, ensuring SMBs adjust inventory practices to meet actual needs and avoid over or understocking.
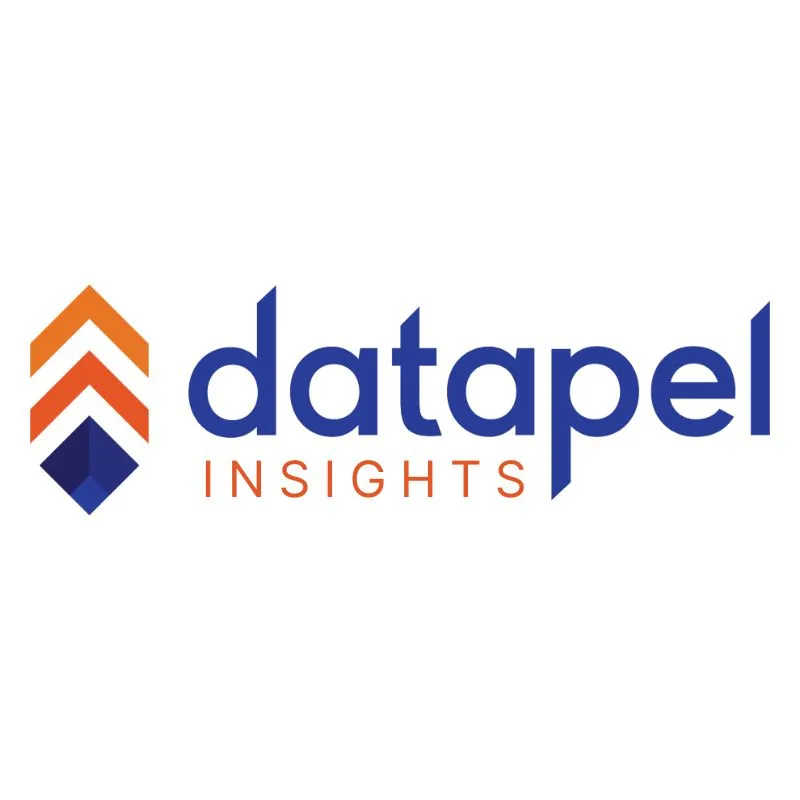
In my role, I oversee the development of insightful blogs that delve into the intricacies of warehouse management. Each piece reflects my dedication to empowering businesses through informative content. Through my team’s extensive experience in the industry, we aim to bring clarity to the complexities of WMS, helping businesses make informed decisions.
Join me on a journey through the ever-evolving landscape of warehouse technology as we explore the latest trends, industry insights, and practical tips to streamline your operations. Feel free to connect, and let’s embark on a collaborative exploration of how WMS can redefine your business efficiency.
Cheers to innovation, efficiency, and the exciting world of warehouse management!