How to Avoid Negative Inventory
Contents
Negative inventory means your system shows less stock than you have. This causes problems. In this article, we’ll cover negative inventory, its causes and how to prevent it. Knowing this will help you keep your operations running smoothly and avoid costly mistakes.
Quick Facts
- Negative inventory is when stock records show levels below zero, often due to timing issues, production problems or multi-location challenges.
- To prevent negative inventory you need a reliable inventory management system, regular inventory counts and employee training on inventory procedures.
- Using technology like real-time inventory monitoring, automation and integration with accounting software will reduce the risk of negative inventory and overall inventory accuracy.
Introduction
Inventory management is key to any business that wants to make more profit while minimising inventory investment and maximise customer satisfaction. This is not a goal but a necessity for operational success and sustainability in real business. However, it is important to caution against embracing negative inventory as an actual business practice, as it can hurt business decisions and overall management.
When inventory management is not done well it can lead to:
- Stock-outs that hamper production and delay delivery
- Disruptions that affect customer satisfaction
- Negative impact to the bottom line
Tools like Datapel’s cloud inventory platform is designed for manufacturers to have control over their stock and production schedule.
Having a single system to monitor all sales channels is beneficial for direct-to-consumer manufacturers as it simplifies management and tracks inventory levels accurately.
Understanding negative inventory is key to business integrity. It helps you identify and correct discrepancies before they become bigger problems. This understanding is the foundation for good inventory management practices that prevent negative balances and operational efficiency.
What is Negative Inventory
Negative inventory is when your inventory records show a stock level below zero. This anomaly will cause big problems to your business and management must understand this.
Negative inventory can lead to discrepancies in the company’s inventory records, affecting financial reporting and profit margins.
Maintaining a balanced inventory is crucial for any business. It helps not only in profit maximisation but also in customer satisfaction. Understanding the causes and effects of negative inventory is key to business integrity and no disruptions.
Root Causes of Negative Inventory
In most cases negative inventory can be attributed to three main causes: timing discrepancies, production inconsistencies and multi-location issues. Negative inventory issues often occur when demand exceeds supply, leading to backlogs and customer dissatisfaction. Here are the details:
- Timing issues when sales orders and inventory updates are not in sync resulting to negative balances.
- Production discrepancies due to not accounting for scrap, batch tracking and byproducts resulting to inventory inaccuracies.
- Multi-location issues when sales are recorded from the wrong store or products are delivered to the wrong warehouse.
Timing
Timing discrepancies is one of the main cause of negative inventory. This happens when sales transactions are recorded before inventory updates are made resulting to negative inventory balance. For example if an order is marked as shipped before the stock is available it will create a negative balance in the inventory system.
This is common in retail where orders are marked as shipped even though the process has not started or there are not enough items in the warehouse.
Production Discrepancies
Production discrepancies can cause big impact on inventory. Not accounting for scrap or byproducts in the production process can lead to negative inventory. In manufacturing negative inventory often happens when production records do not match the actual items produced resulting to ghost inventory. Accurate production statistics are crucial in verifying actual production quantities and avoiding negative inventory. This will cause inefficiencies in the supply chain, procurement, production and distribution.
Duplicate manufacturing orders or unclear production bills can also cause negative inventory. To avoid negative inventory, address these issues as soon as possible.
Multi-Location Issues
Managing inventory across multiple locations has several challenges that can cause negative inventory. Some of these are:
- Mistakes in recording sales from the wrong store location
- Delivering products to the wrong store
- Big differences in on-hand inventory data
These are common in businesses with multiple warehouses where inventory management is critical.
For example Apple stores sometimes have negative inventory due to discrepancies between system stock and on-hand items during new product launches which can be seen in their production stats.
Effects to Business Operations
Negative inventory can go deep into business operations. It can disrupt operations by causing stockouts or overstocks both of which will increase operational costs. Disrupted operations due to negative inventory can result to stockouts which will lead to lost sales and damaged customer relationships. Inaccurate inventory data will cause supply chain inefficiencies affecting procurement, production and distribution.
Also negative inventory can cause financial reporting errors which will affect reported earnings and overall asset values. This will impair strategic decision making and lead to audit and compliance risks and inaccuracies in income and expense reports.
Financial Reporting Inaccuracies
Negative inventory can cause big distortions in financial statements and misstate asset values. It affects financial reporting by causing inaccuracies in cost of goods sold (COGS) calculation. Inventory inaccuracies from negative inventory can result to over or understated asset values in the balance sheet. These distortions will mislead stakeholders about the company’s financial health.
Ultimately negative inventory will lead to inaccurate financial reporting, wrong COGS calculation and lower profit margins.
Customer Satisfaction Issues
Unfulfilled orders or delays caused by negative inventory can have big impact on customer satisfaction. When a company can’t fulfil orders due to negative inventory it will lead to:
- Lost sales
- Customer dissatisfaction
- Damage to customer trust and loyalty
- Lower chance of repeat business
Immediate access to accurate inventory data will allow businesses to act fast to replenish stock through inventory purchases and avoid stockouts and customer satisfaction.
Operational Inefficiencies
Negative inventory can cause big operational inefficiencies. It can severely disrupt business operations by indicating deeper inventory control or record-keeping issues. These will increase storage costs and tie up capital in excess inventory.
Negative inventory figures will also impair strategic decision making by skewing analysis and lead to poor decisions on product lines or market opportunities. Auditors also look into inventory discrepancies and negative inventory can lead to audit findings or regulatory penalties.
How to Prevent Negative Inventory
To prevent negative inventory a multi-faceted approach is needed that includes reliable inventory management systems, regular inventory counts and staff training. Regular updates and maintenance of inventory management software is key to prevent glitches that will cause negative inventory. A reliable inventory management system can automate tracking and reduce human error.
Regular inventory counts is important to identify the discrepancies between the company’s inventory records and actual inventory levels. When discrepancies are found they can be addressed and corrected to ensure accurate inventory management. Enhanced training for all staff involved in inventory management will ensure proper handling and recording of inventory.
Reliable Inventory Management Systems
Modern inventory systems offers real-time updates and alerts when stock levels are low, will catch inventory discrepancies fast. Real-time inventory updates will ensure accurate inventory levels and smooth production flow.
Using a centralised Warehouse Management System (WMS) will ensure consistent inventory records and will avoid overselling and stockouts by providing real-time updates to inventory levels.
Regular Inventory Counts
Scheduled inventory audits and periodic physical counts will compare actual inventory with recorded levels, will address mismatches immediately. Regularly auditing sales data from all channels will ensure that inventory records are accurate so negative inventory will be prevented.
Employee Training on Inventory Procedures
Regular refresher training for staff will keep inventory management best practices on top of mind. Staff should be trained on inventory management procedures, data entry, inventory counting and use of inventory management system. This will ensure that all team members understand the importance of accurate inventory handling and the impact of negative inventory to the business.
Using Technology to Manage Inventory Levels
Inventory level management is heavily dependent on technology. Automation solutions will streamline and automate manual inventory processes and reduce the risk of negative inventory. Using inventory management software will improve data accuracy and inventory tracking and prevent discrepancies.
A master planner, an inventory tracking system, can track inventory transactions automatically and in real-time so inventory levels will always be accurate.
Real-Time Inventory Monitoring
Monitoring inventory levels in real-time is important because it will identify low inventory levels and prevent negative inventory and stockouts. Warehouse management systems (WMS) will provide real-time visibility to inventory levels and movements. Real-time visibility will prevent stockouts and overstock situations so products will always be available to meet customer demand.
Visibility through ERP integrations will streamline inventory management across multiple locations.
Automation in Inventory Management
Automated inventory systems will reduce manual entries and minimise errors and ensure accurate inventory records. Automation tools can set reorder alerts so stock will be replenished on time and prevent negative inventory.
Using barcode scanning during transfers will ensure accurate documentation of stock movement. Inventory management systems can automate the setting of reorder points so negative inventory will be reduced.
Integration with Accounting Software
Inventory systems integration with accounting software will ensure data consistency and reduce manual data transfer. This integration will support negative inventory tracking through platforms like MYOB and Xero.
Integrating sales platforms with inventory management systems will give you:
- Accurate stock levels
- Consistent stock information across multiple channels
- Automated billing, invoicing and payment processing
- Cash and accounts handling
- High accounting standards
Negative Inventory in Multi-Location Warehouses
Negative inventory in multi-location warehouses requires consistent monitoring, centralised management and precise stock transfers. Monitoring inventory levels at each location will identify discrepancies early. Having clear inventory management procedures across all locations will prevent negative inventory balances.
Inventory management across multiple locations can lead to negative inventory if mistakes are made.
Centralised Inventory Control
Centralised inventory management will give you:
- Consolidate all stock into one warehouse, easier to track and manage
- Improve inventory accuracy and streamline order fulfilment process
- Prevent overselling and stockouts by having real-time inventory levels
Accurate Stock Transfers
Strict documentation and verification process for stock transfers will ensure accuracy. Tracking stock transfers will prevent discrepancies between warehouse locations so each location will have the correct inventory levels.
Sales from Multiple Channels
Coordinating sales across multiple channels is important to prevent inventory discrepancies. Synchronising sales data from different channels will prevent over-selling and under-stocking so inventory levels will be accurate.
Real-Life Examples of Negative Inventory
Some of the world’s biggest companies have experienced negative inventory. Amazon had negative inventory during holiday seasons because of high demand for certain products. In 2018, Tesla had negative inventory for the Model 3 car because demand exceeded production capacity and customers had to wait for months.
Macy’s had negative inventory during 2015 holiday season and customers were unhappy because they couldn’t get the clothing items they wanted. Walmart had negative inventory when high-demand items were mis-recorded during peak season.
Conclusion
Negative inventory can affect business operations in many ways including financial reporting inaccuracies, customer dissatisfaction and operational inefficiencies. Knowing the root causes of negative inventory (timing issues, production discrepancies and multi-location challenges) is key to effective inventory management.
By having reliable inventory management system, conducting regular inventory counts and thorough employee training, businesses can prevent negative inventory and maintain operational efficiency. Using technology such as real-time inventory monitoring and automation will further improve inventory accuracy and prevent negative balances. Proactive inventory management is key to business success and customer satisfaction.
FAQs
What is negative inventory?
Negative inventory is when the recorded quantity of an item in stock is a negative number, meaning the stock is short for that item. It’s when the available stock of an item is less than zero in the records.
How does negative inventory affect financial reporting?
Negative inventory will result to financial reporting inaccuracies, will affect the calculation of cost of goods sold and valuation of assets and will mislead stakeholders about the company’s financial situation.
What are the common causes of negative inventory?
Common causes of negative inventory are returns not handled properly, supplier delivery mistakes, too many returns, production problems, data entry errors and damaged goods. Be mindful of these to avoid negative inventory.
How can technology help?
Technology can help by improving data accuracy, providing real-time updates and streamlining tracking to prevent discrepancies. This includes inventory management software and automation tools.
How to prevent negative inventory?
Prevent negative inventory by having reliable inventory management system, conduct regular inventory counts, train employees, use technology for real-time monitoring and ensure accurate stock transfers in multi-location warehouses.
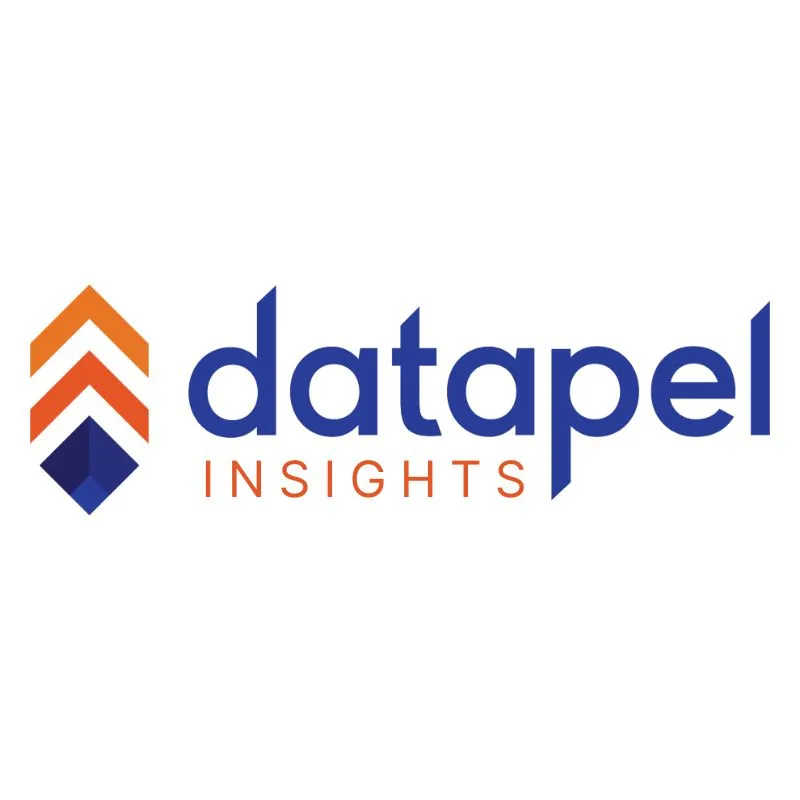
In my role, I oversee the development of insightful blogs that delve into the intricacies of warehouse management. Each piece reflects my dedication to empowering businesses through informative content. Through my team’s extensive experience in the industry, we aim to bring clarity to the complexities of WMS, helping businesses make informed decisions.
Join me on a journey through the ever-evolving landscape of warehouse technology as we explore the latest trends, industry insights, and practical tips to streamline your operations. Feel free to connect, and let’s embark on a collaborative exploration of how WMS can redefine your business efficiency.
Cheers to innovation, efficiency, and the exciting world of warehouse management!