Unlocking Warehouse Efficiency: Signs It’s Time for a Powerful WMS Solution
Contents
Welcome to our comprehensive guide on the signs that indicate it’s time for your business to implement a Warehouse Management System (WMS). In this article, we will explore the key indicators that highlight the need for an efficient WMS solution. By identifying these signs and taking appropriate action, you can streamline your warehouse operations, improve inventory management, and achieve better overall efficiency.
The Challenges of Manual Warehouse Management
As your business grows and your warehouse operations become more complex, relying on manual processes for warehouse management can become increasingly burdensome. Let’s examine the challenges you may encounter without a robust Warehouse Management System in place.
1. Inventory Inaccuracies and Discrepancies
Manual inventory management often leads to inaccuracies and discrepancies in stock levels. Tracking inventory manually is prone to human error, resulting in differences between the recorded inventory and actual stock on shelves. These inaccuracies can lead to stockouts, overstocking, dissatisfied customers, and financial losses.
2. Inefficient Order Fulfillment
Without a centralised system to manage warehouse operations, order fulfilment can become time-consuming and prone to errors. Manually locating products, updating inventory records, and processing orders can lead to delays and mistakes. Inefficient order fulfilment not only affects customer satisfaction but also hampers overall operational efficiency.
3. Limited Visibility and Insights into Warehouse Performance
Gaining real-time visibility and insights into your warehouse performance is crucial for making informed business decisions. Manual processes make it challenging to track key metrics such as inventory turnover, order cycle times, and picking accuracy. Without comprehensive visibility, it becomes difficult to optimise warehouse processes, identify bottlenecks, and implement improvements.
4. Increased Labor and Time for Manual Replenishment
Determining when and how much to replenish manually can be a labour-intensive and time-consuming task. Without accurate and real-time data, you may face challenges in maintaining optimal stock levels. Inefficient manual replenishment processes can lead to wasted labour, excess carrying costs, and increased risk of stockouts or overstocking.
5. Lack of Integration and Data Consistency
When warehouse management processes are disconnected from other systems, it creates inefficiencies and data inconsistencies. Manual data entry and transfer between different systems increase the risk of errors and waste valuable time. Lack of integration with other software, such as e-commerce platforms or inventory management systems, can lead to duplicated efforts and hinder productivity.
The Solution: Implementing a Warehouse Management System (WMS)
To overcome the challenges posed by manual warehouse management, it is essential to adopt a comprehensive Warehouse Management System. Let’s explore the key benefits you can expect by implementing a WMS solution:
1. Real-time Inventory Tracking and Accuracy
A robust Warehouse Management System provides real-time visibility into inventory levels and locations. By leveraging barcode scanning and automation, you can accurately track inventory movements, reduce errors, and maintain accurate stock records. This level of control empowers you to fulfil customer orders promptly and minimise stock discrepancies.
2. Streamlined Order Fulfillment Process
With a WMS, you can streamline and automate your order fulfilment processes. Features such as automated picking instructions optimised picking routes, and real-time inventory updates enable efficient order fulfilment. By minimising manual tasks, you can improve order accuracy, reduce processing time, and enhance customer satisfaction.
3. Enhanced Warehouse Visibility and Analytics
A Warehouse Management System offers comprehensive reporting and analytics capabilities, providing insights into warehouse performance. You can track key metrics, such as order cycle times, pick accuracy rates, and resource utilisation. These insights help you identify areas for improvement, optimise warehouse layout, and make data-driven decisions to boost operational efficiency.
4. Efficient Replenishment and Stock Management
By implementing a Warehouse Management System, you can automate and optimise replenishment processes. The system can generate automatic replenishment suggestions based on real-time data and predefined rules. This ensures optimal stock levels, reduces manual labour, and prevents stockouts or overstocking. Efficient replenishment enables you to meet customer demand while minimising carrying costs.
5. Seamless Integration with Other Systems
An advanced WMS integrates seamlessly with other business systems such as ERP software, eCommerce platforms, or accounting systems. This integration eliminates data silos, improves data consistency, and streamlines workflows across different departments. It enables seamless data exchange, eliminates manual data entry, and improves productivity.
Steps to Implementing a WMS
Implementing a WMS can be a complex process, but it’s worth the effort. Here are the steps you should follow to implement a WMS:
1. Evaluate your current warehouse operations and identify areas for improvement.
2. Research WMS providers and choose one that fits your business needs.
3. Develop a plan for implementing the WMS, including training employees and integrating it with your existing systems.
4. Test the WMS before rolling it out to ensure it works as expected.
5. Train employees on how to use the WMS effectively.
6. Monitor the WMS to ensure it continues to meet your business needs and make adjustments as necessary.
Best Practices for Optimising Your WMS
Once you’ve implemented a WMS, there are several best practices you can follow to optimise its performance. These include:
1. Regularly review and analyse data to identify areas for improvement.
2. Train new employees on how to use the WMS effectively.
3. Regularly update your WMS to ensure it stays up-to-date with the latest features and security patches.
4. Optimize your inventory management by regularly reviewing stock levels and adjusting as necessary.
5. Continually monitor and adjust your workforce to ensure you have the right staffing levels for your business needs.
Choosing the Right WMS for Your Business
When choosing a WMS for your business, it’s important to consider your business needs and the features that are most important to you. Some of the factors you should consider include:
1. The size of your business and the number of products you sell.
2. The complexity of your warehouse operations.
3. The level of integration you need with your existing systems.
4. The cost of the WMS and the return on investment you can expect.
Additionally, it’s important to choose a WMS provider that offers excellent customer support. You want to make sure you can get help quickly if you run into any issues with the WMS.
Conclusion
In conclusion, implementing a Warehouse Management System (WMS) is crucial for businesses experiencing the challenges of manual warehouse management. By embracing an advanced WMS solution, you can optimise your warehouse operations, improve inventory accuracy, and achieve better overall efficiency.
A Warehouse Management System offers real-time visibility into inventory, streamlines order fulfilment, provides insights into warehouse performance, and automates replenishment processes. By centralising data, reducing errors, and improving productivity, you can enhance customer satisfaction, reduce costs, and gain a competitive advantage.
Take action today and empower your business with a WMS. Streamline your warehouse operations, improve inventory management, and unlock new opportunities for growth and success.
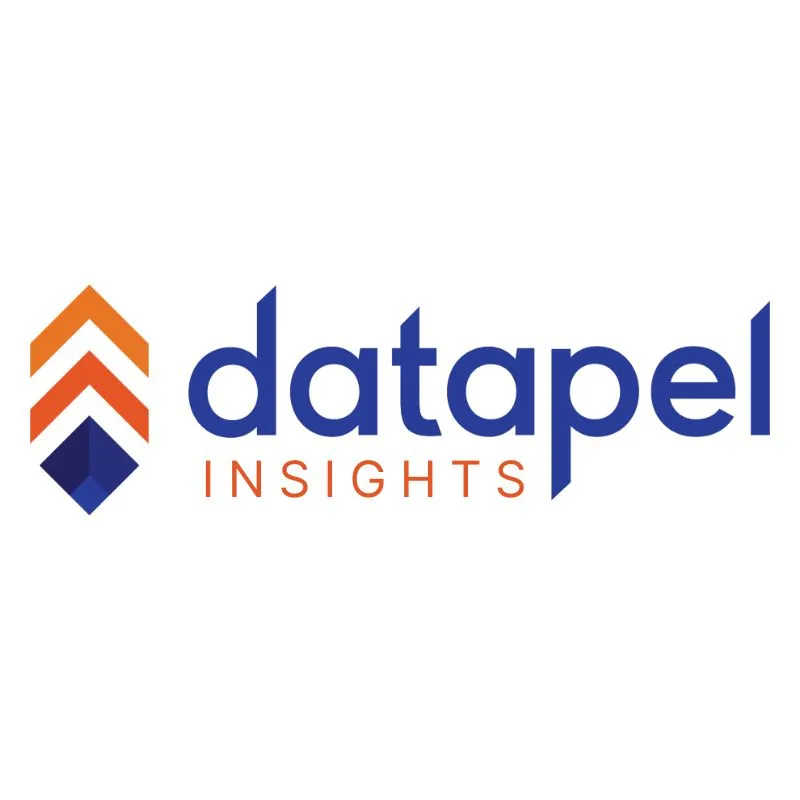
In my role, I oversee the development of insightful blogs that delve into the intricacies of warehouse management. Each piece reflects my dedication to empowering businesses through informative content. Through my team’s extensive experience in the industry, we aim to bring clarity to the complexities of WMS, helping businesses make informed decisions.
Join me on a journey through the ever-evolving landscape of warehouse technology as we explore the latest trends, industry insights, and practical tips to streamline your operations. Feel free to connect, and let’s embark on a collaborative exploration of how WMS can redefine your business efficiency.
Cheers to innovation, efficiency, and the exciting world of warehouse management!